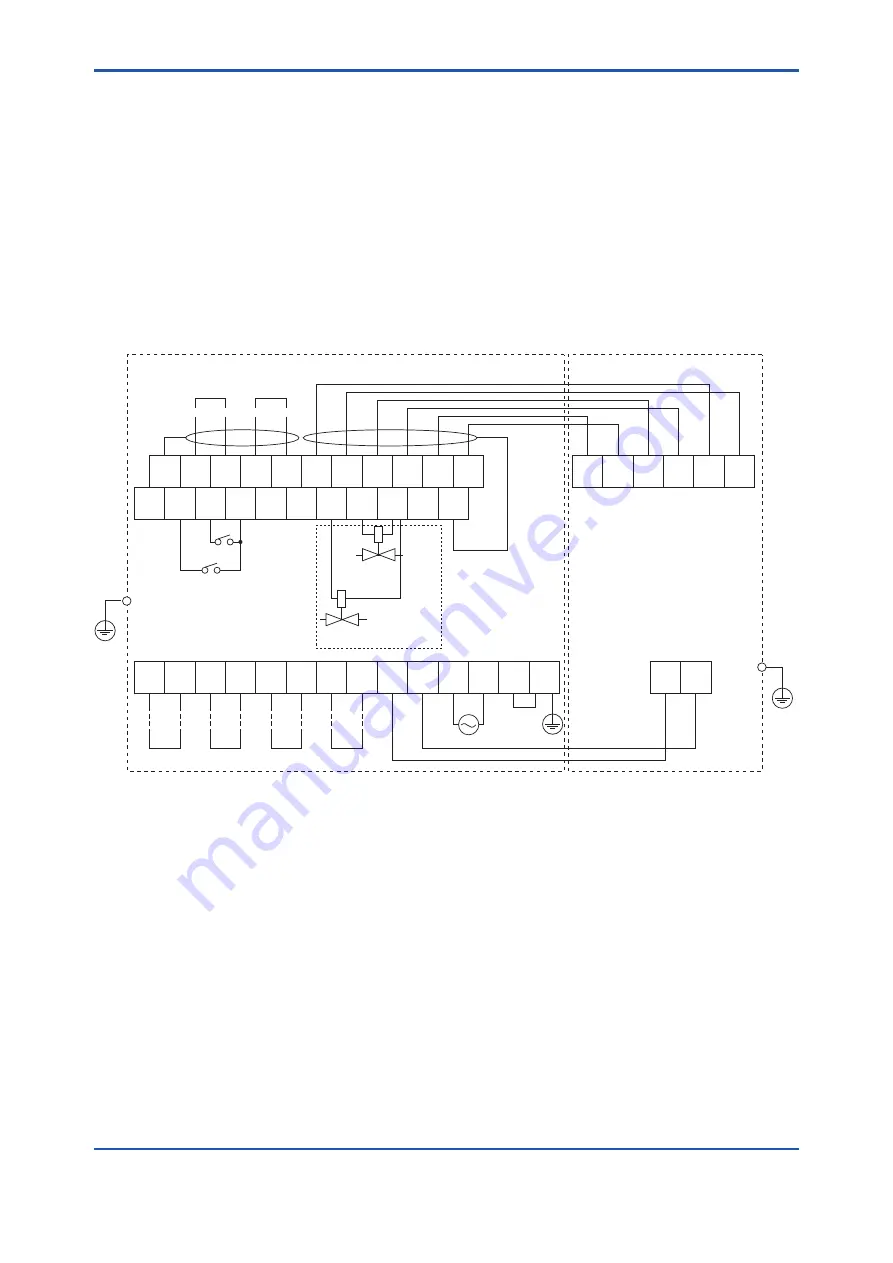
<4. WIRING>
4-2
IM 11M03A02-00E
4.1.2
Wiring Procedure
Wiring should be performed according to the following procedure:
1. Be sure to connect the shield line to FG terminal of the converter.
2. The outer sheath of the signal line should be stripped to a length of 50 mm or less. The most
outer sheath of the power cable should be stripped to a length of 20 mm or less.
3. Signals may be affected by noise if signal lines, power cable and heater cable are located in
the same conduit. When using conduit, signal lines should be installed in a separate conduit
than power and heater cables.
4. Install metal blind plug(s) in unused cable connection gland(s) of the converter.
5. Metal conduit should be grounded.
1
FG
2
AO1
(+)
3
AO1
(-)
4
AO2
(+)
5
AO2
(-)
6
CJ
(+)
7
CJ
(-)
8
TC
(+)
9
TC
(-)
10
CELL
(+)
11
CELL
(-)
12
FG
13
DI-1
14
DI-2
15
DI-C
16
AI
(+)
17
AI
(-)
18
AC-
ZERO
19
AC-
SPAN
20
AC-
COM
21
FG
22
FG
CELL
(+)
CELL
(-)
TC
(+)
TC
(-)
CJ
(+)
CJ
(-)
23
DO-1
24
DO-1
25
DO-2
26
DO-2
27
DO-3
28
DO-3
29
DO-4
30
DO-4
31
HTR
32
HTR
33
L
34
N
35
G
36
FG
HTR HTR
100-240V AC
50/60 Hz
F4.1E.ai
Model ZR402G Separate type Zirconia Oxygen Analyzer/
Converter
Zirconia Oxygen Analyzer,
Model ZO21DW Detector
Analog
output 2
Analog
output 1
4-20 mA DC
4-20 mA DC
Digital output
Contact
input 2
Contact input 1
Contact
output 1
Contact
output 2
Contact
output 3
Contact
output 4
Solenoid valve for span gas
for automatic calibration
Solenoid valve for zero gas
for automatic calibration
Flow setting unit
*1
*1
The protective grounding for the converter should be connected to either the protective ground terminal in the equipment or
the ground terminal on the case.
Grounding standard: JIS D type (Class 3 grounding), ground resistance: 100
Ω
or less.
*1
Figure 4.1
Wiring connection to the converter (ZR402G)
Summary of Contents for ZO21DW
Page 11: ...Blank Page...
Page 25: ...Blank Page...
Page 27: ...Blank Page...
Page 37: ......
Page 39: ...Blank Page...