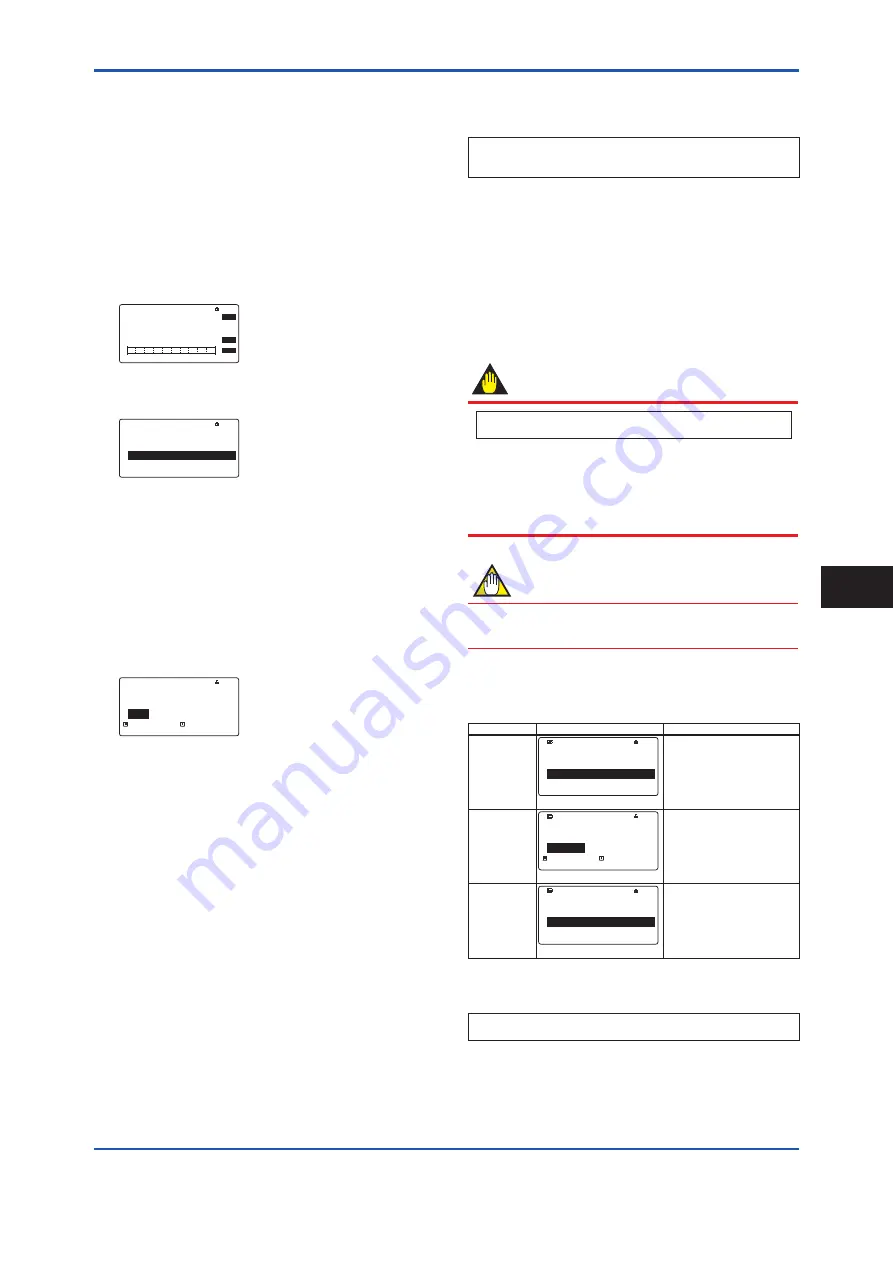
<5. Basic Operating Procedures>
51
IM 01E24A01-01EN
5.3 Display Mode and Setting
Mode
The device runs in the Display Mode when the power
is turned on. For check or change of parameters, the
Setting Mode must be activated. The following procesure
explains how to change to the Setting Mode. For the
function of IR switches, read Subsection 5.2.1.
[Procedure]
1) Turn on the power and wait for several seconds to
move to display mode.
F0513.ai
0.00000m/s
0.00000
l/min
00 : 00
PRV
VEL
FLB
SET
SFT
INC
2) Keep touching [SET] switch for two seconds. The
screen moves to the menu of Operation Level.
F0514.ai
Operation level
Maintenance
Specialist
Exit
▲
▼
00 : 00
SET
SFT
INC
3) Select an appropreate operation level by moving the
cursor with [INC] or [DEC] switch.
Passcode is not necessary for “Operator”. For
“Maintenance” and “Specialist”, passcode is
necessary for each.
For passcode setting, [SFT] is for position change,
and [INC] is for number, then twice [SET] is for entry
completion.
The default passcode at the factory shipment is set to
“0000”.
F0515.ai
Pass code
****
0000
0000
9999
00 : 00
SET
SFT
INC
4) When the Operation Level is determined, the screen
moves to “Device setup” as the Setting Mode where
parameters can be configured.
5) After completing parameter setting, push [ESC]
switch. The screen returns to the Display Mode.
[Passcode Confirmation and Change]
The confirmation and change of the passcode are
allowed only by parameter setting from the display unit.
Display Menu Path:
Device setup ► Detailed setup ► Access cfg ► Chg mainte
Device setup ► Detailed setup ► Access cfg ► Chg special
(1) Passcode for “Maintenance” operation level
To change the passcode (Maintenance code),
“Maintenance” or “Specialist” as the operational level
is required.
(2) Passcode for “Specialist” operation level
To change the passcode (Specialist code),
“Maintenance” or “Specialist” as the operational level
is required.
IMPORTANT
Display Menu Path:
Device setup ► Wizard
When parameters are changed in the Wizard of
Easy setup, “Setting download” in the menu of
each parameter must be executed after parameter
is changed. Without the execution, any parameter
changed is not stored into the device.
NOTE
If 10 minutes past without operation in the Setting
Mode, the screen goes back to the Display Mode.
Parameter form
There are three types of parameter form below.
Type
Example of display
Contents
Select type
F0516.ai
Unit
m
3
l(liter)
cm
3
▲
▼
00 : 00
SET
SFT
INC
Select the adequate data
from among alternatives
which are detemined in
advance.
Numeric type
F0517.ai
Span
+7200.00
+2200.00
+0.00001 +999999
00 : 00
SET
SFT
INC
Specify the data with a
combination of number and a
decimal point into each digit.
Alphanumeric
type
F0518.ai
Tag No
FT-1234
FT-1234
00 : 00
SET
SFT
INC
Configure the data with a
combination of alphanumeric
characters. (Tag No., Special
unit, etc…)
The alphanumeric type indicates alphanumeric
characters in the following order.
0123456789ABCDEFGHIJKLMNOPQRSTUVWXYZabcdefghijklmnopqrstu
vwxyz!"#$%&'()*+,-./:;<=>?@[\]^_`{|}~"space"
Basic Operating Procedures
5