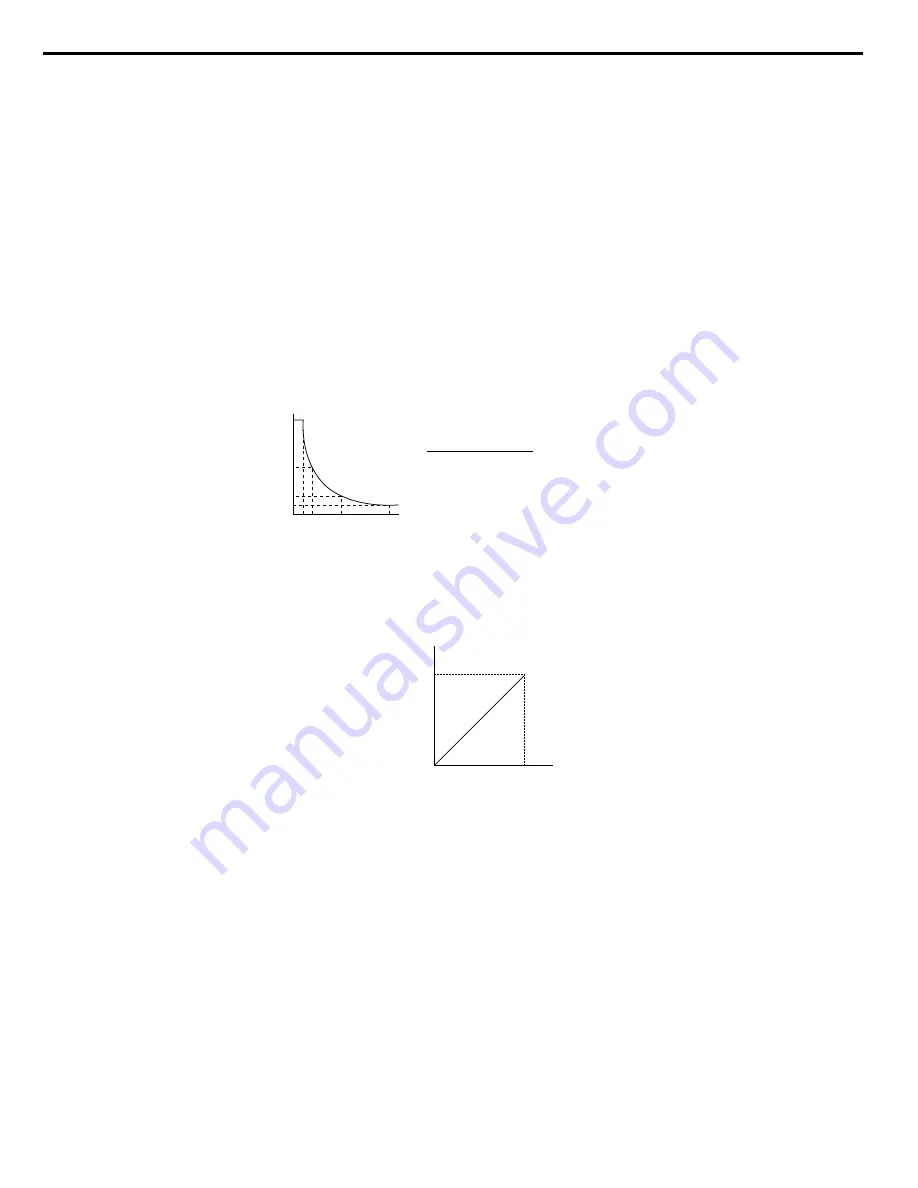
Example: If the analog frequency reference from analog input terminal A1 is 80% and a gain of 50% is applied from analog
input terminal A2, the resulting frequency reference will be 40% of the maximum output frequency.
Setting 2: Auxiliary Reference 1
Sets the auxiliary frequency reference 1 when multi-step speed operation is selected.
Refer to Multi-Step Speed Selection on
for details.
Setting 3: Auxiliary Reference 2
Sets the auxiliary frequency reference 2 when multi-step speed operation is selected.
Refer to Multi-Step Speed Selection on
for details.
Setting 4: Output Voltage Bias
Voltage bias boosts the output voltage of the V/f curve as a percentage of the maximum output voltage (E1-05). Available
only when using V/f Control.
Setting 5: Accel/Decel Time Gain
Adjusts the gain level for the acceleration and deceleration times set to parameters C1-01 through C1-08.
The drive acceleration time is calculated by multiplying the gain level to C1-
oo
as follows:
C1-
oo
× Accel/decel time gain = Drive accel/decel time
100%
50%
0
5 V
10 V
1V 2V
20%
10%
Acceleration/deceleration gain from 1 to 10 V
(10 V)
Input Voltage (V)
×
10 (%)
=
Figure 1.54 Accel/Decel Time Gain with Analog Input Terminal
Setting 6: DC Injection Braking Current
The current level used for DC Injection Braking is set as a percentage of the drive rated current.
Drive Rated
Current
0
(4)
100%
10 V
(20 mA)
DC Injection Braking Current Level
Figure 1.55 DC Injection Braking Current Using an Analog Input Terminal
Setting 7: Torque Detection Level
Using this setting, the overtorque/undertorque detection level for torque detection 1 (L6-01) can be set by an analog input.
The analog input replaces the level set to L6-02. An analog input of 100% (10 V or 20 mA) sets a torque detection level equal
to 100% drive rated current/motor rated torque. Adjust the analog input gain if higher detection level settings are required.
Refer to L6: Torque Detection on page 120
for details on torque detection.
Setting 8: Stall Prevention Level
Allows an analog input signal to adjust the Stall Prevention level.
shows the setting characteristics. The drive will
use the lower value of the Stall Prevention level set to L3-06 or the level coming from the selected analog input terminal.
1.7 H: Terminal Functions
102
YASKAWA ELECTRIC SIEP C710636 10C Z1000U HVAC MATRIX Drive Programming Manual