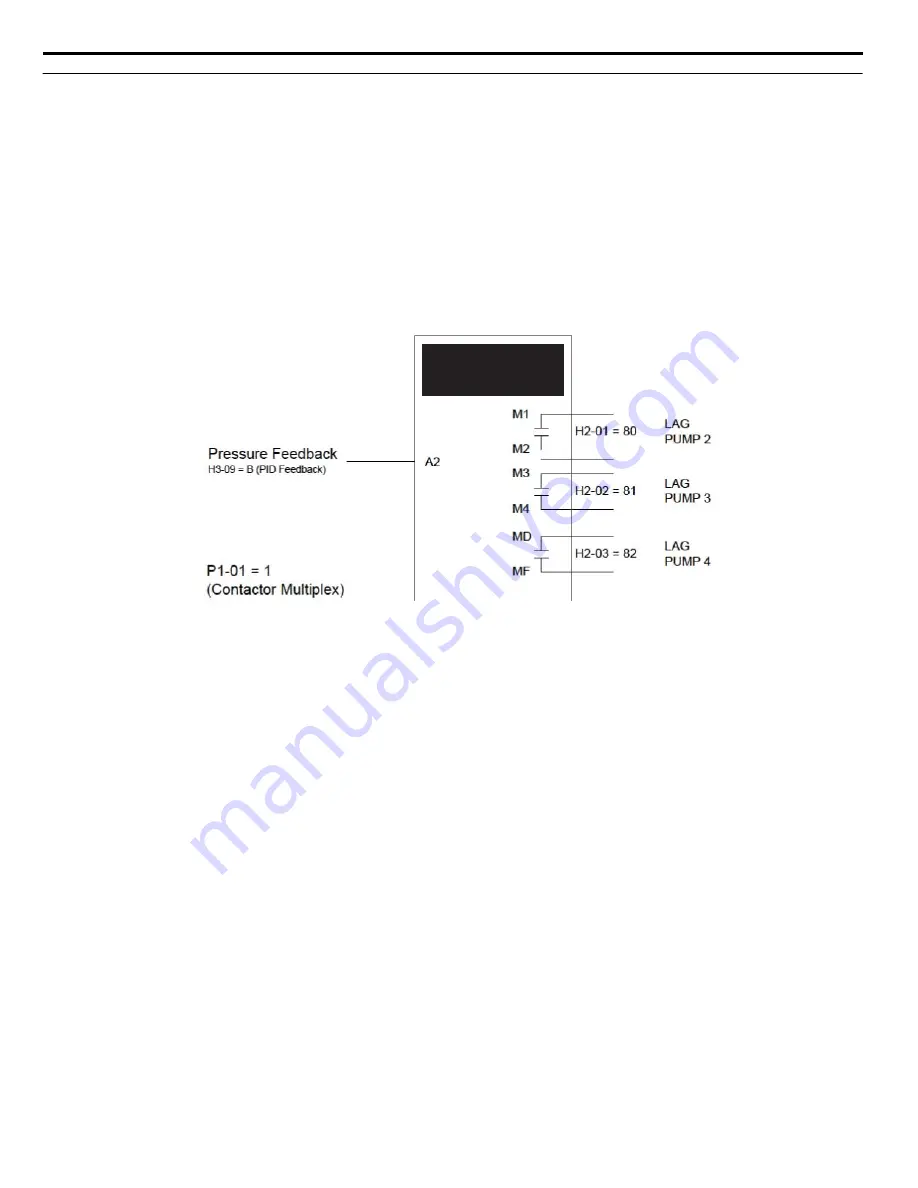
u
Vertical Turbine Controller (VTC)
Vertical turbine pumps are typically used when water needs to be pumped from deep-water wells or open bodies of water such
as rivers, lakes, irrigation canals, lifting stations, and water storage facilities. The VTC Application Preset allows the operator
to easily setup control for a wide range of pumping applications. The drive will automatically adjust pump-operating conditions
from Simplex (one pump on the drive) to multiple lag pumps as the process variables change. Control can be extended from
simple pressure regulation to adding suction and vacuum control as well.
n
Required Control Wiring
Most pressure transducers have current-based feedback (4 - 20 mA). The drive A2 terminal is preset for 4-20 mA and
preprogrammed for PI feedback (H3-10 = B). If the sensor is voltage based (0-10 V) and terminal A3 is unused, then wire the
transducer to terminal A3 and program H3-10 to F (A2 not used) and H3-06 to B (A3 PI Feedback).
When using lag pumps, the lag pump on/off control must be wired to the drive digital output terminals. The figure below
shows the drive with the pressure transducer wired into terminal A2 and 3 lag pumps wired into output relays.
Drive
n
Start Up Procedure for Drive with Three Lag Pumps
1.
Set parameter A1-03 to 6011 (VTC Pressure Control). This will preset parameter values for this application.
2.
Set the motor-rated current in parameter E2-01. This information can be found on the motor nameplate or specification
sheet.
3.
Set the number of motor poles in parameter E2-04 (2-pole motors have a rated RPM of slightly less than 3600 RPM;
4-pole motors have a rated RPM of slightly less than 1800 RPM). This information can be found on the motor
nameplate or specification sheet.
4.
Set the feedback device scaling in parameter P1-03. Check the sensor nameplate or specification sheet. For example,
if the device outputs 20 mA at 100.0 PSI of pressure, then set P1-03 to 100.0 PSI. The drive controller will automatically
scale all associated parameters and monitors. Monitor U1-91 (Pump Feedback) will display the measured pressure
in PSI. The drive has a High Feedback Fault set in parameter P1-11. Make sure that P1-11 is appropriately set for
sensor scaling in P1-03.
5.
Set the desired pressure setpoint in parameter Q1-01 (PI setpoint). This is desired pressure that the drive will regulate
the pump to control around. To quickly access this parameter, press the F1 key and then the ENTER key. The U1-99
monitor on the home screen displays the Q1-01 PI setpoint.
6.
Set the minimum speed that the pump can be run in parameter P1-06. The default is 35 Hz. This information can be
found on the pump specification sheet.
7.
The default setting is for the drive to control the pump motor wired to the drive. Additional Lag pumps can be added
to the system by wiring the on/off switch of the lag-pump motor to the drive as shown in the figure above. Set parameter
P1-01 to 1 (Contactor Lag). This will enable the multiplexing control for multiple pumps
8.
Set the number of additional lag pumps in parameter P3-00. For example, for a system with the drive pump and 3
additional lag pumps, set P3-00 to 3.
9.
Set each lag pump’s shutdown (stage off) level in Parameters P3-50, P3-60 and P3-70. The value is set in Hz. The
setting tells the drive controller to de-stage the lag pump if the output frequency drops below this level. This setting
needs to be coordinated with minimum pump speed (P1-06) and the sleep level. It is important that all lag pumps be
de-staged above the sleep level or the drive will not enter sleep mode
4.6 U1000 iQpump Presets and Functions
116
YASKAWA TOEPYAIUPW01A YASKAWA AC Drive - U1000 iQpump Matrix Drive User Manual