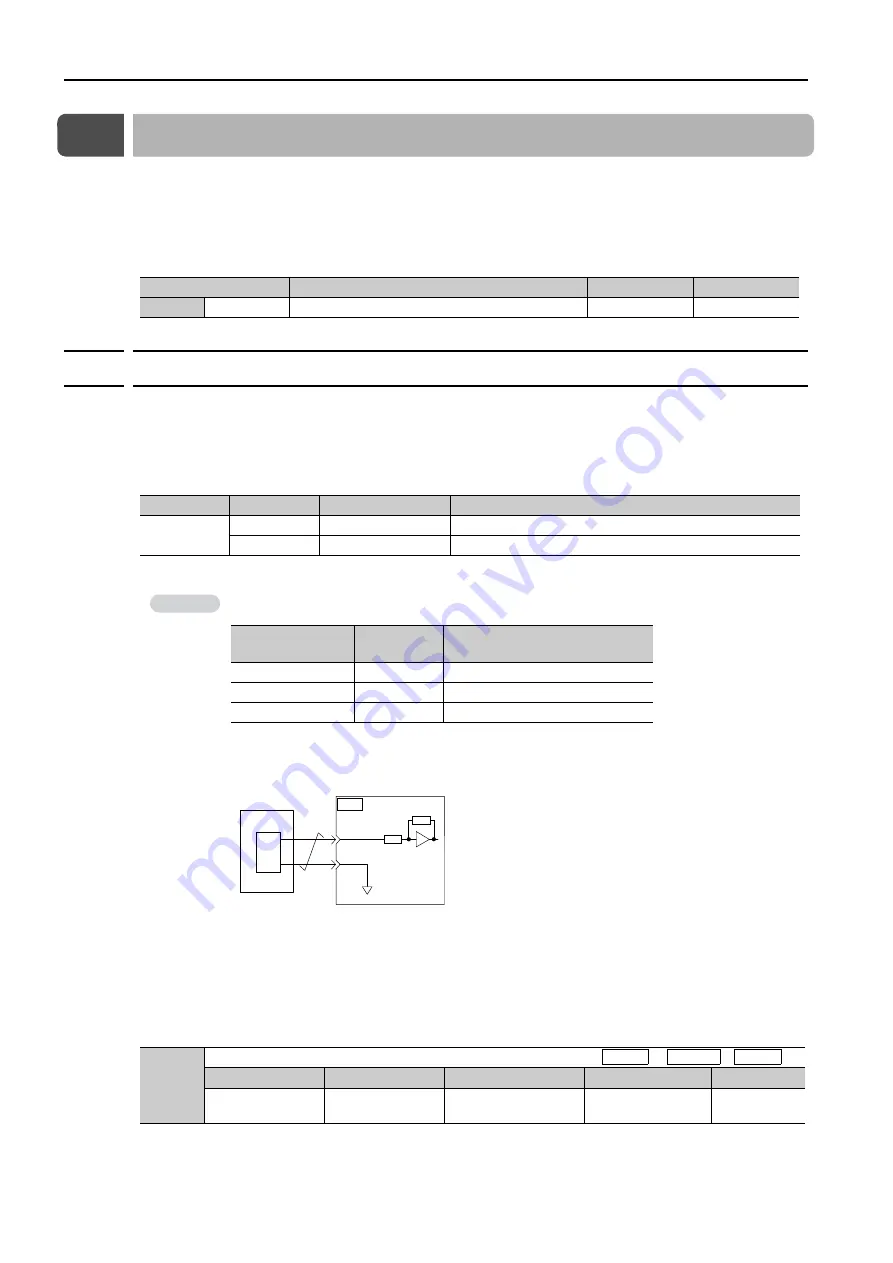
6.7 Torque Control
6.7.1 Basic Settings for Torque Control
6-40
6.7
Torque Control
Torque control is performed by inputting a torque reference with an analog voltage reference to
the SERVOPACK to control the Servomotor with a torque that is proportional to the input volt-
age.
Torque control is set by setting Pn000 = n.
X
(Control Method Selection) to 2 (Torque con-
trol).
6.7.1
Basic Settings for Torque Control
This section describes the torque reference input signal and torque reference input gain.
T-REF (Torque Reference Input) Signal
The T-REF signal is described in the following table.
Maximum input voltage:
±
12 VDC
Setting the Torque Reference Input Gain (Pn400)
The torque of the Servomotor is controlled in proportion to an analog voltage reference.
The reference voltage for the rated motor torque is set in Pn400 (Torque Reference Input Gain)
to define the relationship between the analog voltage reference and the motor output torque.
Parameter
Meaning
When Enabled
Classification
Pn000
n.
2
Torque control
After restart
Setup
Type
Signal
Connector Pin No.
Name
Input
T-REF
CN1-9
Torque reference input
SG
CN1-10
Signal ground for torque reference input
Input Circuit Example
Pn400 (Torque Reference Input Gain) is set to 3 (setting unit: V) by default.
If you will use a host controller, such as a programmable controller, for torque control, con-
nect the above output pins to the analog reference output terminals on the host controller .
Always use twisted-pair cables to control noise.
Pn400
Torque Reference Input Gain
Setting Range
Setting Unit
Default Setting
When Enabled
Classification
10 to 100
0.1 V
30
(rated torque at 3.0 V)
Immediately Setup
Example
Torque Reference
Input
Rotation
Direction
Torque
+3 V
Forward Rated
torque
+1 V
Forward
1/3 rated torque
–1.5 V
Reverse
1/2 rated torque
S
G
CN1
10
T-REF
9
D/A
0 V
Ho
s
t controller
Approx. 14 k
S
ERVOPACK
Speed
Position
Torque