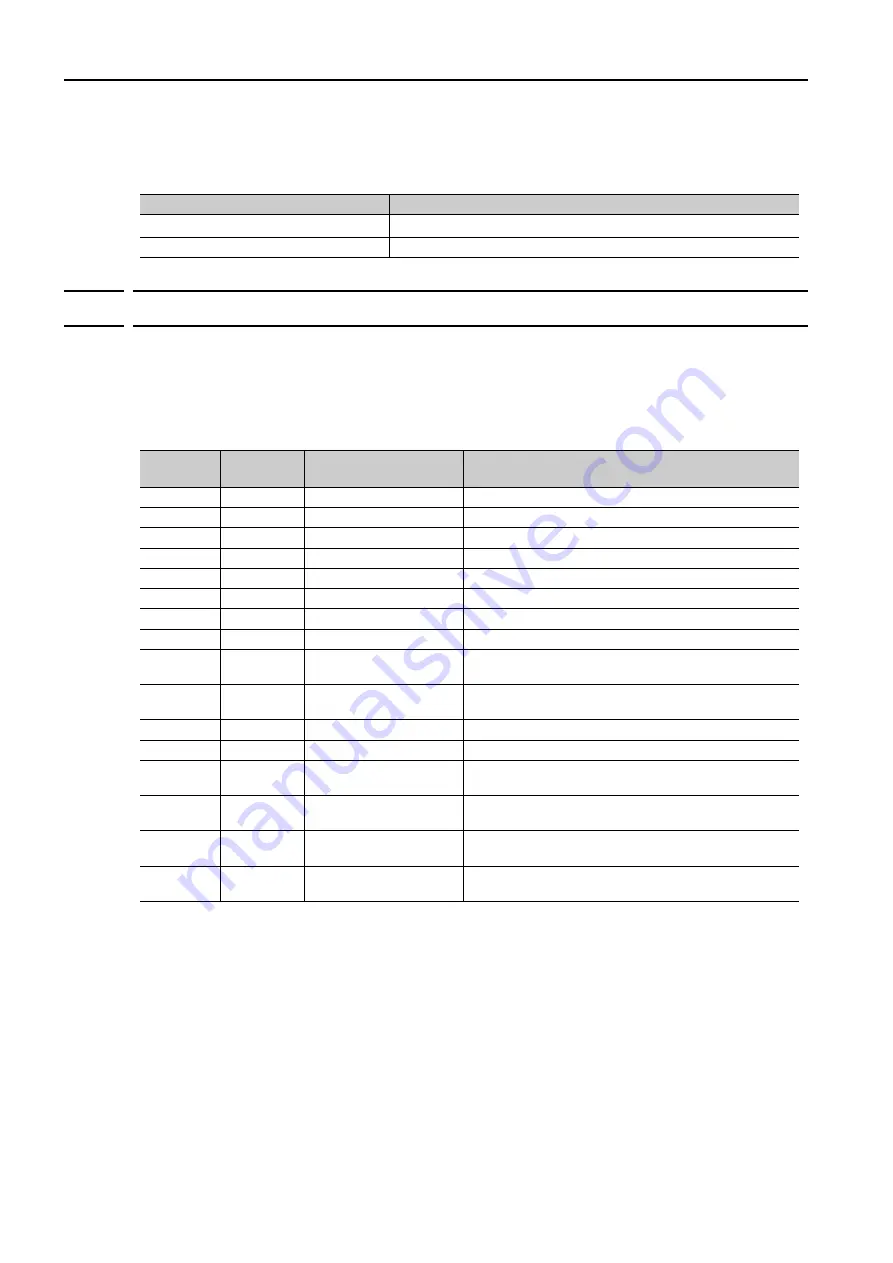
2.7 Command Data
2.7.3 Specifying Monitor Data
2-28
Torque
The following units can be selected.
Settings are made with common parameters 47 and 48.
2.7.3
Specifying Monitor Data
The master station sets the selection code of the monitor data to be read from a slave station
at monitor selection bits SEL_MON1 to 3 in the servo command control field (SVCMD_CTRL)
and at monitor selection bits SEL_MON4 to 6 in the subcommand control field (SUB_CTRL).
The slave station sets the specified monitor selection code and the monitor data in the
response.
The following table lists the monitor data.
Unit
Remark
% of rated torque (default)
×
10
n
[%] can be set.
Max. torque/40000000 (h)
Set "0" for common parameter 48.
Selection
Code
Monitor
Name
Description
Remark
0
APOS
Feedback Position
–
1
CPOS
Command Position
–
2
PERR
Position Error
Valid only when performing position control
3
LPOS1
Latched Position 1
–
4
LPOS2
Latched Position 2
–
5
FSPD
Feedback Speed
–
6
CSPD
Reference Speed
–
7
TRQ
Reference Torque
–
8
ALARM
Detailed Information on
the Current Alarm
When an alarm has occurred after the occurrence of a
warning, the information on the alarm is displayed.
9
MPOS
Command Position
Input reference position in a position control loop
MPOS = APOS + PERR
A
–
Reserved
–
B
–
Reserved
–
C
CMN1
Common Monitor 1
Selects the monitor data specified at common param-
eter 89.
D
CMN2
Common Monitor 2
Selects the monitor data specified at common param-
eter 8A.
E
OMN1
Optional Monitor 1
Selects the monitor data specified at parameter
Pn824.
F
OMN2
Optional Monitor 2
Selects the monitor data specified at parameter
Pn825.