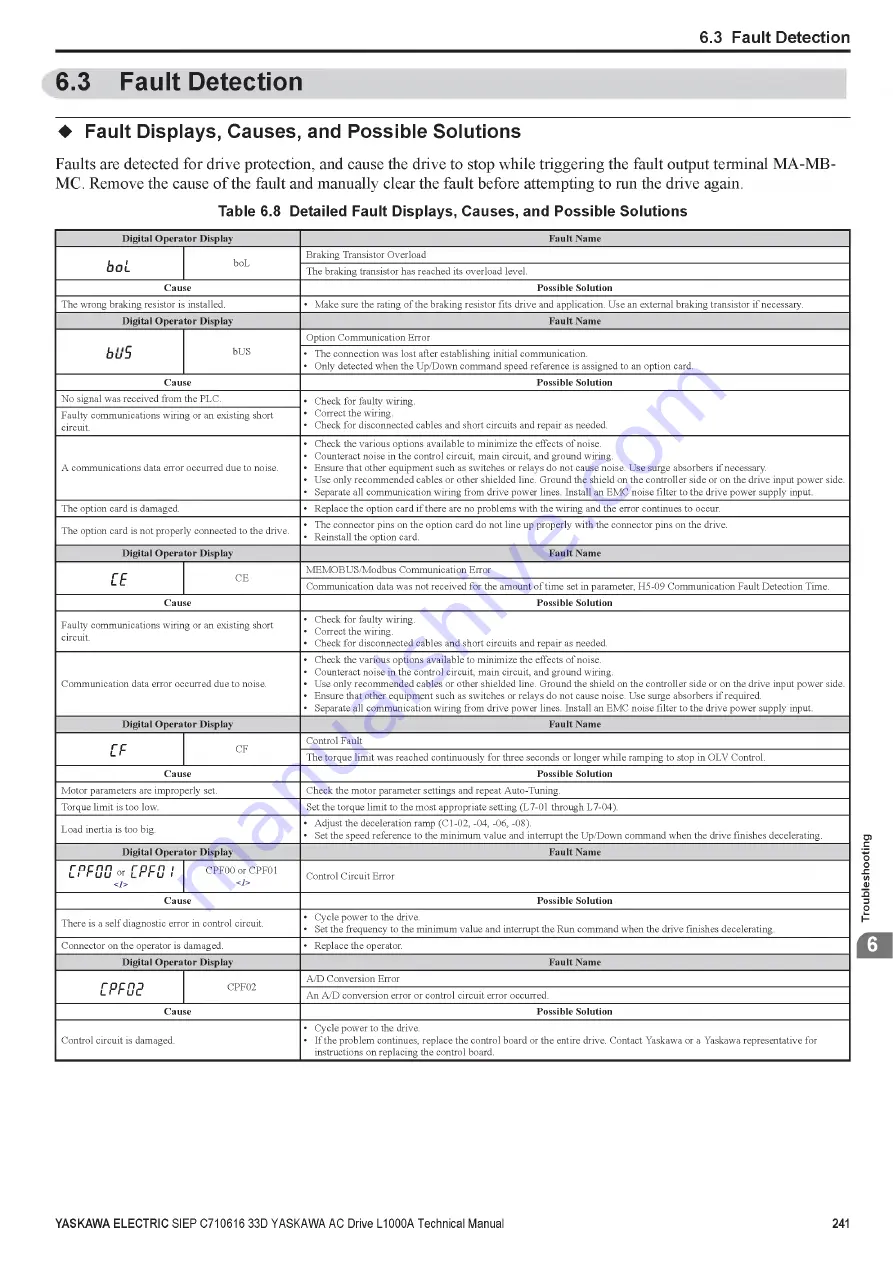
6.3 Fault Detection
6.3
Fault Detection
♦ Fault Displays, Causes, and Possible Solutions
Faults are detected for drive protection, and cause the drive to stop while triggering the fault output terminal MA-MB-
MC. Remove the cause o f the fault and manually clear the fault before attempting to run the drive again.
Table 6.8 Detailed Fault Displays, Causes, and Possible Solutions
D i g i t a l O p e r a t o r D i s p l a y
F a u l t N a m e
boL
boL
Braking Transistor Overload
The braking transistor has reached its overload level.
C a u s e
P o s s ib le S o l u t i o n
The wrong braking resistor is installed.
• Make sure the rating o f the braking resistor fits drive and application. U se an external braking transistor if necessary.
D i g i t a l O p e r a t o r D i s p l a y
F a u l t N a m e
bu5
bUS
Option Communication Error
• The connection was lost after establishing initial communication.
• Only detected when the U p/Dow n command speed reference is assigned to an option card.
C a u s e
P o s s i b l e S o l u t i o n
N o signal was received from the PLC.
• Check for faulty wiring.
• Correct the wiring.
• Check for disconnected cables and short circuits and repair as needed.
Faulty communications wiring or an existing short
circuit.
A communications data error occurred due to noise.
• Check the various options available to m inim ize the effects o f noise.
• Counteract noise in the control circuit, main circuit, and ground wiring.
• Ensure that other equipment such as switches or relays do not cause noise. U se surge absorbers if necessary.
• U se only recommended cables or other shielded line. Ground the shield on the controller side or on the drive input power side.
• Separate all communication wiring from drive power lines. Install an EMC noise filter to the drive power supply input.
The option card is damaged.
• Replace the option card i f there are no problems with the wiring and the error continues to occur.
The option card is not properly connected to the drive.
• The connector pins on the option card do not line up properly with the connector pins on the drive.
• Reinstall the option card.
D i g i t a l O p e r a t o r D i s p l a y
F a u l t N a m e
CE
CE
MEM OBUS/M odbus Communication Error
Communication data was not received for the amount o f tim e set in parameter, H 5-09 Communication Fault Detection Time.
C a u s e
P o s s i b l e S o l u t i o n
Faulty communications wiring or an existing short
circuit.
• Check for faulty wiring.
• Correct the wiring.
• Check for disconnected cables and short circuits and repair as needed.
Communication data error occurred due to noise.
• Check the various options available to m inim ize the effects o f noise.
• Counteract noise in the control circuit, main circuit, and ground wiring.
• U se only recommended cables or other shielded line. Ground the shield on the controller side or on the drive input power side.
• Ensure that other equipment such as switches or relays do not cause noise. U se surge absorbers if required.
• Separate all communication wiring from drive power lines. Install an EMC noise filter to the drive power supply input.
D i g i t a l O p e r a t o r D i s p l a y
F a u l t N a m e
CF
CF
Control Fault
The torque limit was reached continuously for three seconds or longer w hile ramping to stop in OLV Control.
C a u s e
P o s s ib le S o l u t i o n
Motor parameters are improperly set.
Check the motor parameter settings and repeat Auto-Tuning.
Torque limit is too low.
Set the torque limit to the m ost appropriate setting (L7-01 through L7-04).
Load inertia is too big.
• Adjust the deceleration ramp (C 1-02, -04, -06, -08).
• Set the speed reference to the minimum value and interrupt the U p/Dow n command when the drive finishes decelerating.
D i g i t a l O p e r a t o r D i s p l a y
F a u l t N a m e
r o c n n
or Г П Г П
t
L r r u u
or
Г Г и t
<1>
CPF00 or CPF01
<1>
Control Circuit Error
C a u s e
P o s s ib le S o l u t i o n
There is a s e lf diagnostic error in control circuit.
• Cycle power to the drive.
• Set the frequency to the minimum value and interrupt the Run command when the drive finishes decelerating.
Connector on the operator is damaged.
• Replace the operator.
D i g i t a l O p e r a t o r D i s p l a y
F a u l t N a m e
CP FOB
CPF02
A /D Conversion Error
A n A /D conversion error or control circuit error occurred.
C a u s e
P o s s i b l e S o l u t i o n
Control circuit is damaged.
• Cycle power to the drive.
• I f the problem continues, replace the control board or the entire drive. Contact Yaskawa or a Yaskawa representative for
instructions on replacing the control board.
T
.
YASKAWA ELECTRIC SIEP C710616 33D YASKAWA AC Drive L1000A Technical Manual
241
T
ro
u
b
le
s
h
o
o
ti
n
g