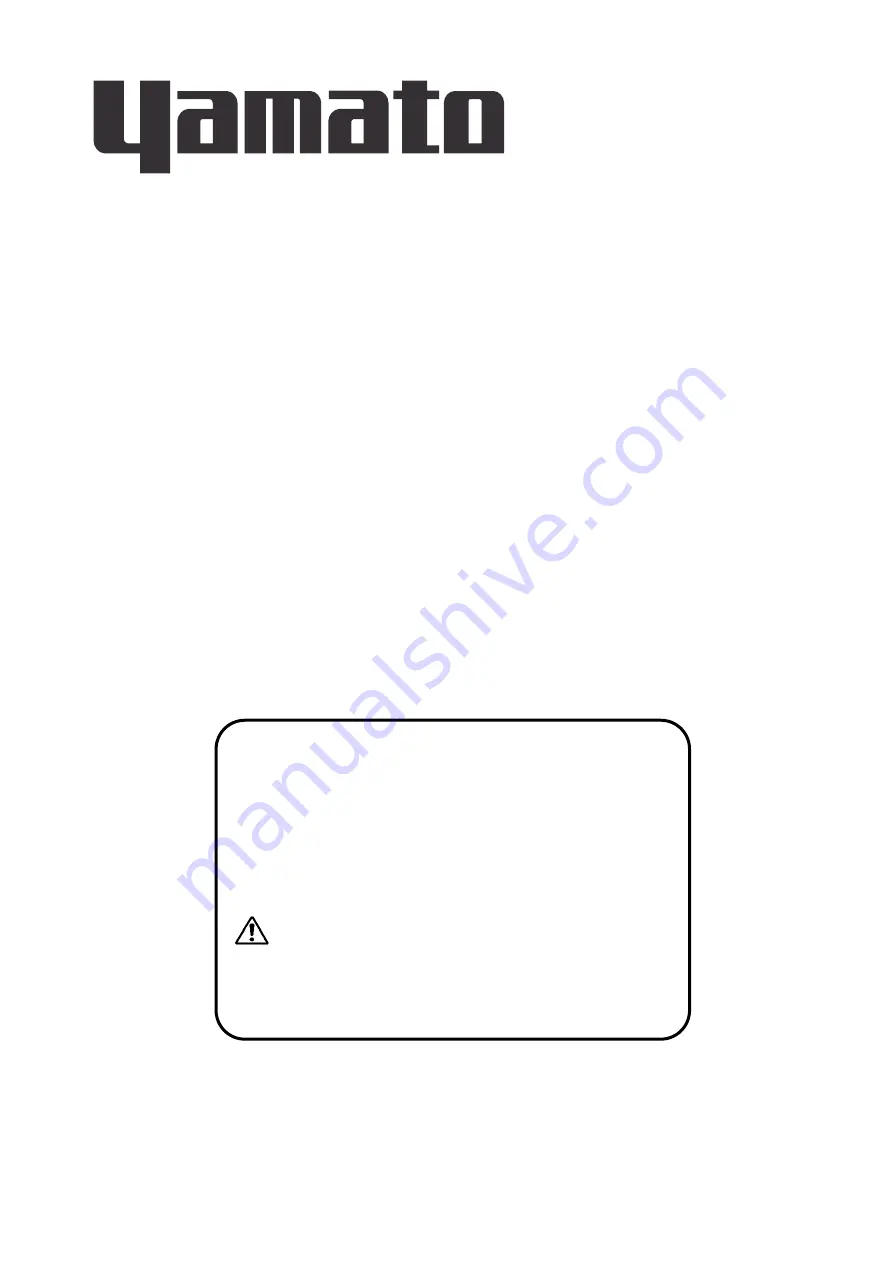
Rotary Evaporator
RE202-A/212-A
Instruction Manual
First Edition
Yamato Scientific Co., Ltd.
Printed on recycled paper
Thank you for choosing RE series Rotary
Evaporators from Yamato Scientific Co., Ltd.
For proper equipment operation, please read
and become thoroughly familiar cith this
instruction manual before use. Alcays keep
equipment documentation safe and close at
hand for convenient future reference.
Warning
:
Read instruction manual
carnings and cautions carefully
and completely before
proceeding.
Summary of Contents for RE202-A/212-A
Page 2: ......
Page 4: ...1 1 SAFETY PRECAUTIONS Explanation of Symbols ...