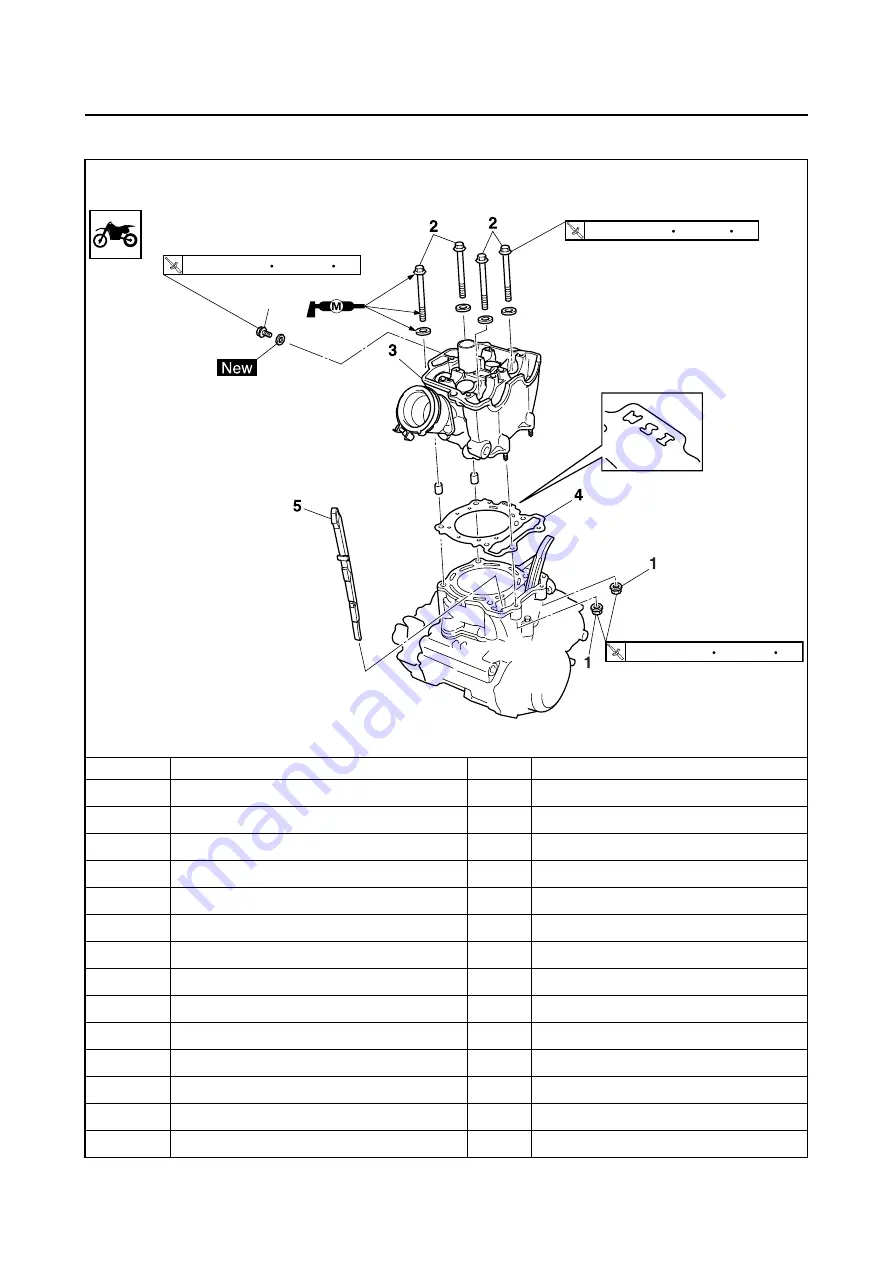
CYLINDER HEAD
6-20
EAS2GBB244
CYLINDER HEAD
Removing the cylinder head
Order
Part name
Q’ty
Remarks
Seat
Refer to “GENERAL CHASSIS” on page 5-1.
Side cover (left/right)
Refer to “GENERAL CHASSIS” on page 5-1.
Air scoop (left/right)
Refer to “GENERAL CHASSIS” on page 5-1.
Fuel tank
Refer to “FUEL TANK” on page 8-1.
Exhaust pipe and silencer
Refer to “ENGINE REMOVAL” on page 6-1.
Radiator hose
Disconnect.
Coolant temperature sensor coupler
Disconnect.
Throttle body
Refer to “THROTTLE BODY” on page 8-7.
Camshaft
Refer to “CAMSHAFT” on page 6-12.
Upper engine bracket
Refer to “ENGINE REMOVAL” on page 6-1.
1
Nut (cylinder head)
2
2
Bolt (cylinder head)
4
3
Cylinder head
1
4
Cylinder head gasket
1
6
10 Nm (1.0 m kgf, 7.2 ft Ibf)
T.R.
33 Nm (3.3 m kgf, 24 ft Ibf)
T.R.
10 Nm (1.0 m kgf, 7.2 ft Ibf)
T.R.
Summary of Contents for WR250F 2017
Page 4: ......
Page 10: ......
Page 12: ......
Page 16: ...LOCATION OF IMPORTANT LABELS 1 2 EUR...
Page 17: ...LOCATION OF IMPORTANT LABELS 1 3 AUS NZL ZAF...
Page 41: ...MULTI FUNCTION DISPLAY 1 27...
Page 78: ...LUBRICATION SYSTEM CHART AND DIAGRAMS 2 25...
Page 80: ...LUBRICATION SYSTEM CHART AND DIAGRAMS 2 27...
Page 82: ...LUBRICATION SYSTEM CHART AND DIAGRAMS 2 29...
Page 84: ...CABLE ROUTING DIAGRAM 2 31 EAS2GBB073 CABLE ROUTING DIAGRAM...
Page 86: ...CABLE ROUTING DIAGRAM 2 33...
Page 88: ...CABLE ROUTING DIAGRAM 2 35...
Page 90: ...CABLE ROUTING DIAGRAM 2 37...
Page 92: ...CABLE ROUTING DIAGRAM 2 39...
Page 94: ...CABLE ROUTING DIAGRAM 2 41...
Page 96: ...CABLE ROUTING DIAGRAM 2 43...
Page 98: ...CABLE ROUTING DIAGRAM 2 45...
Page 152: ...CHASSIS 4 9...
Page 162: ...FRONT WHEEL 5 8 1 1...
Page 226: ...CHAIN DRIVE 5 72...
Page 270: ...ELECTRIC STARTER 6 41...
Page 294: ...OIL PUMP AND BALANCER GEAR 6 65 a 2 10 b 2 9 1 b 5 3 a 4 10 5 9 3 E c d 6 7 8 8 b 6...
Page 300: ...GENERATOR AND STARTER CLUTCH 6 71 1 a 3 3 2 4...
Page 351: ...CHARGING SYSTEM 9 15...
Page 355: ...LIGHTING SYSTEM 9 19...
Page 363: ...COOLING SYSTEM 9 27...
Page 395: ...FUEL PUMP SYSTEM 9 59...
Page 396: ...ELECTRICAL COMPONENTS 9 60 EAS2GBB381 ELECTRICAL COMPONENTS EAS2GBB382 9 10 11 1 3 2 4 5 6 7 8...
Page 398: ...ELECTRICAL COMPONENTS 9 62 12 11 10 2 3 1 6 7 4 5 8 9...
Page 400: ...ELECTRICAL COMPONENTS 9 64 EAS2GBB383 CHECKING THE SWITCHES 4 1 3 2 B B Sb B B B B B B B B...
Page 418: ...ELECTRICAL COMPONENTS 9 82...
Page 429: ......
Page 430: ...PRINTED IN JAPAN E PRINTED ON RECYCLED PAPER...