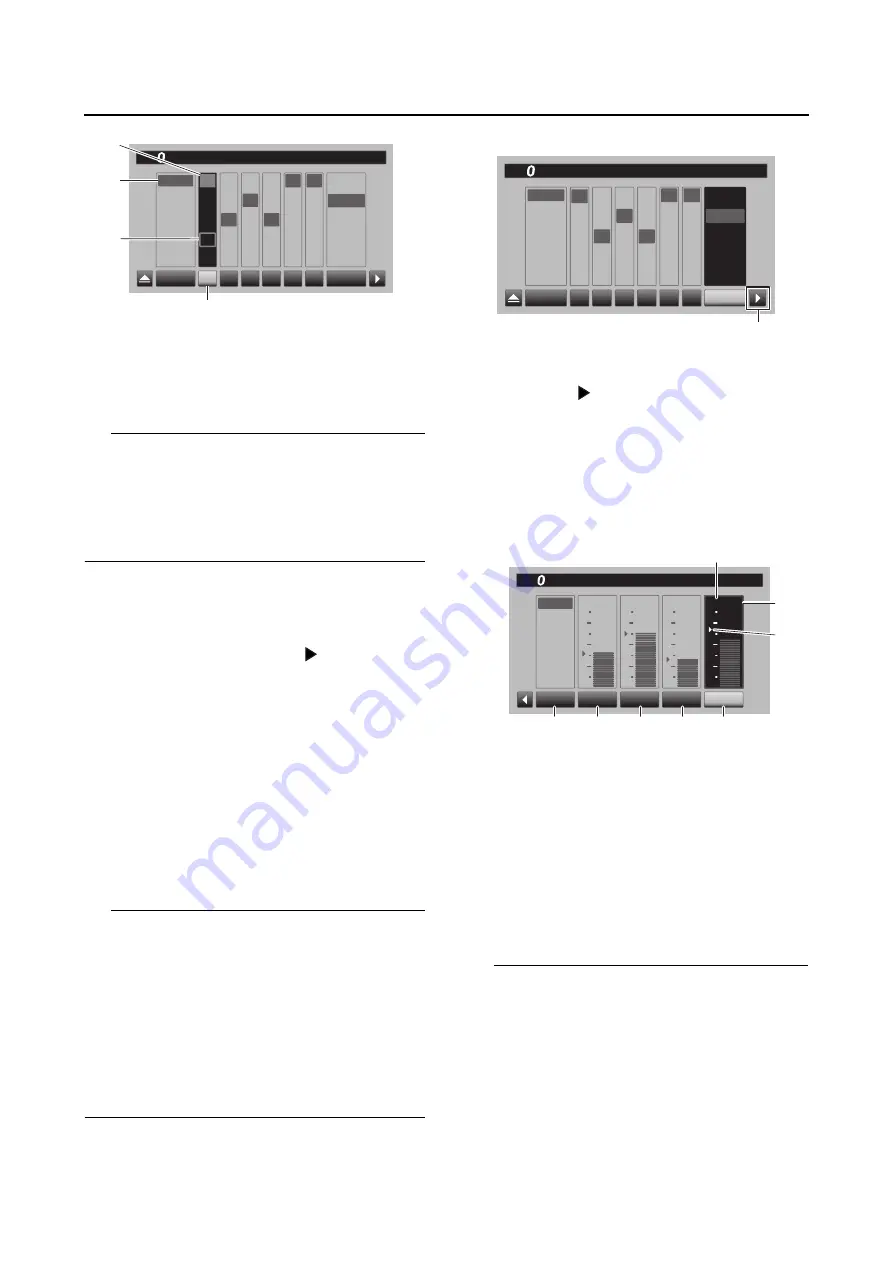
FEATURES
1-39
TIP
•
When a YRC item is selected, the current set-
ting level is indicated by a blue-framed square
and the factory preset level is indicated in a
grey box.
•
Factory preset levels vary depending on the
selected YRC mode.
4. To customize other YRC modes or adjust in-
dividual YRC items, repeat from step 2.
When finished, select the triangle mark on
the far left to return to the MENU screen; or
for YZF-R1M, select the “ ” mark to fine
tune the ERS mode settings.
ERS (YZF-R1M)
There are three automatic setting modes; A-1,
A-2, and A-3. A-3 is fixed and cannot be adjust-
ed. A-1 and A-2 can be adjusted to within a -5 to
+5 offset of their factory preset settings.
There are three manual setting modes; M-1, M-
2, and M-3. When a manual mode is selected,
the SCU does not actively adjust the suspension
compression and rebound damping forces.
Manual mode suspension settings are adjust-
able to 32 levels.
TIP
•
A-1 and M-1 are preset for track use with rac-
ing slick tires.
•
A-2 and M-2 are preset for track use with street
tires.
•
A-3 and M-3 are preset for street use with
street tires.
•
Spring preload is manually adjusted. (Refer to
“ADJUSTING THE PRELOAD OF THE
FRONT FORK LEGS (for YZF-R1M)” on page
3-24.)
[To adjust the ERS mode settings]
1. Select the “ ” mark located to the right of
ERS.
2. The display will change to the front and rear
suspension setting screen and the ERS
mode selection box “SETTING” is highlight-
ed. Short push the wheel switch to enter the
box and select the ERS mode A-1, A-2, M-1,
M-2, M-3 that you want to adjust.
3. Select the suspension item, Fr COM, Fr REB,
Rr COM, Rr REB, that you want to adjust.
TIP
•
To decrease the damping force and soften the
suspension, increase the setting level.
•
To increase the damping force and harden the
suspension, decrease the setting level.
•
For A-1 and A-2, a number indicated in ( )
means how many levels are changed from its
factory preset level.
•
When a suspension setting item in A-1 or A-2
is offset, the same suspension item will be sim-
ilarly offset in the other automatic mode (offset
1. YRC item
2. Current level setting
3. YRC mode
4. Factory preset level
D
C
B
A
1
2
3
4
1
2
3
4
1
2
1
2
3
3
5
OFF
1
2
OFF
OFF
1
2
OFF
A-1
A-2
M-1
M-2
A-3
YRC
PWR TCS SCS LCS QSS LIF
ESC
YRC
PWR
TCS SCS LCS QSS LIF
ERS
12:00
YRC Setting
km/h
1
3
4
2
1. To ERS menu
1. ERS mode selection box “SETTING”
2. Front compression damping force
3. Front rebound damping force
4. Rear compression damping force
5. Rear rebound damping force
6. Factory preset level
7. Current level setting
8. Offset level
D
C
B
A
1
2
3
4
1
2
3
4
1
2
1
2
3
3
5
OFF
1
2
OFF
OFF
1
2
OFF
A-1
A-2
M-1
M-2
A-3
YRC
PWR TCS SCS LCS QSS LIF
YRC
PWR TCS SCS LCS QSS LIF
12:00
YRC Setting
km/h
ERS
1
25
16
22
13
( )
( )
( )
( )
-
+
+
+
(
-
5
)
(
+
0
)
(
+
0
)
(
+
0
)
A-2
M-1
M-2
M-3
A-3
Fr COM
Rr COM
Fr REB
Rr REB
SETTING
YRC Setting
km/h
12:00
7
6
8
2
3
4
5
1
Summary of Contents for R1 Series 2015
Page 1: ...2015 SERVICE MANUAL YZF R1 YZF R1F YZF R1M YZF R1MF 2CR 28197 E0...
Page 2: ......
Page 8: ......
Page 74: ...SPECIAL TOOLS 1 65...
Page 105: ...LUBRICATION POINTS AND LUBRICANT TYPES 2 30...
Page 110: ...LUBRICATION SYSTEM CHART AND DIAGRAMS 2 35 Crankcase and cylinder right side view...
Page 112: ...LUBRICATION SYSTEM CHART AND DIAGRAMS 2 37 Timing chain cover and oil pipe right side view...
Page 114: ...LUBRICATION SYSTEM CHART AND DIAGRAMS 2 39 Oil pump and oil cooler bottom view...
Page 116: ...LUBRICATION SYSTEM CHART AND DIAGRAMS 2 41 Camshaft and balancer shaft top view...
Page 118: ...LUBRICATION SYSTEM CHART AND DIAGRAMS 2 43 Crankshaft rear view...
Page 120: ...LUBRICATION SYSTEM CHART AND DIAGRAMS 2 45 Crankshaft and transmission top view...
Page 122: ...COOLING SYSTEM DIAGRAMS 2 47 EAS20020 COOLING SYSTEM DIAGRAMS...
Page 124: ...COOLING SYSTEM DIAGRAMS 2 49...
Page 126: ...CABLE ROUTING 2 51 EAS20021 CABLE ROUTING Handlebar front view...
Page 128: ...CABLE ROUTING 2 53 Clutch cable right side view...
Page 130: ...CABLE ROUTING 2 55 O2 sensor lead right side view...
Page 132: ...CABLE ROUTING 2 57 Electrical components tray left side view...
Page 134: ...CABLE ROUTING 2 59 ECU Engine Control Unit left side view...
Page 136: ...CABLE ROUTING 2 61 Frame top view...
Page 138: ...CABLE ROUTING 2 63 Frame top view for YZF R1M...
Page 140: ...CABLE ROUTING 2 65 Frame top view...
Page 142: ...CABLE ROUTING 2 67 Frame top view...
Page 144: ...CABLE ROUTING 2 69 Rear fender top view...
Page 146: ...CABLE ROUTING 2 71 Rear fender left side view...
Page 148: ...CABLE ROUTING 2 73 Rear brake hose right side view...
Page 150: ...CABLE ROUTING 2 75 Front brake hose left side view...
Page 152: ...CABLE ROUTING 2 77 Front brake hose left side view...
Page 154: ...CABLE ROUTING 2 79 Hydraulic unit assembly top and left side view...
Page 156: ...CABLE ROUTING 2 81 Fuel tank top and left side view...
Page 158: ...CABLE ROUTING 2 83 Air filter case and throttle bodies top and left side view...
Page 160: ...CABLE ROUTING 2 85 Air cut off valve right side view...
Page 162: ...CABLE ROUTING 2 87 Air duct left and right side view...
Page 164: ...CABLE ROUTING 2 89 Radiator left side view...
Page 166: ...CABLE ROUTING 2 91 Radiator right side view...
Page 168: ...CABLE ROUTING 2 93 Muffler top and left side view...
Page 170: ...CABLE ROUTING 2 95 CCU top and right side view for YZF R1M...
Page 172: ...CABLE ROUTING 2 97...
Page 213: ...PERIODIC MAINTENANCE 3 39 1 1 c b c b...
Page 214: ...PERIODIC MAINTENANCE 3 40...
Page 306: ...FRONT FORK for YZF R1 4 89 Refer to ADJUSTING THE FRONT FORK LEGS for YZF R1 on page 3 23...
Page 472: ...AIR INDUCTION SYSTEM 7 19 EAS20071 AIR INDUCTION SYSTEM...
Page 478: ...AIR INDUCTION SYSTEM 7 25...
Page 489: ...IGNITION SYSTEM 8 8...
Page 497: ...ELECTRIC STARTING SYSTEM 8 16...
Page 503: ...CHARGING SYSTEM 8 22...
Page 509: ...LIGHTING SYSTEM 8 28...
Page 519: ...SIGNALING SYSTEM 8 38...
Page 525: ...COOLING SYSTEM 8 44...
Page 589: ...FUEL PUMP SYSTEM 8 108...
Page 604: ...ABS Anti lock Brake System 8 123 EAS30525 ABS COMPONENTS CHART 1 2 5 6 7 8 9 10 11 12 3 4 1...
Page 606: ...ABS Anti lock Brake System 8 125 EAS30844 ABS COUPLER LOCATION CHART 2 1 3 4 5...
Page 633: ...ABS Anti lock Brake System 8 152...
Page 653: ...COMMUNICATION CONTROL SYSTEM for YZF R1M 8 172...
Page 654: ...ELECTRICAL COMPONENTS 8 173 EAS20089 ELECTRICAL COMPONENTS...
Page 656: ...ELECTRICAL COMPONENTS 8 175 1 2 3 4 5 6 7 8 9 10 11 12 13 14 15 16 17 18 19 20 21 22 23 24 25...
Page 658: ...ELECTRICAL COMPONENTS 8 177 EAS30549 CHECKING THE SWITCHES 2 1 3 4 6 5 7 8 9 12 13 14 10 11...
Page 694: ...EVENT CODE TABLE 9 15...
Page 698: ......
Page 699: ......
Page 700: ......