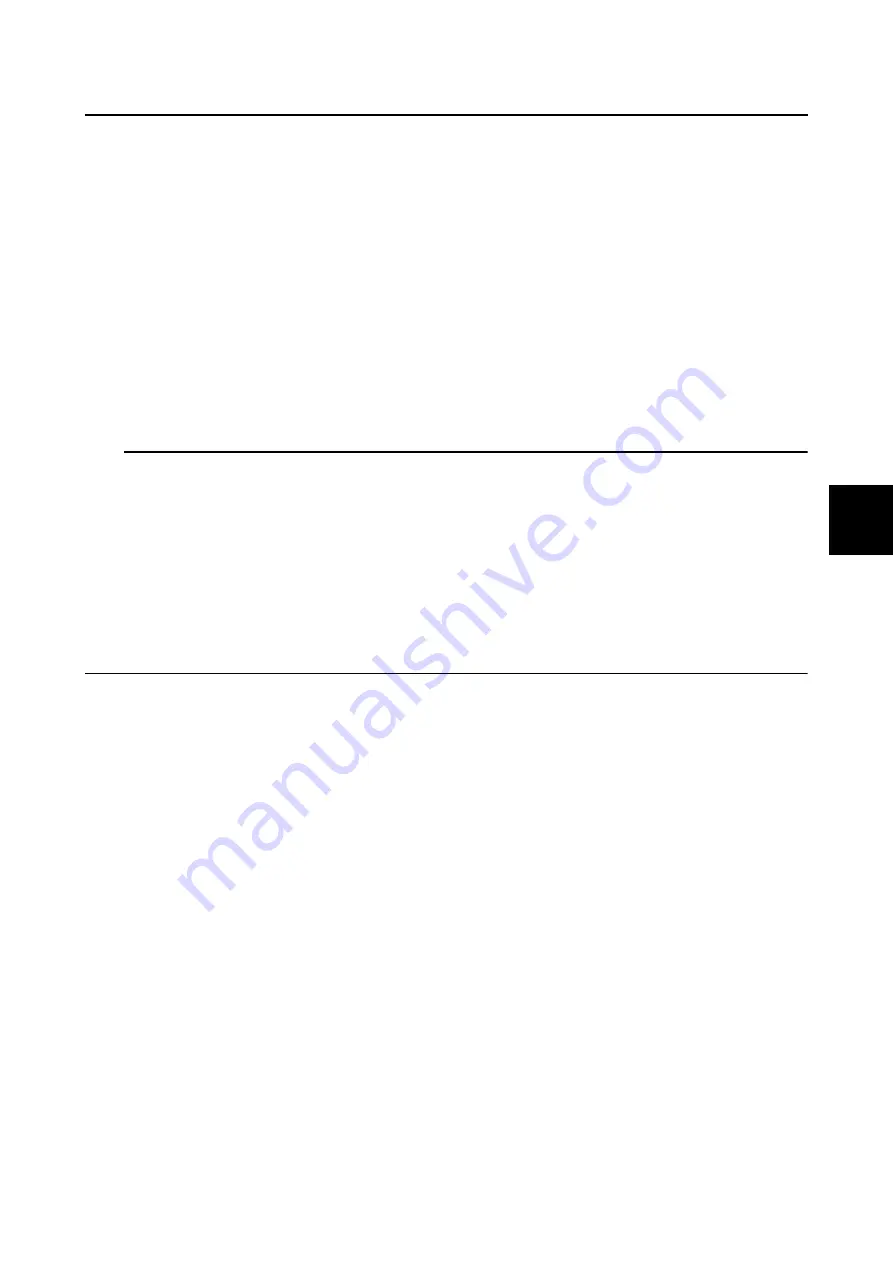
4-4
Troubleshooting the power unit
0
1
2
3
4
5
6
7
8
9
10
A
Troubleshooting the power unit
Troubleshooting procedure
1.
Before troubleshooting the outboard motor, make sure that fresh fuel of the specified type has
been used.
2.
Check that all electrical connections are tight and from corrosion, and that the battery is fully
charged to 12 V.
3.
Check the trouble code using the YDIS first, and then check the electronic control system follow
the trouble code chart.
4.
When a trouble code is detected, check the data logger of the engine ECM record data graph as
well.
5.
If a trouble code is not detected, check the power unit according to “Troubleshooting the power
unit (trouble code not detected)” (4-11).
6.
Before using the YDIS to check the power unit, check the engine ECM circuit. To check the
engine ECM circuit, see “Checking the engine ECM circuit” (5-15).
TIP:
• Make sure to check that the couplers and connectors are securely connected.
• When deleting the diagnosis record on the YDIS, make sure to check the time that the trouble
codes were detected.
• When checking the input voltage of a part, the coupler or connector must be disconnected. As a
result, the engine ECM determines that the part is disconnected and a trouble code is detected.
Therefore, make sure to delete the diagnosis record after checking the input voltage.
• Since the main relay comes on for approximately 10 seconds after the engine start switch is
turned to “OFF,” the power of the engine ECM cannot be turned off. Therefore, if the engine start
switch is turned to “ON” within 10 seconds after it was turned to “OFF,” the trouble codes cannot be
deleted.
Troubleshooting the power unit using the YDIS
1.
Use the trouble codes displayed by the YDIS to check each part according to the “Trouble code
and checking step” table.
2.
Delete the trouble codes after checking, repairing, or replacing a part and check that the trouble
codes are not detected again. If the same trouble codes are detected, the engine ECM may be
faulty.
3.
Check the items listed in the table, if all the items are in good condition, and delete the trouble
code, and then check the trouble codes again. If the same trouble codes are detected again, the
engine ECM is faulty.
YDIS / Troubleshooting the power unit
Summary of Contents for F150B
Page 1: ...SERVICE MANUAL 6BM 28197 5L 11 F150B FL150B ...
Page 4: ......
Page 211: ...6 34 Vapor separator 0 1 2 3 4 5 6 7 8 9 10 A MEMO ...
Page 311: ...8 32 Shimming regular rotation model 0 1 2 3 4 5 6 7 8 9 10 A Shim location F R P T3 T1 T2 ...
Page 351: ...8 72 Shimming counter rotation model 0 1 2 3 4 5 6 7 8 9 10 A Shim location F R P T3 T2 T4 T1 ...
Page 448: ...A 1 MEMO ...
Page 451: ......
Page 452: ...Printed in China Jul 2008 0 6 1 ABE E_4 YAMAHA MOTOR CO LTD ...
Page 458: ......