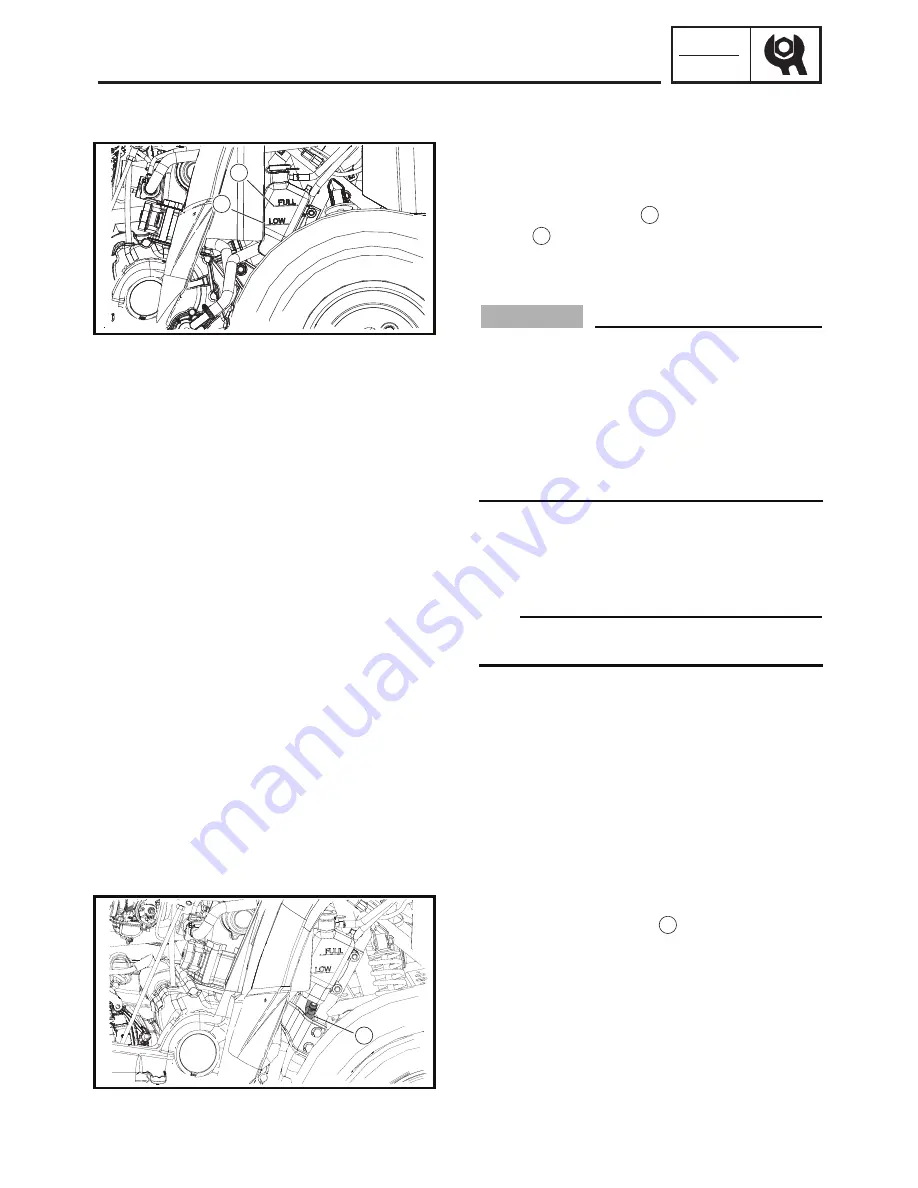
CHK
ADJ
3-25
CHECKING THE COOLANT LEVEL
CHECKING THE COOLANT LEVEL/
1.
Place the machine on a level surface.
2.
Check:
•
Adding water instead of coolant lowers
the antifreeze content of the coolant. If
water is used instead of coolant, check
and if necessary, correct the antifreeze
concentration of the coolant.
•
Use only distilled water. However, soft
water may be used if distilled water is not
available.
4.
Start the engine, warm it up for several
minutes, and then turn it off.
Check:
•
Coolant level
Before checking the coolant level, wait a few
minutes until the coolant has settled.
•
Coolant level
The coolant level should be between the
minimum level mark and maximum level
mark .
Below the minimum level mark
→
Add the
recommended coolant to the proper level.
a
b
a
b
CHANGING THE COOLANT
1
.
Remove:
•
front carrier
•
front panel
Refer to “FRONT CARRIER, FRONT BUMPER
AND FRONT FENDER”.
•
coolant reservoir hose
2
.
Disconnect:
3
.
Drain:
•
Coolant
(from the coolant reservoir)
4
.
Connect:
•
coolant reservoir hose
1
1
CHANGING THE COOLANT
TIP
NOTICE
3
.