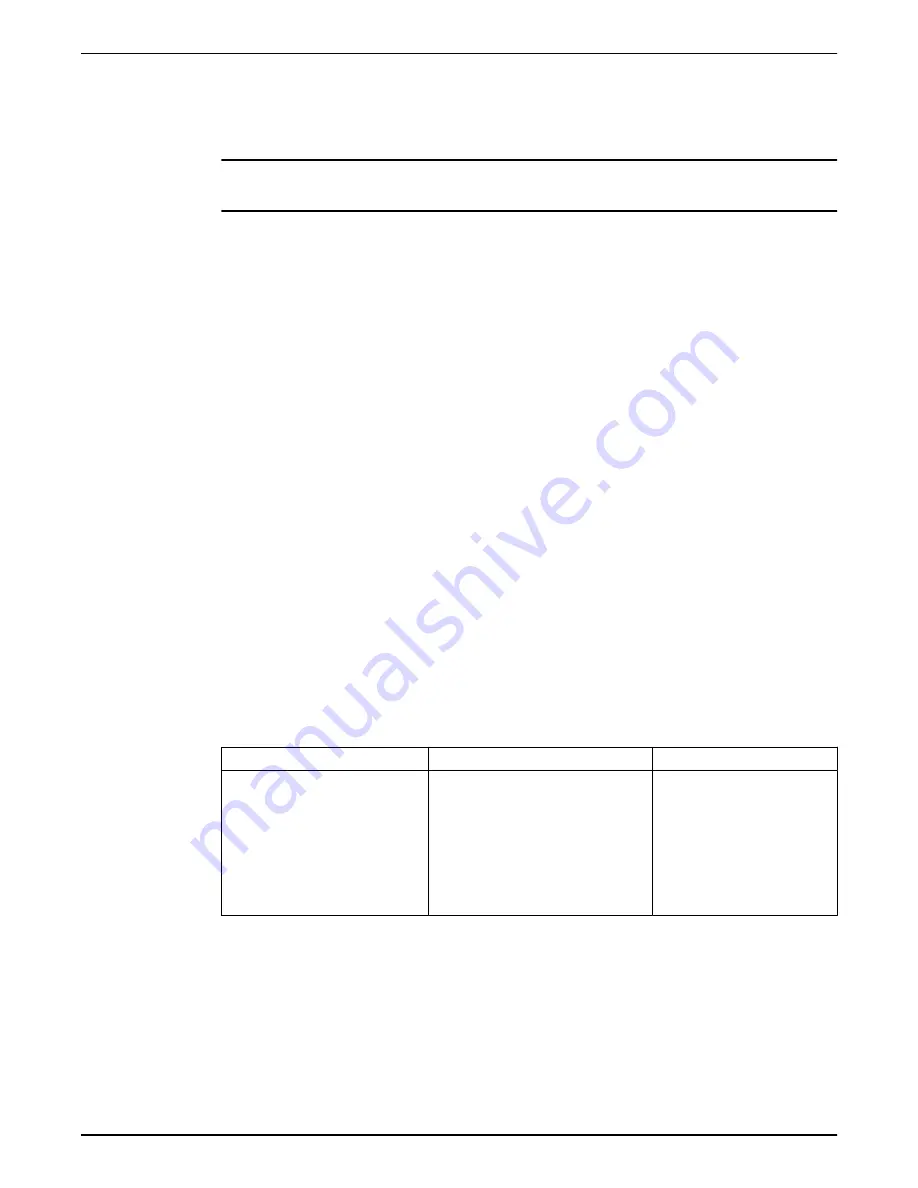
The different types of temperature sensors are:
• Thermal switches
• PTC thermistors
• Pt100
NOTICE:
Do not use a megger or other device applying a higher voltage than 2.5 V.
1. Disconnect the sensor wires.
2. Check the status of the sensor and wiring by measuring the resistance according to the
on page 10.
3. Measure between each sensor lead and ground (earth) to establish that the resistance is
infinite (or at least several megohms).
6.5 Check the leakage detectors
If the unit is connected to the MAS monitoring system, then it is recommended that the
sensors be checked in the MAS unit. Otherwise, use a multimeter.
1. Check the float switch (FLS) in the stator housing, according to the values in
2. Check the float switch (FLS) in the junction box or connection housing.
3. If the drive unit is equipped with a CLS water-in-oil sensor in the oil housing, then check
the CLS by following this procedure.
a) Connect the CLS to a 12 VDC supply.
The sensor must have the correct polarity to be checked. However, a switched plus
and minus does not damage the sensor.
b) Use the multimeter as an ammeter and connect it in series with the sensor.
c) If the sensor is accessible, then check: the alarm function by gripping the sensor with
the hand.
Skin tissue and blood contain a high content of water.
For interpretation of the CLS measurement results, see
on page 10.
6.5.1 FLS
Table 11: Float switch sensor (FLS)
Description
Measured value
Fault values
The float switches are leakage
sensors.
The float switches are located in
the lower part of the stator
housing and in the junction box.
Resistance. 2 sensor variants:
FLS:
• Normal: 1530 ohm
• Alarm: 330 ohm
FLS 10:
• Normal: 1200 ohm
• Alarm: 430 ohm
> 10% (approx.) deviation
from rated ohm values
indicates sensor fault, or fault
in the wiring.
6.6 Change the seal oil
The pump is delivered with a tasteless, odorless, medical white oil of a paraffin type that
fulfills FDA 172.878.
Examples of suitable oil types are the following:
• Statoil MedicWay 32
™
• BP Enerpar M 004
™
• Shell Ondina 927
™
• Shell Ondina X430
™
6 Maintenance
52
P7900 Installation, Operation, and Maintenance Manual
Summary of Contents for FLYFT P7900
Page 1: ...Installation Operation and Maintenance Manual 90028101_1 0 P7900...
Page 2: ......
Page 75: ......