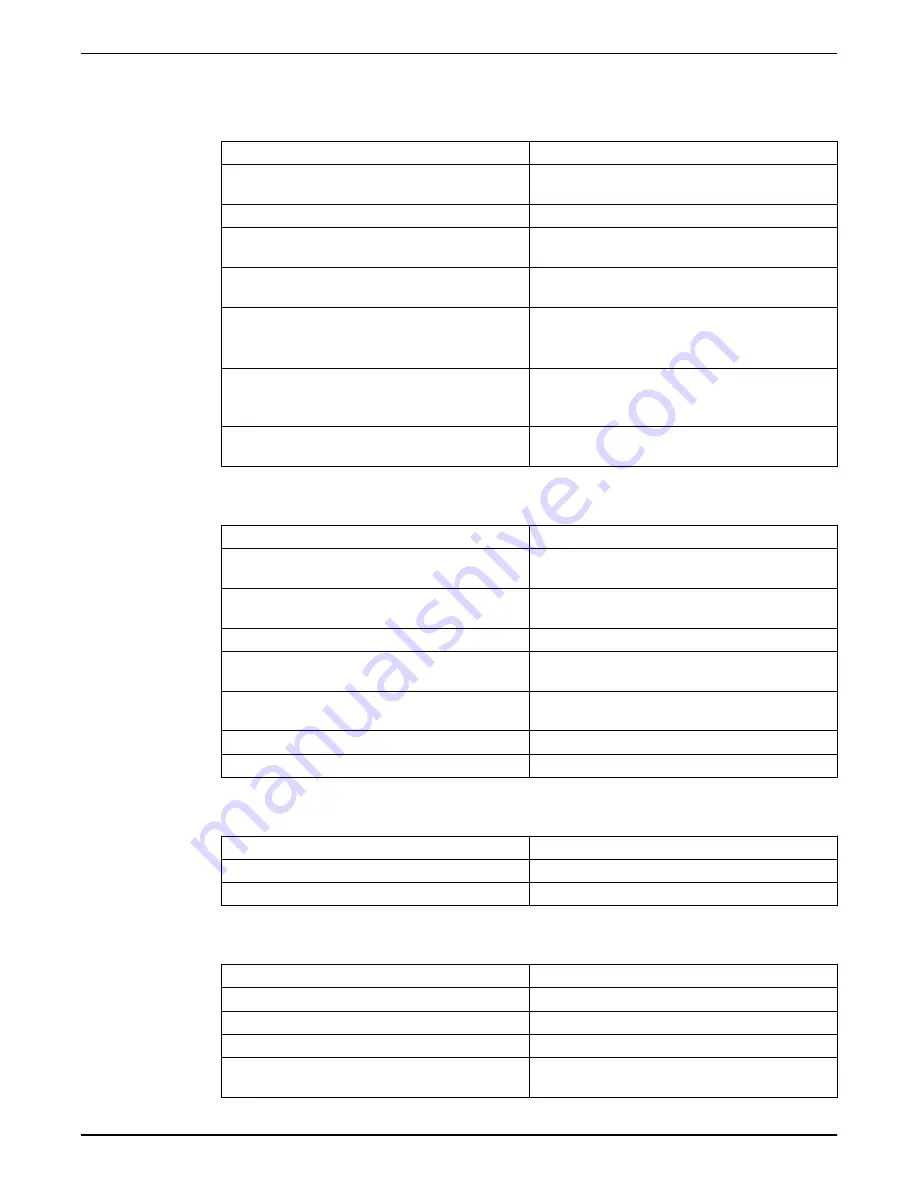
7.5 The thermal overload protection of the motor is triggered
occasionally, or after the pump unit has been running for a few minutes
Cause
Remedy
It is calibrated at a value too low in relation to the
rated current of the motor
Recalibrate
Input voltage outside the rated limits
Make sure the voltage values are correct
Unbalanced input voltage
Make sure the voltage of the three phases is
balanced
Incorrect working curve (flow rate greater that the
maximum permitted flow rate)
Reduce the required flow rate
Liquid too dense, presence of solid or fibrous
substances (pump unit overloaded)
• Reduce the density of the liquid and/or
• Remove the solid substance and/or
• Increase the size of the motor
Room temperature too high, exposure to sunlight
• Lower the temperature at the point od the
thermal overload protection and/or
• Protect against direct sunlight
Pump unit faulty
Send the pump unit to an authorized workshop for
testing
7.6 The pump unit runs but delivers too little or no liquid
Cause
Remedy
Motor turns in the wrong direction
Check the direction of rotation and change it if
necessary
Incorrect priming (there are air bubbles in the
suction pipe or in the pump unit)
Repeat the priming procedure
Cavitation
Increase the NPSH available in the system
Check valve locked in closed or partially closed
position
Replace the check valve
Foot check valve locked in closed or partially
closed position
Replace the foot valve
Delivery pipe throttled
Remove the throttling
Piping and/or pump unit clogged
Remove the clogging
7.7 The pump unit turns the other way when turned off
Cause
Remedy
Check valve faulty
Replace the check valve
Foot check valve faulty
Replace the foot valve
7.8 The pump unit produces excessive noise and/or vibrations
Cause
Remedy
Cavitation
Increase the NPSH available in the system
Unsuitable anchoring to the ground
Check the anchoring to the ground
Resonance
Check the installation
Anti-vibration joints not installed
Install anti-vibration joints on the suction and
discharge lines of the pump unit
7 Troubleshooting
Series e-80SCXL INSTRUCTION MANUAL
29
Summary of Contents for Bell & Gossett e-80SCXL Series
Page 1: ...INSTRUCTION MANUAL P2005589 A Series e 80SCXL...
Page 2: ......