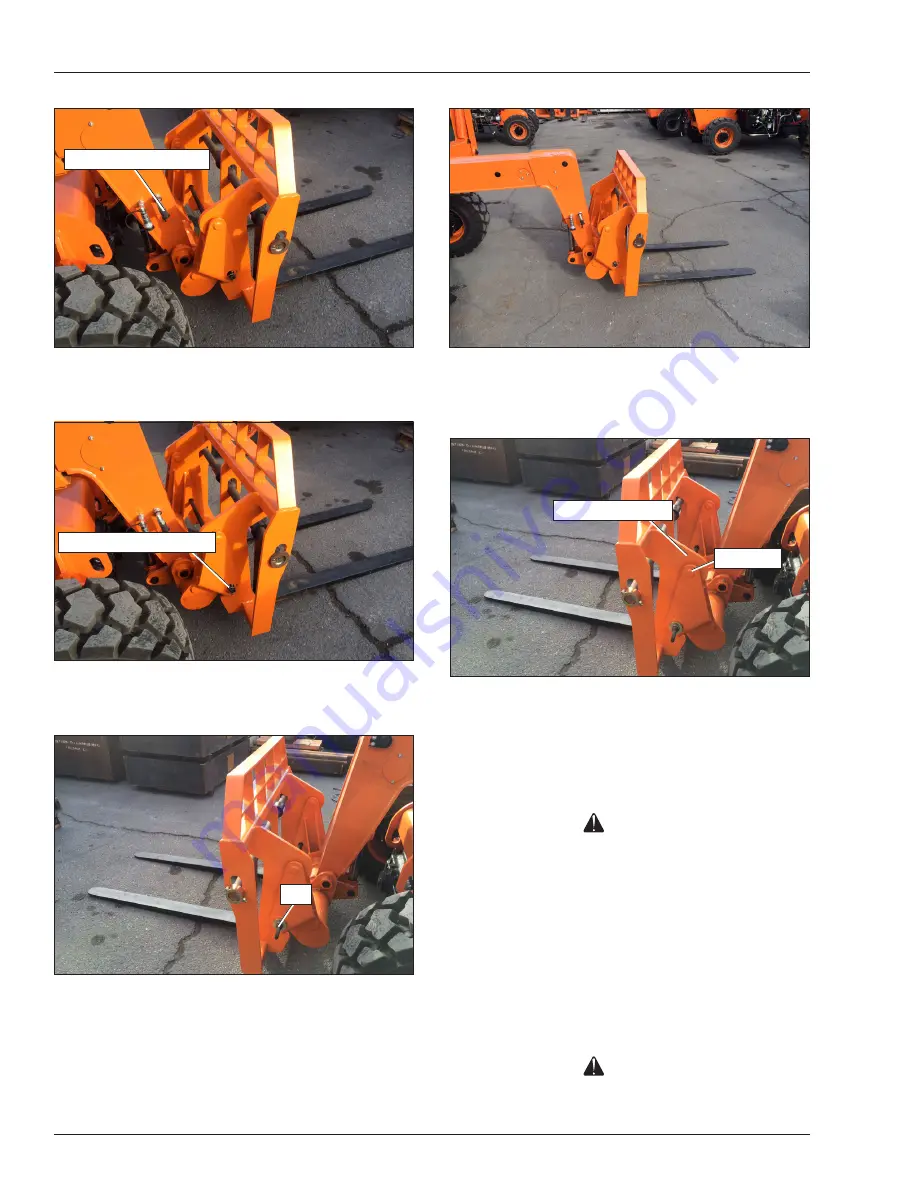
Chapter 6 – Operation
56 XR5919-A
Figure 6.15 – Quick Attach Couplers
7. Remove the quick attach pin keeper.
Figure 6.16 – Quick Attach Pin Keeper
8. Remove the pin at the bottom of the adapter.
Figure 6.17 – Quick Attach Pin
9. Lower the attachment to the ground in a level position.
Quick Attach Couplers
Quick Attach Pin Keeper
Pin
Figure 6.18 – Attachment On Ground
10. Tilt and lower boom until pivot pins (A) have discon-
nected from attachment hooks (B).
Figure 6.19 – Attachment On Ground
11. Retract the boom to fully disconnect the attachment
from the quick attach adapter.
Load Handling
Danger
Death or serious injury by electrocution will result
from contact with or inadequate clearance with en-
ergized power lines or apparatus.
• Take extreme caution when operating the telehan-
dler in an area where active overhead power lines,
overhead or underground cables, or other power
sources exist.
• Contact the appropriate power or utility company to
de-energize power lines or take other suitable pre-
cautions.
Danger
Keep the telehandler, attachments, and loads a safe
distance from electrical power lines.
Attachment Hooks
Pivot Pins
Summary of Contents for XR5919-A
Page 4: ...XR5919 A ...
Page 10: ...Chapter 1 Introduction 4 XR5919 A ...
Page 12: ...Chapter 2 Specifications 6 XR5919 A ...
Page 54: ...Chapter 5 Pre Operation Inspection 48 XR5919 A ...
Page 66: ...Chapter 6 Operation 60 XR5919 A ...
Page 68: ...Chapter 7 Emergency Lowering 62 XR5919 A ...