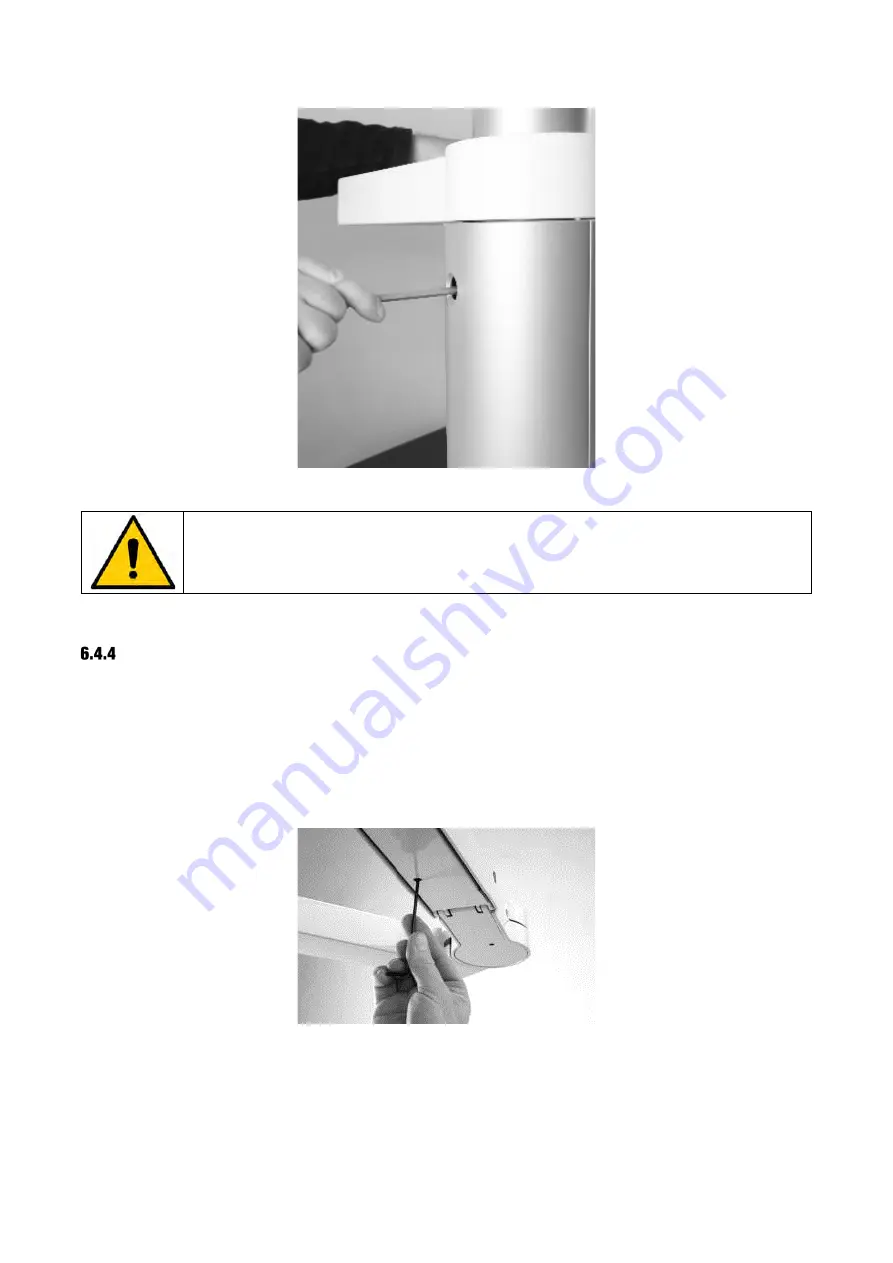
XO FLEX – Installation instructions
Checking
the unit
52
Figure 72 – Adjusting the friction brake of the rear arm
Always remember to fit the cover plug into the hole of the outer cylinder after fitting
the brake.
ADJUSTMENT OF THE FRICTION BRAKES IN THE OPERATING LIGHT ARM AND DISPLAY ARM
The arm for the operating light and the arm for the display have three pivoting joints. Each joint has
its own friction brake, which can be adjusted with a 3mm
-
6 mm Allen key.
Turn brakes clockwise to increase friction.
Turn brakes counter-clockwise to decrease friction.
Figure 73 – Adjusting the vertical friction of the arm