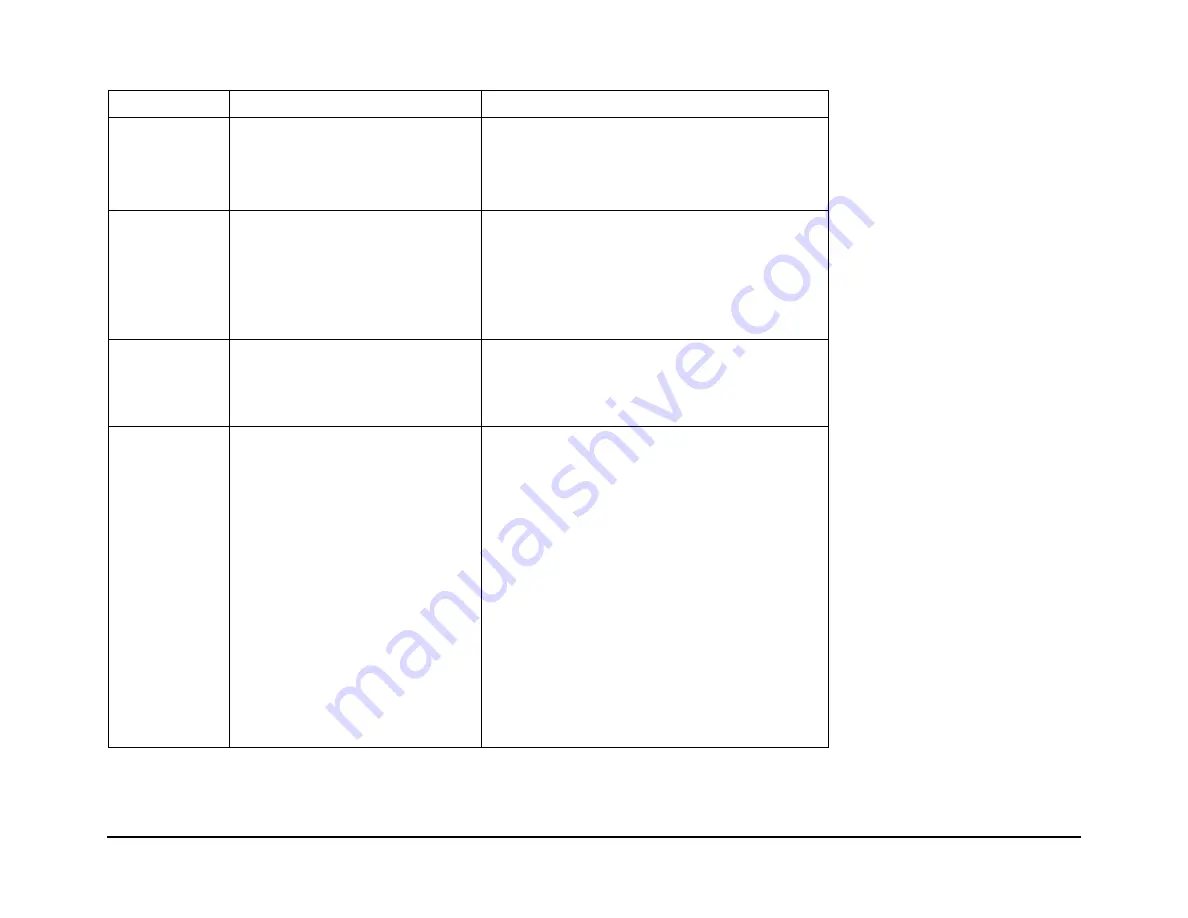
WorkCentre 385
General Error Repair Procedures
12/98
2 - 4
General Error Repair Procedures
Error Status
Check
Solution
No Power
See also “No
Power” Trouble-
shooting Flow.
1.
Check wall power
2.
Check power fuses F1, F2 & F3.
1.
If power differs from machines power rating,
have it corrected.
2.
Replace open fuses.
Fuser Error
See also “Fuser
Error” Trouble-
shooting Flow.
1.
Thermostat open
2.
AC wire open
3.
Thermistor open
4.
Engine PBA
1.
Detach AC connector and measure the
resistance between pin 1 and 2. Replace
thermostat if open.
2.
Check connector and wiring.
3.
Check thermistor, wire and connection.
4.
Replace Engine PBA.
Door Open or
No Toner
1.
When closing Top Cover, check
that the lever is pressed
2.
Micro switches open.
3.
CPU and related circuit
1.
Open top cover and press the lever. If
Controller detects the cover is closed, check
for mechanical problem in top cover and lever
assembly. If ok, check for electrical problem.
Jam 0
See also “Paper
Jam (mis-feed-
ing)” Trouble-
shooting flow.
Check where Jam 0 occurs.
1.
Paper is not picked up.
2.
Paper is located at feed sensor.
3.
Occurs when inserting specific
papers such as an envelope
into the MPF (Multipurpose
Paper Feeder)?
4.
Occurs when inserting specific
papers such as an envelope
into the Manual Feeder?
5.
Is the Stacker Extender folded
out?
6.
Does the Paper Guide Adjust
distort the paper.
1.
Check the solenoid.
2.
Check feed sensor.
Check if it is actuated by the paper width
sensor.
3.
Re-try inserting less paper.
- Fan the paper and align.
- Take out the loaded paper, and re-install in
reverse direction.
4.
Take out the loaded paper and re-install in
reverse direction.
- insert paper as recommended for Manual
Feeding?
- when loading, tap the paper until paper
detect sensor senses that paper is loaded.
5.
When using long paper, use the Extender.
6.
Adjust Guide.
www.printcopy.info
www.printcopy.info
Summary of Contents for WorkCentre 385
Page 2: ...www printcopy info w w w p r i n t c o p y i n f o...
Page 4: ...www printcopy info w w w p r i n t c o p y i n f o...
Page 20: ...WorkCentre 385 12 98 1 10 www printcopy info w w w p r i n t c o p y i n f o...
Page 50: ...WorkCentre 385 12 98 3 18 www printcopy info w w w p r i n t c o p y i n f o...
Page 100: ...WorkCentre 385 12 98 4 50 www printcopy info w w w p r i n t c o p y i n f o...
Page 134: ...WorkCentre 385 12 98 6 22 www printcopy info w w w p r i n t c o p y i n f o...
Page 182: ...WorkCentre 385 12 98 7 48 www printcopy info w w w p r i n t c o p y i n f o...