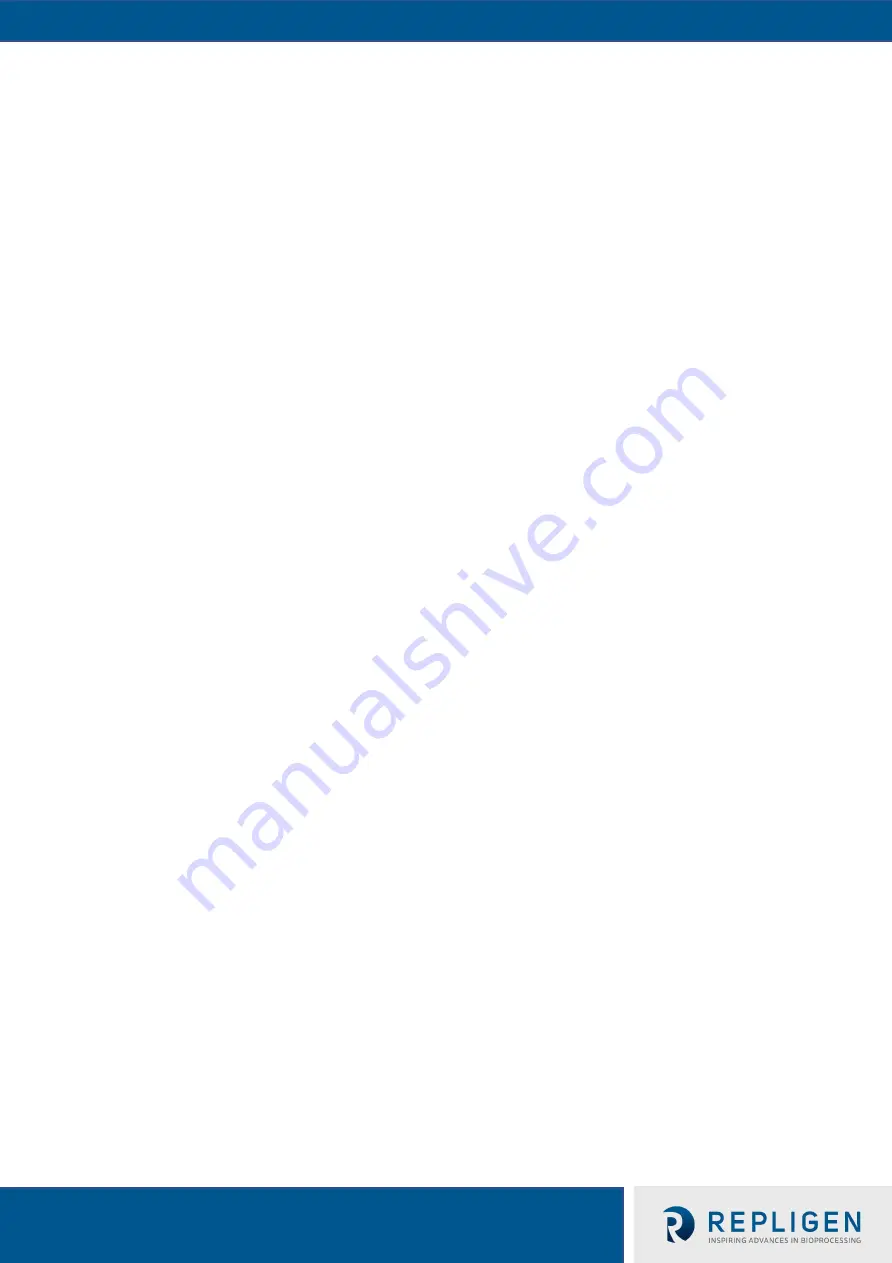
75
XCell
TM
ATF System with C410:V3 Controller
User Guide
Appendix 5: Profinet Communication
Set/Change IP Address of HMI
1.
HMI IP Address setting:
a.
Select settings from the start menu, select network and dial up connections, then
select PN_X1.
b.
From this interface, the IP Address, Subnet Mask and all other Ethernet
Properties can be adjusted.
2.
PLC IP Address setting:
c.
Select settings from the start menu (or go back to the setting screen) and select
Service & Commissioning.
d.
Select IP config by pressing the right arrow to reveal the 5
th
tab.
e.
From the Service & Commissioning screen, press the assign IP button.
f.
On the following screen select network, scan and start. “Scan is running”
appears at the bottom of the window.
g.
After the scan is complete, the S7-1200 device should appear. Select the S7-
1200 device and the device fields populate with the current configuration.
h.
From this interface, the IP Address, Subnet Mask and all other Ethernet
Properties can be adjusted.
i.
Once the values have been entered, select device, download and IP to assign the
address to the device. “IP suite settings could be assigned” appears at the
bottom of the window.
j.
Exit out of the assign IP
3.
Set Connection between HMI and PLC:
k.
From the Service & Commissioning screen, press the set connection button.
l.
On the following screen press the Find Online button. After the scan is complete,
the S7-1200 device should appear. Select it, and the IP Address box below
contains the PLC’s address. Note: It can also be entered manually.
m.
Press OK to accept and close the window.
n.
Press Save to set the connection. “Save is successful” appears at the bottom of
the window.
o.
Close the window to exit.
p.
Close the Service & Commissioning window.
q.
Close the Settings Window
4.
Start the program again and ensure that ‘####’ do not appear in the main screen fields.