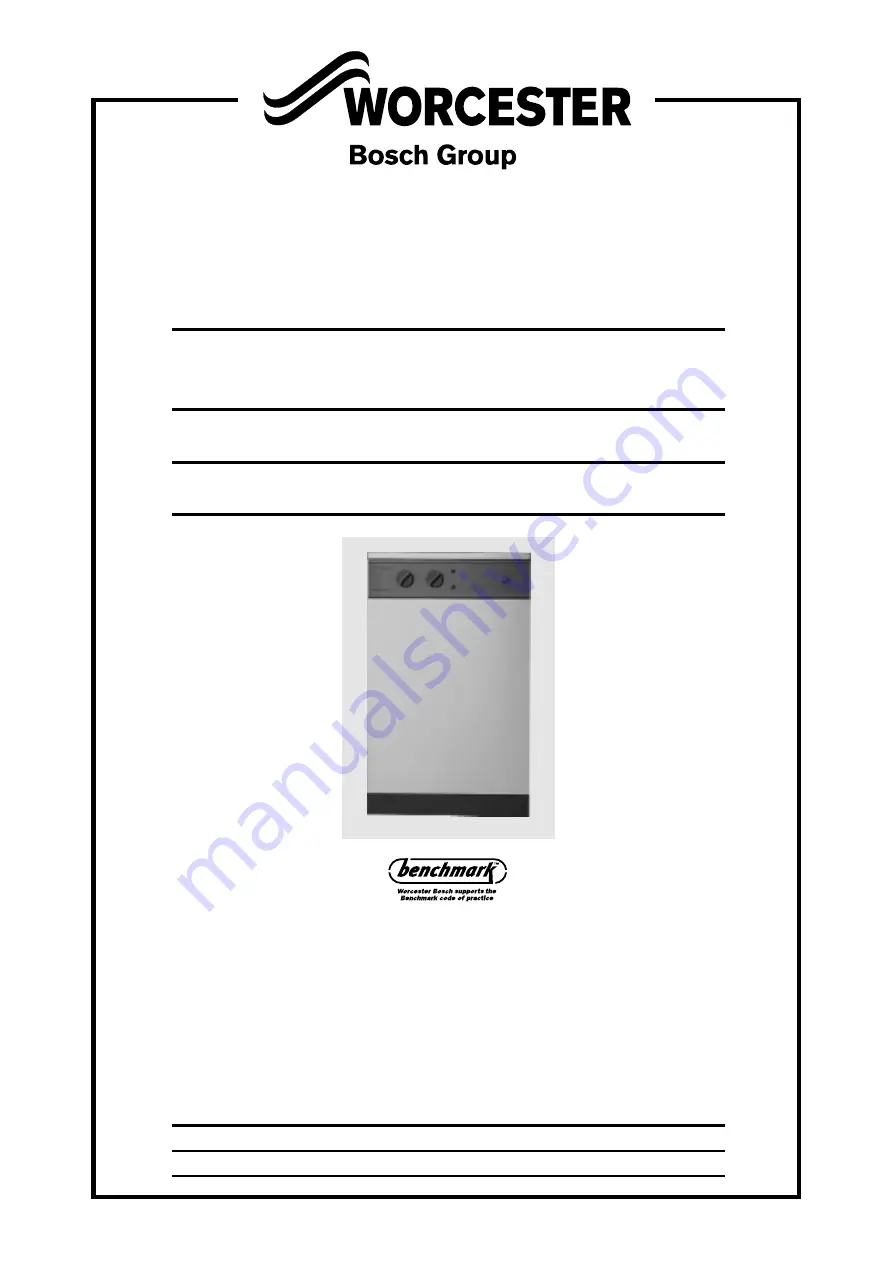
OIL HEATSLAVE
12/14 15/19 20/25 26/32
CONVENTIONAL FLUE AND ROOM SEALED BF FLOOR
STANDING COMBINATION BOILER FOR CENTRAL
HEATING AND MAINS FED DOMESTIC HOT WATER
INSTALLATION AND
SERVICING INSTRUCTIONS
BOILER OUTPUT
Domestic Hot Water and Central Heating
12/14
MINIMUM 12 kW
(41,000 Btu/h)
MAXIMUM 14 kW
(48,000 Btu/h)
15/19
MINIMUM 15 kW
(51,000 Btu/h)
MAXIMUM 19 kW
(65,000 Btu/h)
20/25
MINIMUM 20 kW
(68,000 Btu/h)
MAXIMUM 25 kW
(85,000 Btu/h)
26/32
MINIMUM 26 kW
(89,000 Btu/h)
MAXIMUM 32 kW
(109,000 Btu/h)
THESE INSTRUCTIONS APPLY TO UK MODELS ONLY
THESE INSTRUCTIONS ARE TO BE LEFT WITH THE APPLIANCE