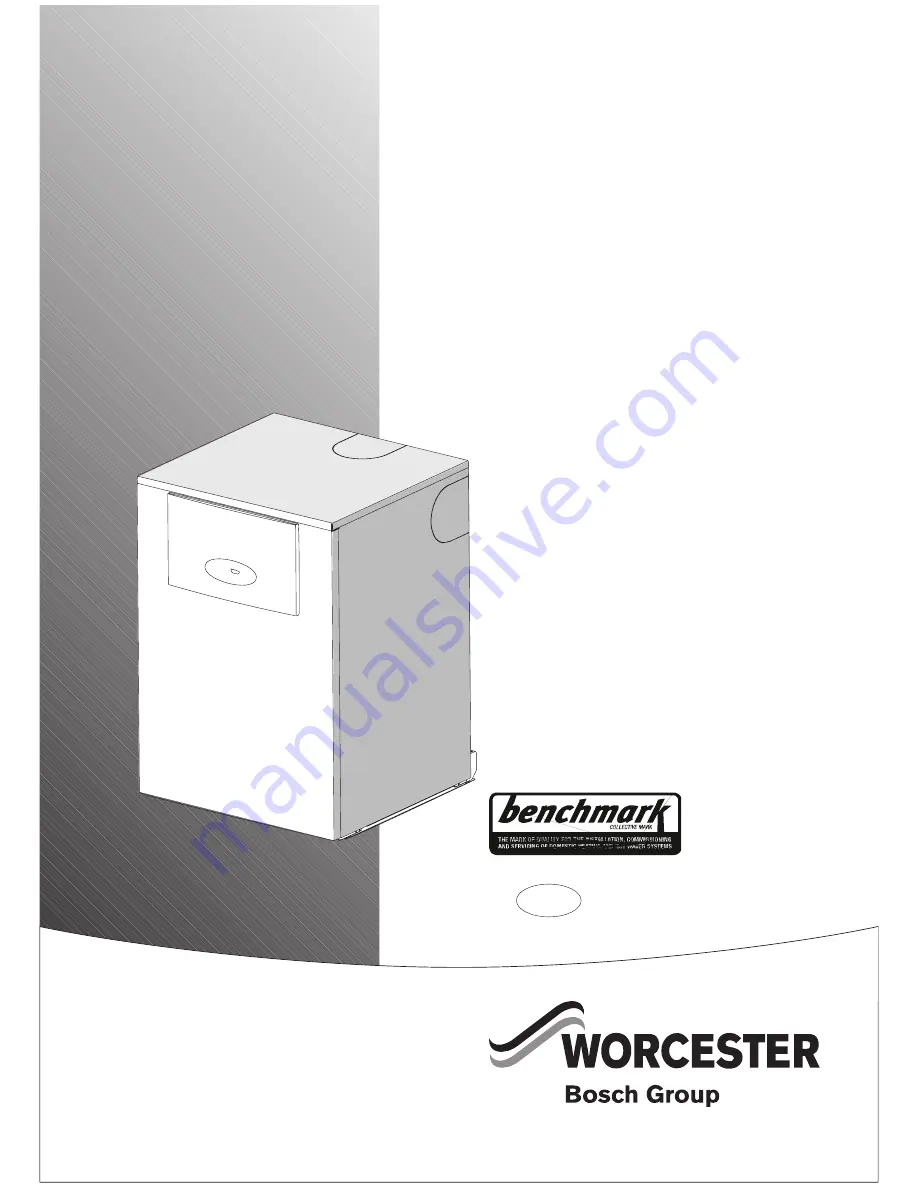
UK/IE
INSTRUCTION MANUAL
INSTALLATION COMMISSIONING & SERVICING
8 716 115 219c (03.2010)
THE APPLIANCE IS FOR USE WITH
NATURAL GAS OR L.P.G. (Cat II 2H3P TYPE C13, C33 & C93)
NATURAL GAS:
GREENSTAR HIGHFLOW 440CDi GC NUMBER 47-406-24
GREENSTAR HIGHFLOW 550CDi GC NUMBER 47-406-25
LIQUID PETROLEUM GAS:
GREENSTAR HIGHFLOW 440CDi GC NUMBER 47-406-26
GREENSTAR HIGHFLOW 550CDi GC NUMBER 47-406-27
GREENSTAR
HIGHFLOW 440CDi & 550CDi
FOR SEALED CENTRAL HEATING SYSTEMS AND MAINS FED DOMESTIC HOT WATER
FLOOR STANDING RSF GAS-FIRED CONDENSING COMBINATION
BOILER