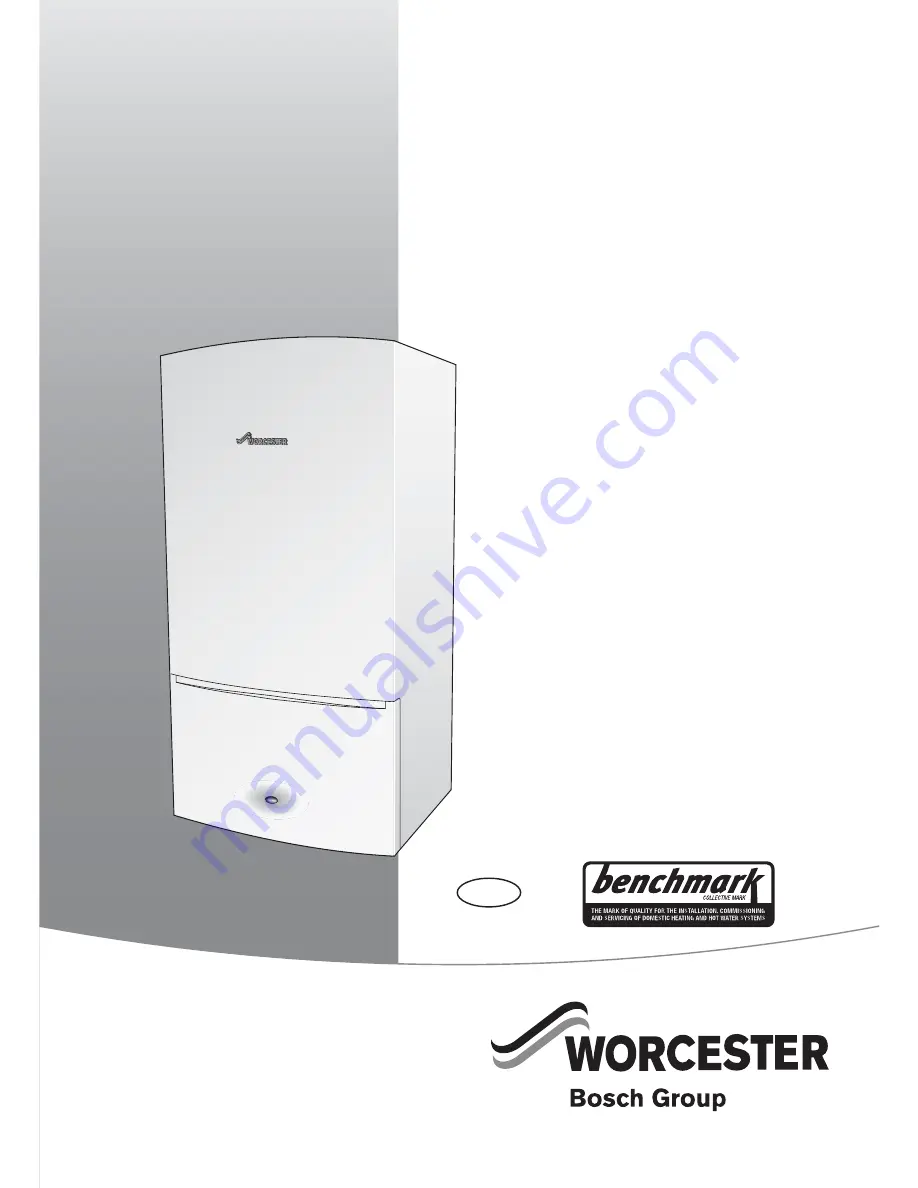
UK/IE
INSTALLATION COMMISSIONING AND SERVICING INSTRUCTIONS
WALL HUNG RSF GAS FIRED CONDENSING COMBINATION BOILER
Greenstar CDi Compact
6720646608-00.1W
o
FOR SEALED CENTRAL HEATING SYSTEMS AND MAINS FED DOMESTIC HOT WATER
6 72
0 803 800 (2012/11)
The appliances are for use with:
Natural Gas or L.P.G. (Cat.II 2H 3P type C13, C33 & 53)
Natural Gas: 28CDi Compact GC number 47-406-44
32CDi Compact GC number 47-406-46
36CDi Compact GC number 47-406-48
L.P.G.: 28CDi Compact GC number 47-406-45
32CDi Compact GC number 47-406-47
36CDi Compact GC number 47-406-49