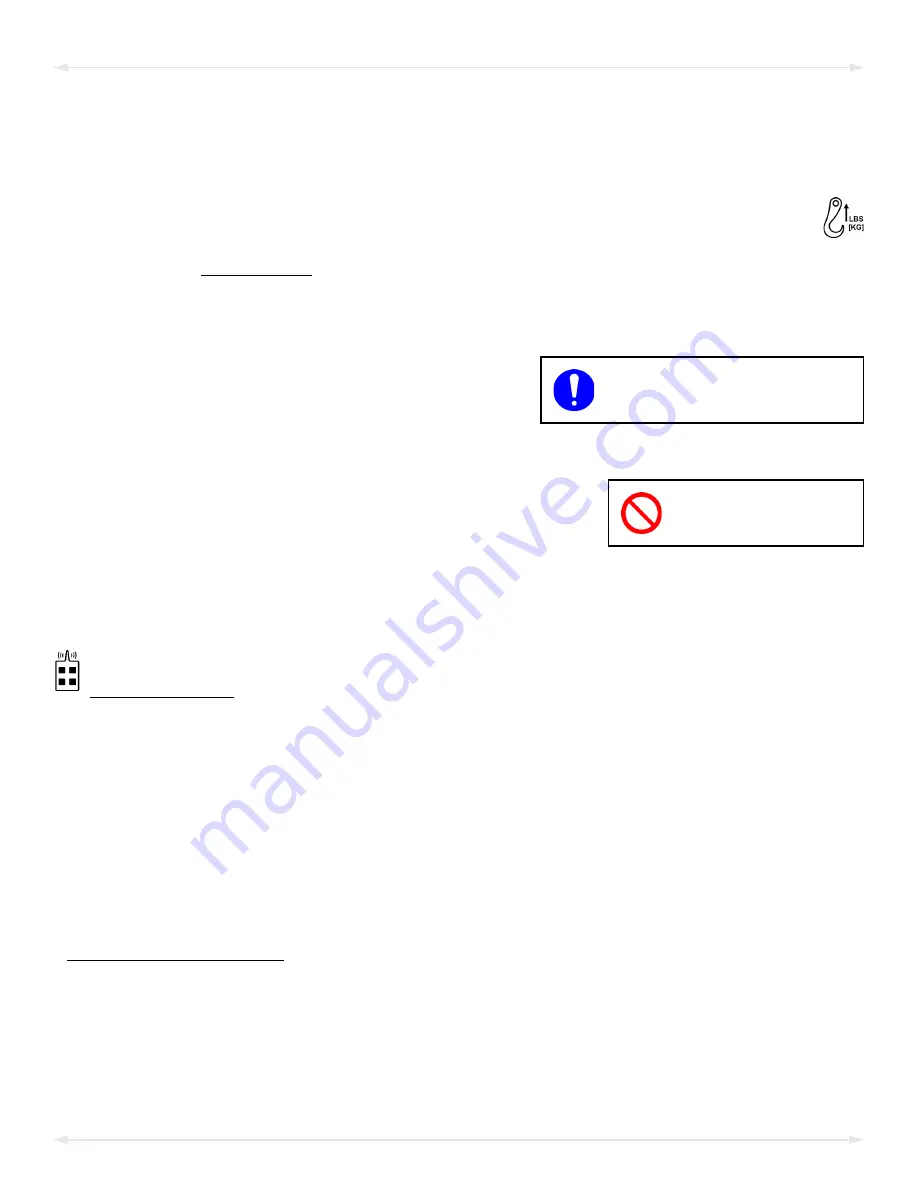
Rev 1.1/1-20
P1-02DC3: #35122
27
Rated Load Test
1
The following steps must be performed or supervised by a qualified person:
2
1) Use a test load that weighs 125% (± 5%) of the Maximum Load Capacity and has the
appropriate “L
2) Attach the vacuum pads to the load as previously directed.
3) Position the load to produce the greatest stress on the lifter consistent with “INTENDED
4)
Take precautions in case
load should fall during test.
Raise the load a minimal distance and leave it
suspended for 2 minutes.
5) Once the test is completed, lower and release the
load as previously directed.
6)
Never use lifter that
has failed test.
Inspect the lifter for any stress damage, and repair or
replace components as necessary to successfully pass the
test.
7) Prepare a written report of the test and keep it on file.
Remote Control System Test
If the lifter has a Remote Control System, test it where the lifter is normally used. Use the
radio transmitter to activate each of the remote functions.
3
Vary the transmitter's direction
and distance from the lifter, to make sure transmissions are effective.
4
If the Remote Control System is not functioning correctly, ...
• the battery for the radio transmitter may need to be replaced, or;
• metal or other electrically conductive surfaces may be causing radio interference.
Reposition the transmitter to transmit signals effectively.
If the problem persists, vary the test conditions, to determine whether there is transmission
interference in the work environment or the Remote Control System is not functioning. Correct
any fault before using the Remote Control System.
1..... An equivalent simulation may also be used. Contact WPG for more information.
2..... A “qualified person” has successfully demonstrated the ability to solve problems relating to the subject matter and work, either by possessing a
recognized degree in an applicable field or a certificate of professional standing, or by possessing extensive knowledge, training and experience.
3..... Use a test material with appropriate “L
” (see page 9) to test the “attach” and “release” functions.
4..... This may require assistance from someone near the lifter, to verify functions are working as intended.
INSPECTIONS AND TESTS
Summary of Contents for P110C02DC3
Page 2: ...P1 02DC3 35122 Rev 1 1 1 20 2 ...
Page 6: ...P1 02DC3 35122 Rev 1 1 1 20 4 Note A standard P110L02DC3 is shown SPECIFICATIONS ...
Page 41: ...Rev 1 1 1 20 P1 02DC3 35122 39 ...
Page 42: ...P1 02DC3 35122 Rev 1 1 1 20 40 ...
Page 43: ...Rev 1 1 1 20 P1 02DC3 35122 41 ...
Page 44: ......
Page 45: ......
Page 46: ......
Page 47: ......
Page 48: ......