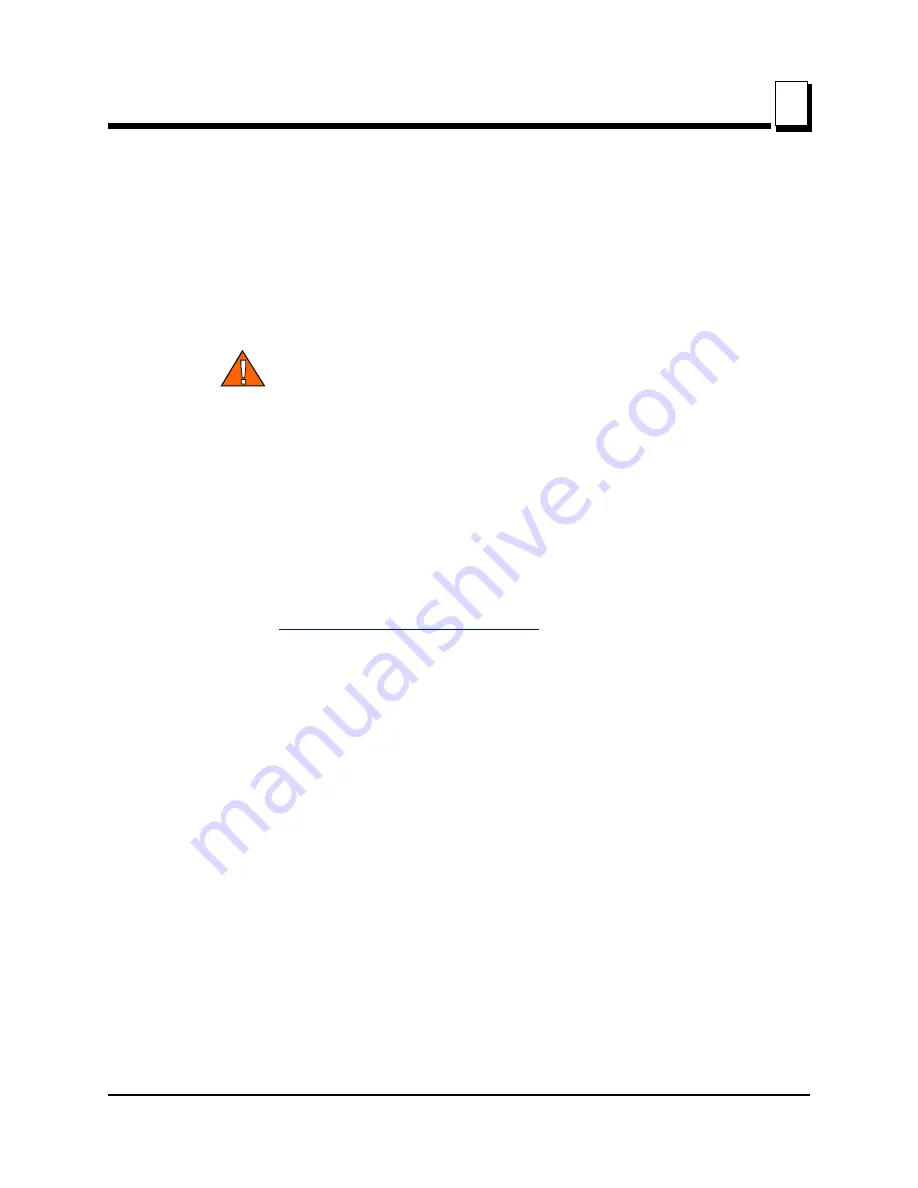
Maintenance
Setter Calibration
Maintenance
SISdoc112009
3-1
3
SECTION 3 MAINTENANCE
3.1
Setter Calibration
To calibrate:
1.
Clean each clamp block with air. If oily, wipe dry with a clean rag.
WARNING!
Never spray a liquid on or near the sensor
assembly.
2.
Inspect the blocks for chips and/or other damage. Replace if necessary.
3.
Place the calibration plate into the clamp assembly. Position the calibration plate so the
top of the plate is slightly above the top of the sensor pin.
4.
Press the F1 Clamp button on the control panel to clamp the calibrate plate.
5.
Press the F5 Zero Calibrate button to calibrate the setter.
NOTE:
If the "Error -- CAL Clamp Zero CAL Block" message appears, you need to adjust
the sensor first.
See Section 4.1 Sensor Adjustment
, for the adjustment procedure.
6.
With the calibration plate still clamped, manually retract the sensor pin and insert the
.024" diameter gauge pin between the calibration plate and the sensor pin. If the display
does not indicate .024 (±.001), the sensor is malfunctioning and should be replaced.
7.
Hold the calibrate plate with the tips of your fingers. Press the F1 Clamp button to
unclamp the calibration plate. Remove the calibration plate.
3.2
Miscellaneous
1.
Check the chain every 40 hours of operation. Lubricate if needed.
2.
Check chain tension periodically. Adjust the chain tension if necessary.
3.
Grease the threads on the up/down height adjustment rods with a heavy axle grease
every 40 hours of operation.