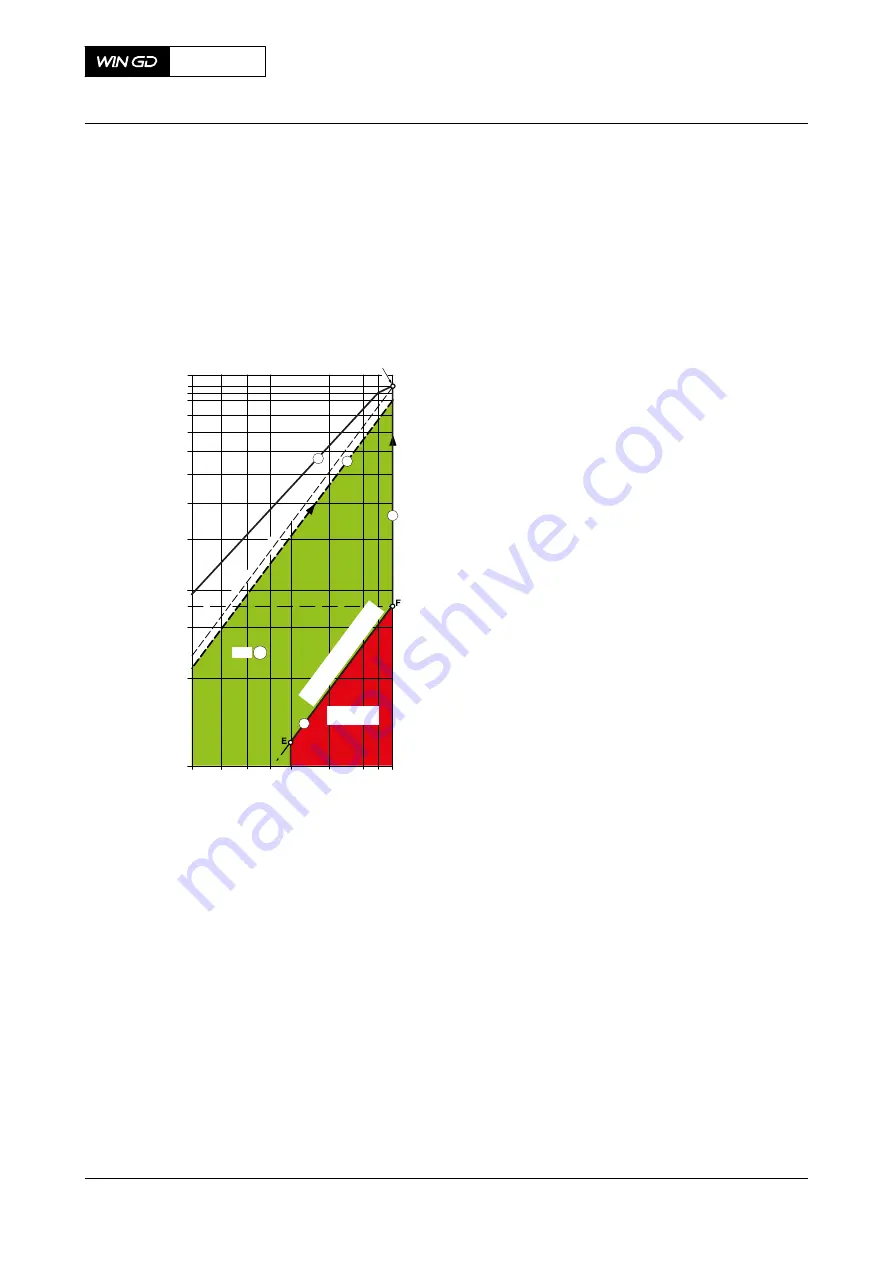
3.3.3
Controllable pitch propeller (CPP)
3.3.3.1
Load ranges
After engine start, the engine operates at an idle speed of up to 70% of the rated engine speed
with zero pitch. From idle speed, the propeller pitch must be increased with constant engine
speed to the minimum at point E, the intersection with Line 9 (see
).
Fig 3-7
Schematic diagram - Relation Speed/ Power (CPP)
Engine speed [% Rx]
Engine power [% Rx]
CMCR [Rx]
5
10
15
20
30
17
40
50
60
60
65
70
80
90
100
70
80
90
100
110
nominal
propeller
characteristic
55
50
7
A
Field
prohibited
operation area
zero pitch propeller
characteristic
(zero thrust)
5
6
8
00116
•
Line 9 is the bottom load limit between 70% and 100% speed, with a pitch position that at
100% speed, is the minimum power at point F is 37%. The formula shown in paragraph 1
is used for this calculation.
•
Along Line 8, the power increase from 37% (point F) to 100% power (CMCR) at 100%
speed is the constant speed mode for the shaft generator operation.
•
Line 5 is the top load limit and relates to the permitted torque limit.
•
The area between 70% and 100% speed and between Line 5 and Line 9 shows the area
that an engine with a CPP must be operated.
•
Line 7 shows a typical combinator curve for variable speed mode.
Maneuvering at maximum speed with low or zero pitch is not permitted. Thus, installations with
main engine-driven generators must have a frequency converter when electrical power is to be
supplied (eg to thrusters) at constant frequency during maneuvering. As an alternative, power
from auxiliary engines can be used for this purpose.
For test purposes, the engine can be operated at rated speed and low load during a one-time
period of 15 minutes on the testbed (eg NO
x
measurements) and 30 minutes during dock trials
X92DF
AA00-0000-00AAA-042B-A
Operation Manual
The relation between engine and propeller
Winterthur Gas & Diesel Ltd.
- 75 -
Issue 002 2020-08