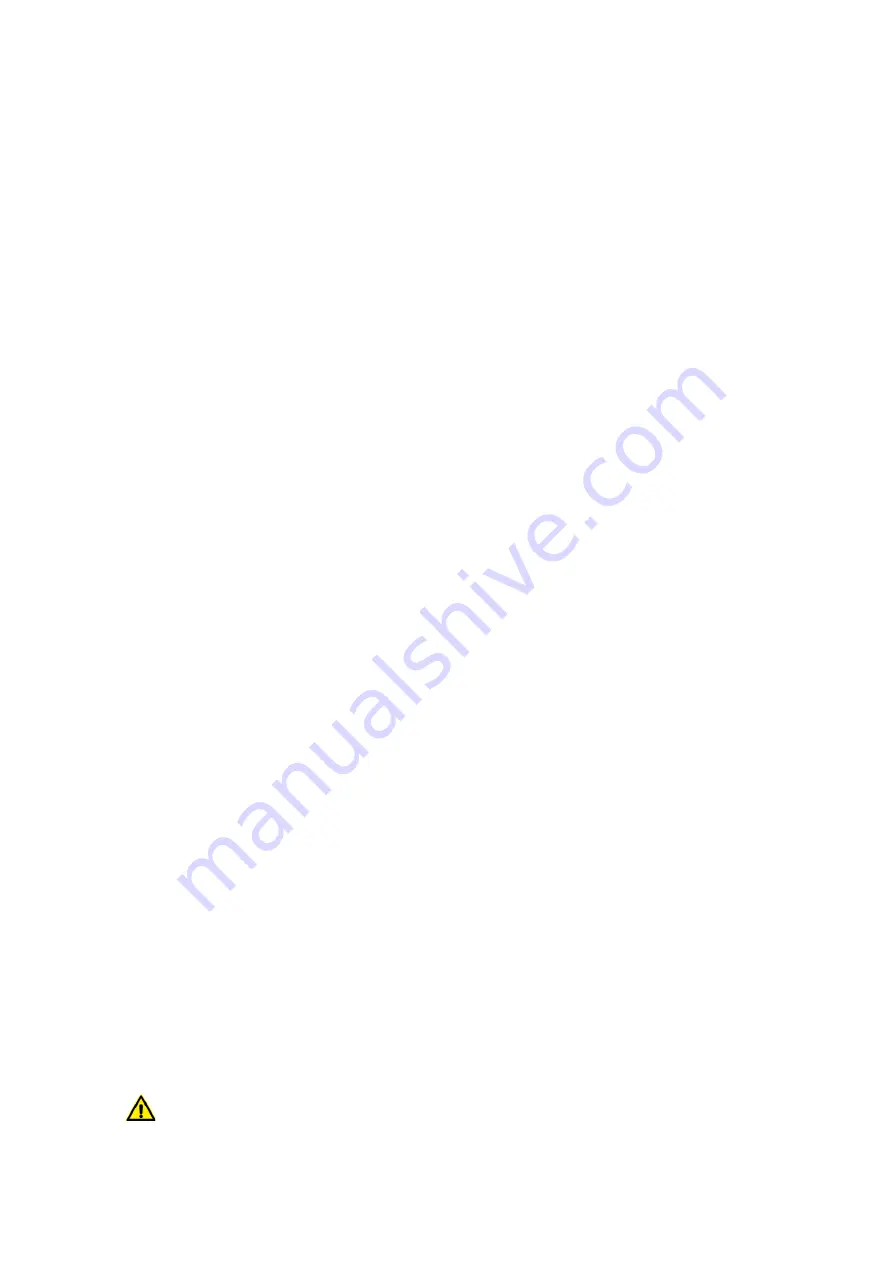
English
42
WILO SE 10/2013
9.1 General position from maintenance
• General inspection of the unit (including water
and power supplies) to check the apparent condi-
tions of all components
• General Cleaning
• Tightness control of non-return valves
• Check the operating configuration of the electri-
cal panel
• Check the correct operation of alarm pilot lights
on the control panel
• Check the correct operation of the minimum tank/
well level alarm
• Check electrical connections to see if there are no
signs of insulation damages, burning, loosening of
terminals
• Check the electric motors insulation resistance.
When it is cold, an engine without isolation dam-
ages must have a resistance of more than 1000
megohm.
• Check the pre-inflation of membrane tanks.
• See also specific operations indicated in the par-
ticular instructions manuals for the various com-
ponents of the booster.
• Check if minimum service equipment supply,
required by the EN 12845 standard for the quick
restoration of the fully working order of the sys-
tem in case of failure, is held in stock.
• Check the correct functioning of the minimum
fuel level alarm.
• Check the correct functioning of engine oil heater
resistor.
• Check the battery charge level and the efficiency
of the battery charger.
• Check the correct functioning of the stop solenoid
valve (fig. 11).
• Check the pump cooling oil level and viscosity.
• Check the priming circuit (especially for unit
above the level of water charge).
During all checks, the following points have to be
controlled:
a) All the different pressures of the manometer for
water and air of the buildings, pressures for main
pipes and pressure tanks.
b) All water levels in storage tanks, rivers, canals,
lakes (including pump priming tanks and under
pressure tanks).
c) The correct position of all the main gate valves.
9.2 Test of automatic start of pump
Tests on automatic pumps must include the fol-
lowing:
a) Control engine oil and fuel level.
b) Reduce the water pressure on starting device, in
this way simulating an automatic start request
(cf. chapter 8).
c) When the pump starts, the starting pressure must
be controlled and recorded.
d) Control the oil pressure on diesel pump and the
cooling circuit water flow.
CAUTION! Risk of malfunction of the pump!
Always top up fuel and other fluids after per-
forming the tests.
9.3 Test of automatic start of diesel pump
After testing the start, diesel engines must be
tested as follows:
a) Let the motor run for 20 min, or for the time
recommended by the supplier. Then, stop the
engine and immediately restart it by using the
test button ‘manual start’.
b) Control the water level in the primary cooling
circuit.
During the test, you must check the oil pressure,
the engine temperature and the coolant flow.
Then control the oil hoses and make a general
check to detect any possible fuel, coolant or
exhaust smoke leakage.
9.4 Periodic tests
Monthly checks
Control level and density of the electrolyte of all
lead storage battery cells (including diesel engine
starting batteries and batteries used to the elec-
trical control panel power supply). If the density is
low, check the battery charger, and if it is correctly
working, replace the battery in failure.
Quarterly checks
To perform it maximum every 13 weeks
An inspection report must be recorded, signed and
given to the final user. This must include details of
each procedure carried out or planned, details of
external factors, such as weather conditions,
which could have influenced the results.
Check the pipes and supports to check the possi-
ble corrosion points and protect them where if
necessary.
Check pipes for correct earth connection.
Sprinkler pipes cannot be used for electrical
equipment earth connection. Remove all of this
kind of connection and implement an alternative
solution.
Check each water supply on each control station
of the system. The pump(s) should automatically
start, pressure values and measured flow cannot
be less than that reported values on the project.
Each change must be recorded.
Check all valves that supply sprinklers with water
in order to be sure they are working. Then return
them to their normal running position. Realize the
same operation for all the water supply valves, the
control and alarm valves and all local or auxiliary
valves.
Check and control the amount and packaging of
spare parts that are in stock.
Semi-annual checks
To perform it maximum every 6 months
Check the alarm system and remotely alarm sys-
tem report to the central supervision.
Summary of Contents for SiFire
Page 2: ...Fig 1 Fig 2a A 2 2 E B C D...
Page 3: ...Fig 2b Fig 3 21 25 26 13 11 12 19 15 22 27 20 24 23 2 1 14 4 16 7 5 6 10 18 17 9 9 10 8 3...
Page 4: ...Fig 4 Fig 5...
Page 5: ...Fig 6a 3 5 D D 4 D 2 3 C min max 1 8 m s Fig 6b min 3 5 D D 4 D max 2 m 2 3 C max 1 8 m s...
Page 6: ...Fig 7 Fig 8 max 3 2 m min A B C D 2 4 5 6 3 8 7 1...
Page 7: ...Fig 9a Fig 9b A B C D 800 800 800...
Page 8: ...Fig 1a Fig 9a variant Fig 9b variant A B C D 800 800 800...
Page 9: ...Fig 10 Fig 11 1 2 1 2 1...
Page 10: ......
Page 34: ......
Page 35: ......