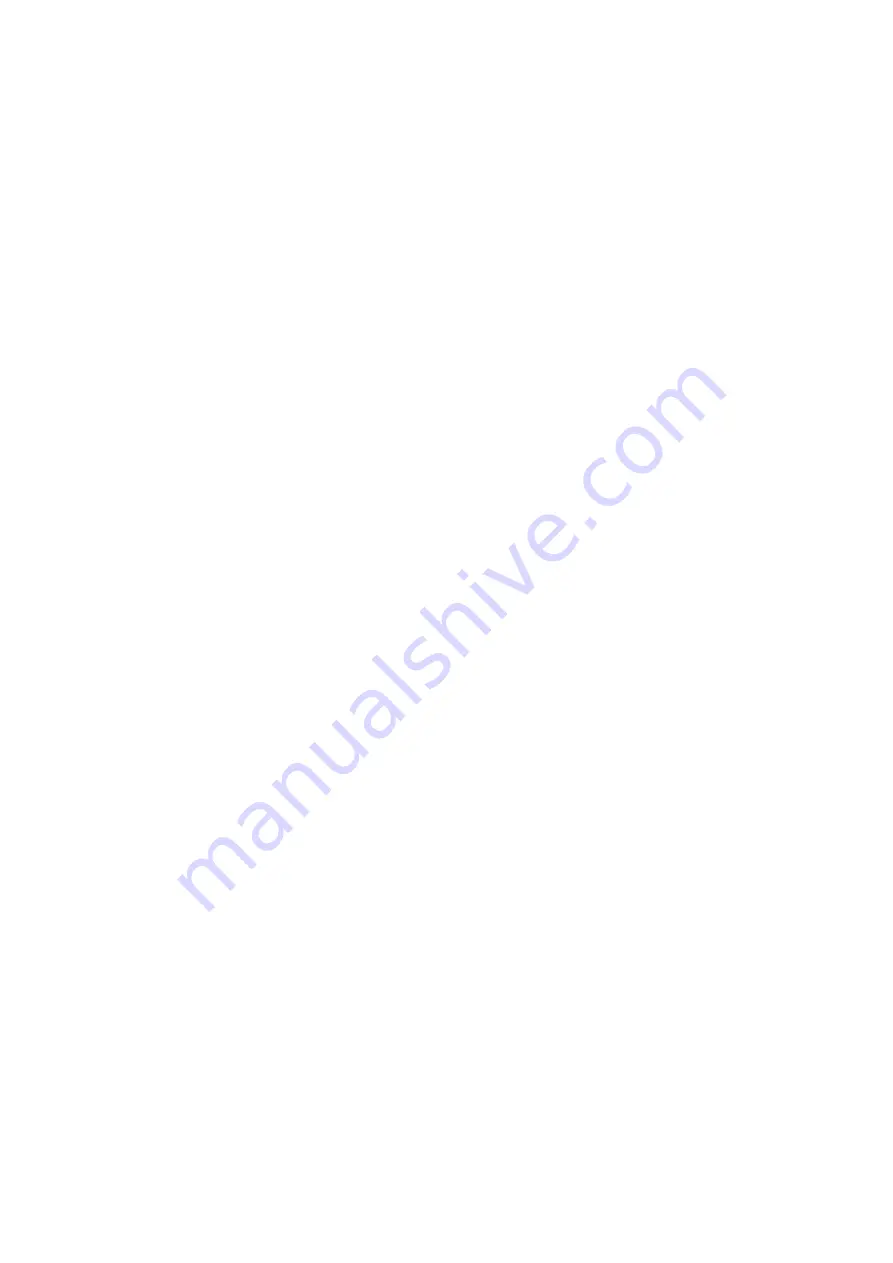
English
32
WILO SE 10/2013
5.3 Scope of delivery
• Fire Extinguishing Booster
• Operating instructions for fire extinguishing sys-
tem.
• Operating instructions for pumps (1 manual per
kind of pump)
• Operating instructions for panels (1 manual per
kind of panel)
• Operating instructions and maintenance of diesel
motor if present.
5.4 Accessories
• Priming tank(s) complete with electrical float.
• Electric contacts limit for the check valve of the
pumps.
• Flexible vibration-damping sleeves.
• Eccentric suction cone kit with vacuum gauge for
suction side of the pumps.
• Butterfly valves.
• Silencer for diesel engine.
• Water/water heat exchanger for diesel engine
cooling.
• Flow meter.
• Diesel engine spare parts kit.
• Remote alarm panel.
The installer is responsible for the assembly of the
equipment supplied and for completion of the
system in compliance with the requirements of EN
12845 standards, as well as for integration of our
supply with all other necessary components (cir-
culation piping, flow rate metering circuits with
meter, priming tank, etc).
See the specific instructions provided in the rele-
vant instruction manuals and/or the indications
provided on the items themselves for details of
how to assemble, set and adjust the accessories
listed above or other particular accessories
requested at the order stage and supplied with the
standard pumping unit.
The installer is responsible for issuing the final
certification “installation built-in compliance with
EN 12845 standard”, as required by the relevant
standards, and for issuing the end user with all the
documents required by the applicable standard.
6 Description and function
6.1 General description
The fire extinguishing units in the SiFire series are
built in several variants and models, as indicated in
our catalogues, or in versions modified in order to
satisfy particular customer requirements (trans-
port/handling difficulties, particular perform-
ances, etc), using the main components described
below:
• main normalised “back pull out” pumps, coupled
to an electrical motor or diesel engine by a spacer
allowing the dismantling of the pump and/or
motor without having to work on the other. It also
allows the extraction of the rotating part of the
pump for maintenance without having to remove
the motor and/or the end suction pump housing.
• vertical multistage jockey pump for correcting
small losses and for keeping the system pressure
constant.
• electrical control panels for the main and jockey
pumps (one per pump).
• piping and discharge manifolds in steel.
• valves on the pump discharge that can be locked
in the open position.
• non-return valves on the pump discharge.
• butterfly valves, manometers, pressure switches.
• Connection for flow meter to control the perform-
ance of the pumps.
• double pressure switch circuit for start-up of the
main pumps and control of the working order of
each individual pressure switch.
• pressure switch for automatic start-up of the
jockey pump.
• support frame(s) for control panels and manifolds.
• independent fuel tank for the diesel engine, com-
pleted with accessories.
• Two batteries for the start-up of the diesel engine
(if present).
The system is assembled on a base frame in
accordance with the EN 12845 standard, within
the limit of delivery, indicated on installation dia-
gram from fig. 2a-2b.
Each pump is installed on a steel base frame. Die-
sel pumps are connected to hydraulic elements
with intermediary vibration damping joints to
avoid the transmission of vibrations from diesel
motors but also the possible piping or mechanical
structure breaks.
For connection to the public water distribution,
rules and existing standards must be respected,
and possibly completed with rules of water distri-
bution companies. Besides, local particularities
have to be taken into account, for example a too
high or too variable suction pressure which
requests the assembly of a pressure reducing
valve.
Summary of Contents for SiFire
Page 2: ...Fig 1 Fig 2a A 2 2 E B C D...
Page 3: ...Fig 2b Fig 3 21 25 26 13 11 12 19 15 22 27 20 24 23 2 1 14 4 16 7 5 6 10 18 17 9 9 10 8 3...
Page 4: ...Fig 4 Fig 5...
Page 5: ...Fig 6a 3 5 D D 4 D 2 3 C min max 1 8 m s Fig 6b min 3 5 D D 4 D max 2 m 2 3 C max 1 8 m s...
Page 6: ...Fig 7 Fig 8 max 3 2 m min A B C D 2 4 5 6 3 8 7 1...
Page 7: ...Fig 9a Fig 9b A B C D 800 800 800...
Page 8: ...Fig 1a Fig 9a variant Fig 9b variant A B C D 800 800 800...
Page 9: ...Fig 10 Fig 11 1 2 1 2 1...
Page 10: ......
Page 34: ......
Page 35: ......