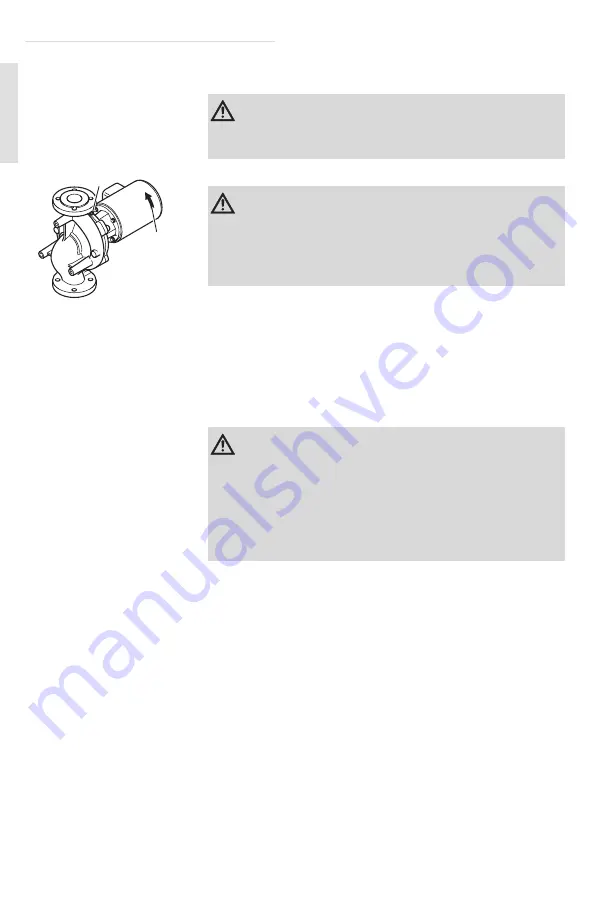
12
Wilo AG 05/2007
Englis
h
Installation
6.3 Fill and ventilate
Ventilate
1.
Open air vent valve (1) 1/2 turn, do not remove
.
2.
Completely open suction side and discharge side isolation
valves.
3.
Wait until the liquid has exited the ventilation opening and
until bubbles no longer form.
4.
Tightly close the ventilation opening.
Avoid cavitation
5.
Ensure that the minimum pressure stipulated in the product
catalog is present on the suction side.
Check direction of rotation
6.
Check the motor's direction of rotation by briefly turning it
on. The direction of rotation is correct if the fan or other
visibly rotating parts of the pump are rotating in the direction
of the arrow (2).
On three phase only, if the direction of rotation is incorrect,
have an electrician correct it by swapping two phases.
For single phase applications, to change direction of the
motor please follow the directions supplied with the motor.
If there is not arrow on the motor run the pump, note pres-
sure, reverse rotation and recheck pressure. The rotation that
produces a higher pressure is the correct rotation (for clarifi-
cation contact WILO).
7.
Turn on the pump for test operation and observe whether it
is pumping correctly. If necessary, ventilate again until a
sufficient pumping result is achieved.
Caution: Damage due to dry running!
The pump may never be allowed to run dry. Dry running destroys
the mechanical seal.
1
2
Warning: Danger due to hot liquid under pressure!
Extreme caution must be used when venting systems that have
elevated temperatures and/or dangerous fluids. Maintain suffi-
cient distance from the air vent opening, wear suitable clothing
including protective glasses/facial protection and gloves.
Caution: Damage due to cavitation!
Failing to maintain minimum pressure on the suction side can to
lead to cavitation accompanied by noise.This can damage the
pump. This minimum inlet pressure depends on the operating
conditions and the duty point of the pump and must be calcu-
lated accordingly. Please contact WILO or your WILO distributor
if this further information is required.