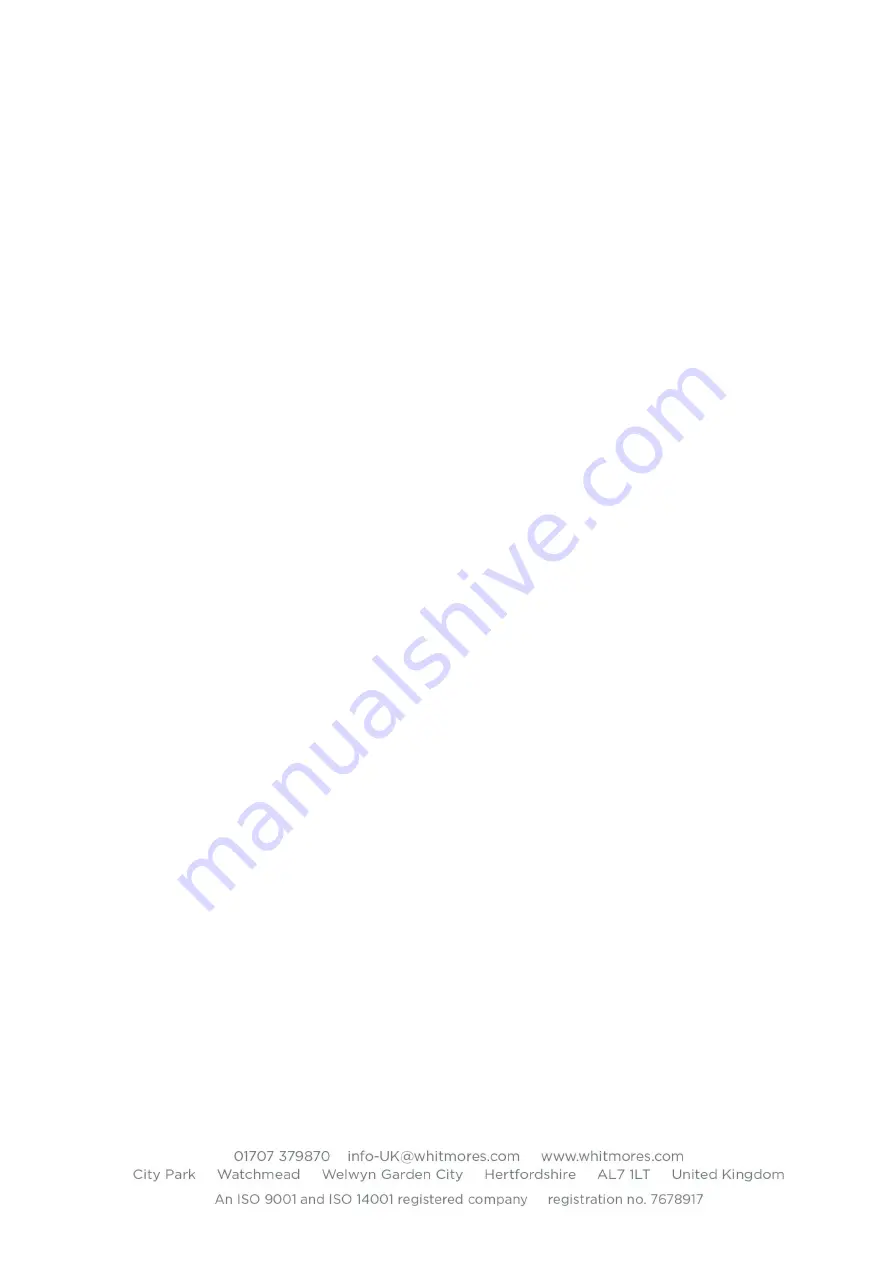
15
Note: If the plunger is being raised, it should only be raised by 0.25mm at a time and must be inspected
on the following shift. However, if the plunger height is known to have dropped they may be
reset to their original height, but a follow up inspection must still be made on the following shift.
The Plunger height should be adjusted up (to increase grease output) or down (to decrease
grease output), to suit local traffic / wheel pattern.
7.5
Checking for Airlocks
7.5.1
The following shows steps taken to check for airlocks.
Remove the delivery hose from the pump outlet.
Using the 10mm “T” bar, depress the plunger downwards several times.
If the plunger has no resistance, and / or there is no grease flow, the pump is probably air
locked.
Record the results.
If the test was not satisfactory, clear the air lock. The easiest method is by loosening the air
bleed screw until the groove on the threaded section is exposed. Using the 10mm “T” bar,
depress the plungers downwards several times; do not exceed the permissible plunger travel.
Record the results.
If the attempt to clear the airlock was not satisfactory check that there is a grease flow from
the reservoir.
7.5.2
Air locks that are present on arrival at the lubricator will give you certain information into
why the lubricator has not had a sufficient grease output.
7.5.3
If the lubricator has not used any or enough grease required for that particular lubricator
but air locks are present, plunger must not be raised, as due to the air locks, the lubricator
would have not been working.
7.5.4
If the lubricator has not used any grease, but no air locks are present other corrective
actions should be undertaken.
7.6
Checking for Defective Plunger and Plunger Spring
7.6.1
The operation test of this section should be made into two parts:
Firstly, by using the pump pliers, grip the plunger and move the plunger up and down to ensure
that there is no free movement of the plunger or plunger return spring.
The second test is using the 10mm “T” bar to depress the plunger. Ensure that the return of the
plunger is not too slow and in addition check that it’s returning fully after every depression.
IMPORTANT NOTE: Do not fully depress plunger to avoid damage.
Record the results of the test.
If the test is not satisfactory then the plunger and / or plunger return spring should be changed.
7.7
Checking for a Defective Outlet Non-return Valve
7.7.1
If the grease is flowing onto the spreader bar or out of the pump body outlet ports, when
the delivery hoses are removed, without the plungers being struck, the non-return valve
may be defective.
Summary of Contents for EasiPoint
Page 18: ...18 10Exploded Views of System Elements 10 1 EasiPump Schematic ...
Page 19: ...19 ...
Page 20: ...20 ...
Page 21: ...21 10 2 EasiPoint Schematic ...
Page 22: ...22 ...
Page 23: ...23 10 3 Blades ...
Page 24: ...24 ...
Page 25: ...25 10 4 Reservoirs ...
Page 26: ...26 ...
Page 27: ...27 ...