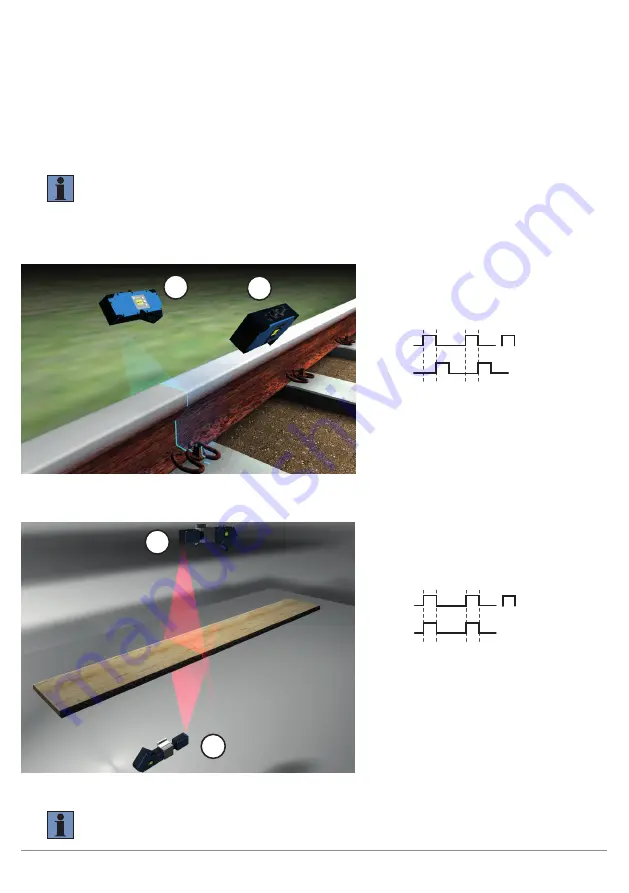
50
Integrated Web Server
6.3 Using More than One Sensor (synchronization)
It may be necessary to use more than one weCat3D in an application. This is fundamentally possible, but it
necessitates special wiring and sensor configuration depending on sensor array and how the sensors are
used.
Note!
The master (sensor 1 in this example) has to be in the “Encoder”, “Internal” or “Software”
profile mode, and the slave (sensor 2 in this example) has to be in the “syncIN” sync mode.
Example 1: Time-shifted measurement for extending the measuring range while avoiding reciprocal influence
of the sensors despite overlapping of the laser lines.
2
1
Figure 6: Sample Application, Rail Head Measurement
Example 2: Simultaneous measurement:
1
2
Figure 7: Sample Application, Thickness Measurement for Wooden Floorboards
NOTE!
The hardware trigger must have a pulse width of at least 10 µs.
Sample configuration:
Master, SyncOut (default setting I/O3)
connected to slave, SyncIn (default setting
I/O4).
Sensor 1
Sensor 2
Exposure Time
Sensor 1:
Sync mode (internal/encoder/software)
Exposure time: 200 µs
Sync out delay: 200 µs
Sensor 2:
Sync mode (syncIN)
Exposure time: 200 µs
Sample configuration:
Master, SyncOut (default setting I/O3)
connected to slave, SyncIn (default setting
I/O4).
Sensor 1
Sensor 2
Exposure Time
Sensor 1:
Sync mode (internal/encoder/software)
Exposure time: 200 µs
Sync out delay: 0 (default setting)
Sensor 2:
Sync mode (syncIN)
Exposure time: 200 µs