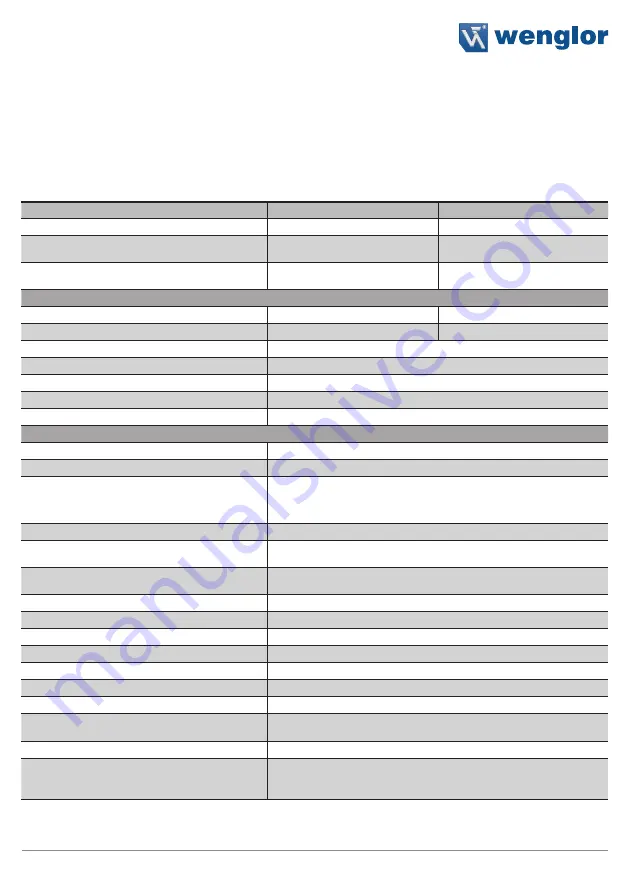
Safety Light Curtain
15
4. Technical Data
4.1 General Technical Data
For US and Canada:
Device to be supplied by a certified Class 2 power supply that complies with the requirements according NEC
and CEC.
Order no.
Finger protection
Order no.
Hand protection
Emitter
SEFG531…SEFG542
SEFG511...SEFG522
Receiver
SEFG631…SEFG642
SEFG671…SEFG682
SEFG611 ...SEFG622
SEFG651 ...SEFG662
Set
SEFG431…SEFG442
SEFG471…SEFG482
SEFG411 ...SEFG422
SEFG451 ...SEFG462
Optical data
Resolution
14 mm
30 mm
Range
0.25 m…7 m
0.25 m…20 m
Safety field height
150 mm…1800 mm
Aperture angle
± 2.5°
Wavelength emitter
typ. 630 nm
Coated optics:
Yes
Ambient light immunity (for continuous light) 10,000 Lux
Electrical data
Response time
Processing time muting signals
95 ms
Supply voltage
19.2…28.8 V DC (24 V DC +/–20 %)
(SELV-, PELV power supply unit), it must be possible to bridge
power failures of 20 ms (EN 60204-1)
Safeguarding the supply voltage, inputs
max. 2 A
Current consumption
(Ub = 24 V) receiver
≤
350 mA (without load)
Current consumption
(Ub = 24 V) emitter
≤
100 mA
Internal fuse
2 A
Temperature range
–30…55 °C
Storage temperature
–30…70 °C
Relative humidity
≤
95 %, non-condensing
Vibration resistance
5 g (10 to 55 Hz)
Shock resistance
10 g / 16 ms
Short-circuit proof
Yes
Reverse polarity protected and over-
load-proof
Yes
Protection class
III
Max. cable length*
< 35 m/0.25 mm²
< 50 m/0.34 mm²
< 72 m/0.50 mm²