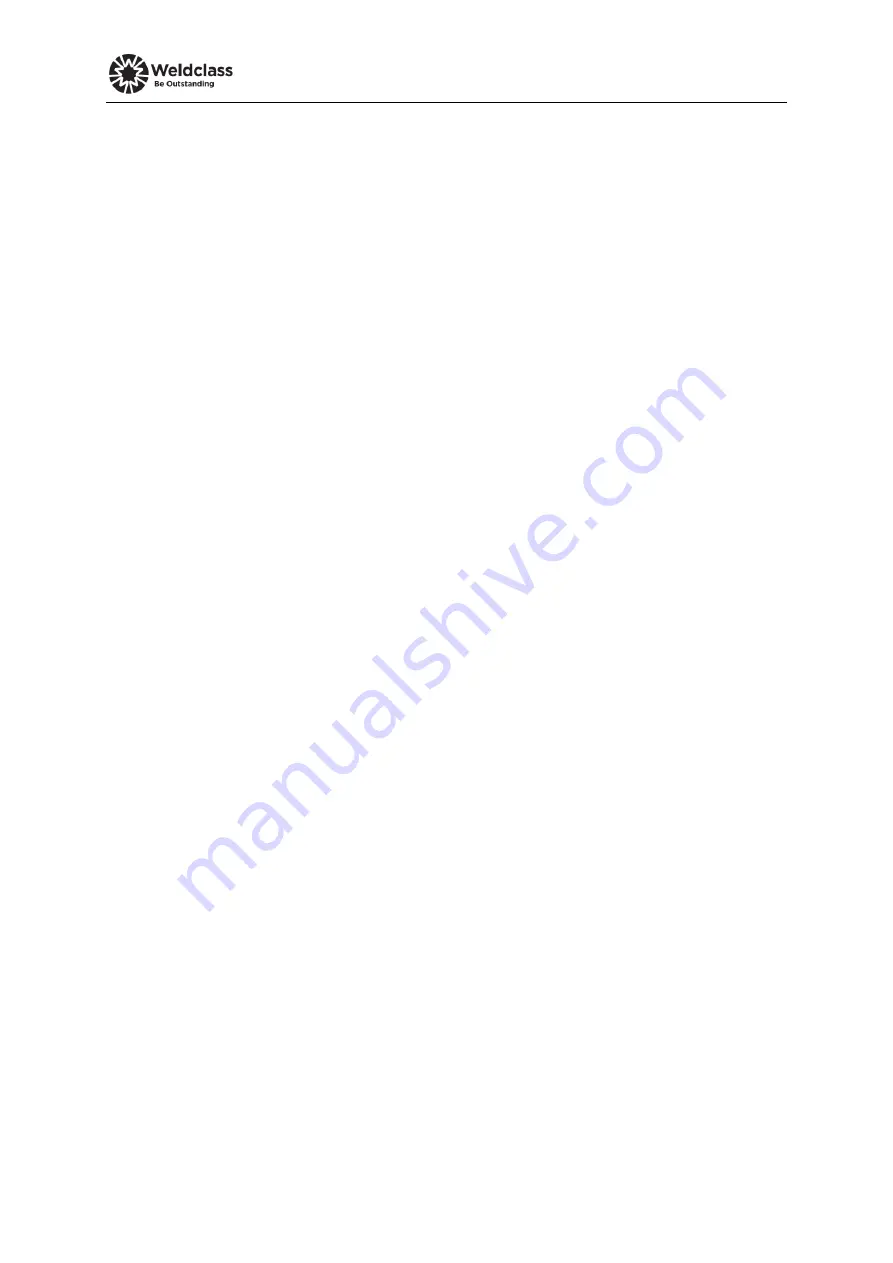
.
34
© Weldclass 2020 | E.&O.E.
10.2.2
The TIG Process
10.2.2.1
Description
The acronym TIG stands for Tungsten Inert Gas. Tungsten refers to the type of conductor (a tungsten
electrode) that is used to transfer the welding current to the job and create the arc. Inert Gas refers
to the fact that the process relies on an inert gas to prevent weld oxidisation.
Also referred to as Gas Tungsten Arc Welding (GTAW).
10.2.2.2
Process
In simple terms, TIG welding is probably most similar to oxy flame welding. However, instead of a
flame it uses an electrical arc to melt the job and filler metal, and instead of a preheat flame it uses
inert gas to prevent weld oxidisation. Like oxy flame welding, the filler metal is fed into the weld by
hand as required. Due to the fact that the current is not conducted to the job via the filler metal, (as
it is in MIG and MMA welding), the arc is much more controllable.
10.2.2.3
Advantages
Very low amperages can be achieved making this process ideal for welding thin materials. Also, due
to the independence of the arc and the filler metal application, TIG welding is very controllable and
can therefore achieve very high quality welds with excellent appearance. Unlike MIG and MMA
welding, TIG welding does not produce spatter so clean up is very minimal. It is typically used where
weld appearance is critical (e.g. handrails) or where weld quality is vital (e.g. pressure vessels or
pipes).
10.2.2.4
Limitations
Whilst TIG welding is very controllable, it can also be slower and more tedious than MIG or MMA
welding and it will generally not operate well on dirty or rusty materials meaning that additional
weld preparation is sometimes necessary. It also requires a higher level of skill and experience to
achieve a quality result.
10.2.2.5
Materials
This machine incorporates DC TIG function which can be used to weld a variety of materials including
mild steels, stainless steels, copper and chrome moly.
Note: TIG welding is often associated with welding of aluminium, however, aluminium TIG welding
is only possible with AC/DC TIG welding machines. This machine is DC only and is not designed for
TIG welding of aluminium.
10.2.3
The MIG Process
10.2.3.1
Description
The acronym MIG stands for Metal Inert Gas. Metal’ refers to the fact that the filler metal itself (the
MIG wire) is used to conduct the welding current to the job and create the arc. Inert Gas refers to
the fact that the process relies on an inert gas to prevent weld oxidisation. The acronym MAG is also
often used which stands for Metal Active Gas. MAG is fundamentally the same as MIG except that
MAG technically refers to when Carbon Dioxide (CO2) is used as a shielding gas (instead of an inert
gas of argon, helium or a mixed gas with these as a base).
The process is also referred to as Gas Metal Arc Welding (GMAW) when gas is used or Flux-Cored Arc
Welding (FCAW) when flux-cored or gasless/self-shielded wire is used.
10.2.3.2
Process
The MIG welding process involves the filler wire being fed through a torch/gun to the job. The filler
wire carries the welding current to the job. The weld pool is generally covered by an inert gas
supplied from the torch which shields the weld and prevents it from oxidising. However, gasless
welding wire can be used without any shielding gas. This gasless wire has a hollow core filled with
flux which shields the weld and prevents it from oxidising. During welding this flux forms into a slag
covering the weld which is chipped off after the weld has formed.
10.2.3.3
Advantages
MIG welding is both easy and fast. Once weld settings are adjusted, the filler wire is fed automatically
into the weld at the correct rate. It does not rely on the operator to feed in filler wire like TIG welding.
Also because the filler wire is on a roll it lasts significantly longer than a Stick welding electrode so