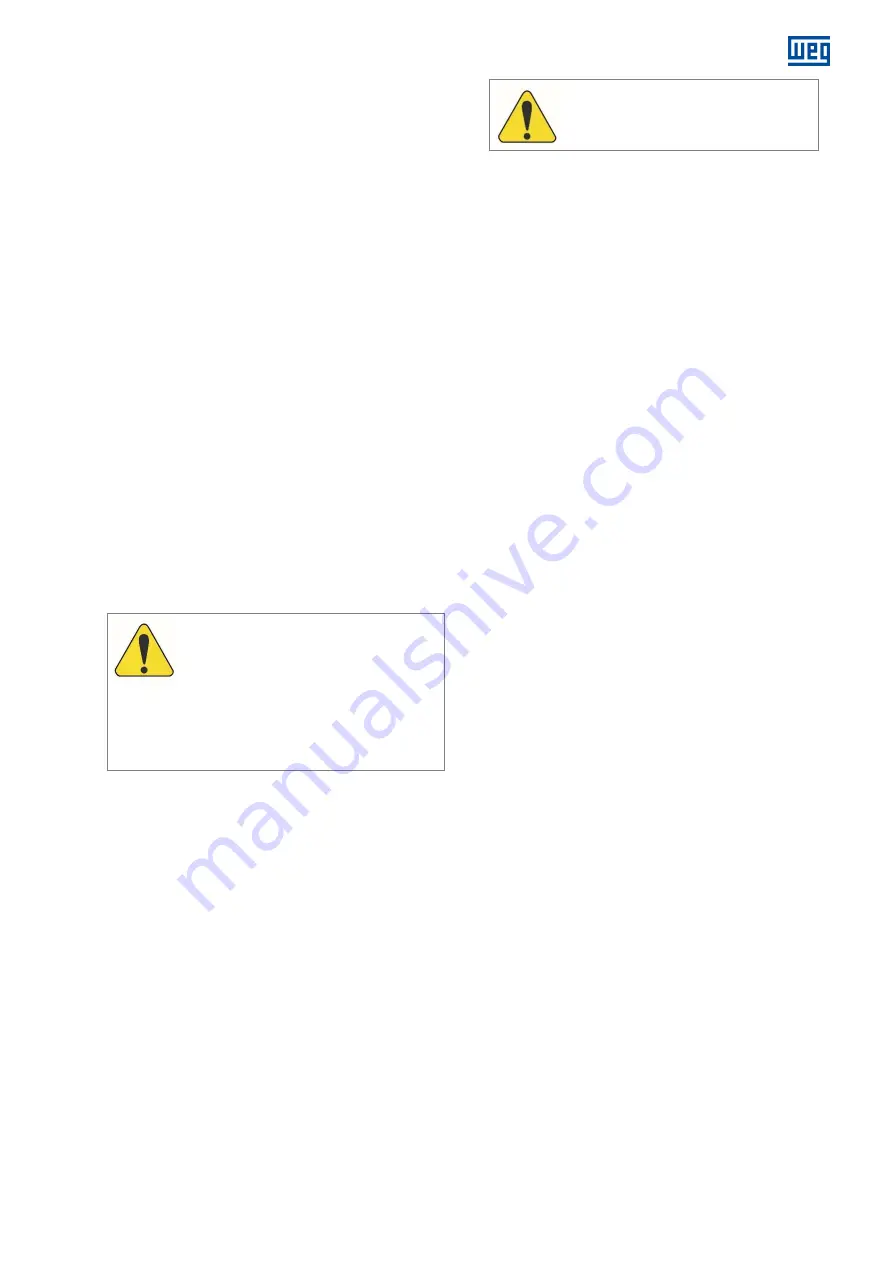
14108242 Installation, operation and maintenance manual – Squirrel cage motor – WGM20 Line l 17
3.3.3.3
Insulation resistance
During the storage period, the insulation resistance of the
motor windings must be measured and recorded every
two months, and before the motor installation or eventually
if there is any change in the preservation process (E.g.
prolonged lack of power).
The measurement procedures and the criteria for
acceptance of the results shall be according to IEEE-43
Standard.
Any insulation resistance reduction must be investigated.
3.3.3.4
Exposed machined surfaces
All exposed machined surfaces (e.g., shaft end and
flanges) are protected at the factory with a temporary
protective agent (rust inhibitor).
This protection coating must be reapplied at least every
six months or when removed and/or damaged.
Recommended Product: Protective agent Anticorit BW
Supplier: Fuchs
3.3.3.5
Sealing
The rubber seals, gaskets, plugs and cable glands of the
motor shall be inspected annually and replaced, if
necessary.
3.3.3.6
Bearings
The rolling bearings are lubricated at the factory for
motor testing.
ATTENTION
In order to keep the bearings in good
condition during the storage period, the
shaft locking device must be removed
every two months, and the motor rotor
must be rotated at least 10 complete turns
at 30 rpm to circulate the grease and
preserve the internal parts of the bearings.
Before putting the motor into operation, the rolling
bearings must be lubricated;
If the motor remains stored for a period exceeding two
years, the rolling bearings must be disassembled,
washed, inspected and relubricated.
3.3.3.7
Terminal boxes
When the insulation resistance of the motor windings is
measured, the main terminal box and the other terminal
boxes must also be inspected, observing the following
aspects:
The inside must be dry, clean and free of any dust
accumulation;
The contact elements cannot present corrosion;
The seals must be in proper condition;
The cable inlets must be correctly sealed.
ATTENTION
If any of these items are not accordingly,
clean or replace the damaged parts.
3.3.3.8
Cleanliness and conservation of the
motor during storage
The motor should be free of oil, water, dust and dirt.
The motor outside must be cleaned with compressed
air at reduced pressure;
Remove the removable rust signs with a clean cloth
soaked in petroleum solvent.
Check if the bearings and lubrication nipples are free of
dust and dirt and if the bearing plugs are properly
tightened.
Risks, marks or rust on the shaft-end should be
removed carefully.
3.3.3.9
Inspections and records during storage
The stored motor must be inspected periodically and
inspection records must be filed.
The following items must be inspected:
1.
Check the motor for physical damages and repair it, if
necessary;
2.
Inspection of the cleanliness conditions;
3.
Check for signs of water condensation inside the
motor;
4.
Check of the protective coating conditions of the
exposed machined parts;
5.
Check the paint conditions, and repair if necessary;
6.
Check for aggressive agents signs;
7.
Check the operation of the space heaters.
8.
Measure and record the temperature, insulation
resistance and polarization index of the stator winding;
9.
Make sure that the storage location complies with the
criteria described in section 3.3.2.1.
3.3.3.10
Predictive/preventive maintenance
WEG recommends that, every 3 years of storage, the
stored motor be sent to a WEG Authorized Repair Shop or
to WEG own factory, in order to perform a complete
predictive maintenance.
The complete predictive maintenance procedure
comprises disassembling the complete motor for
inspection and, after assembly, performing a routine test in
the laboratory.