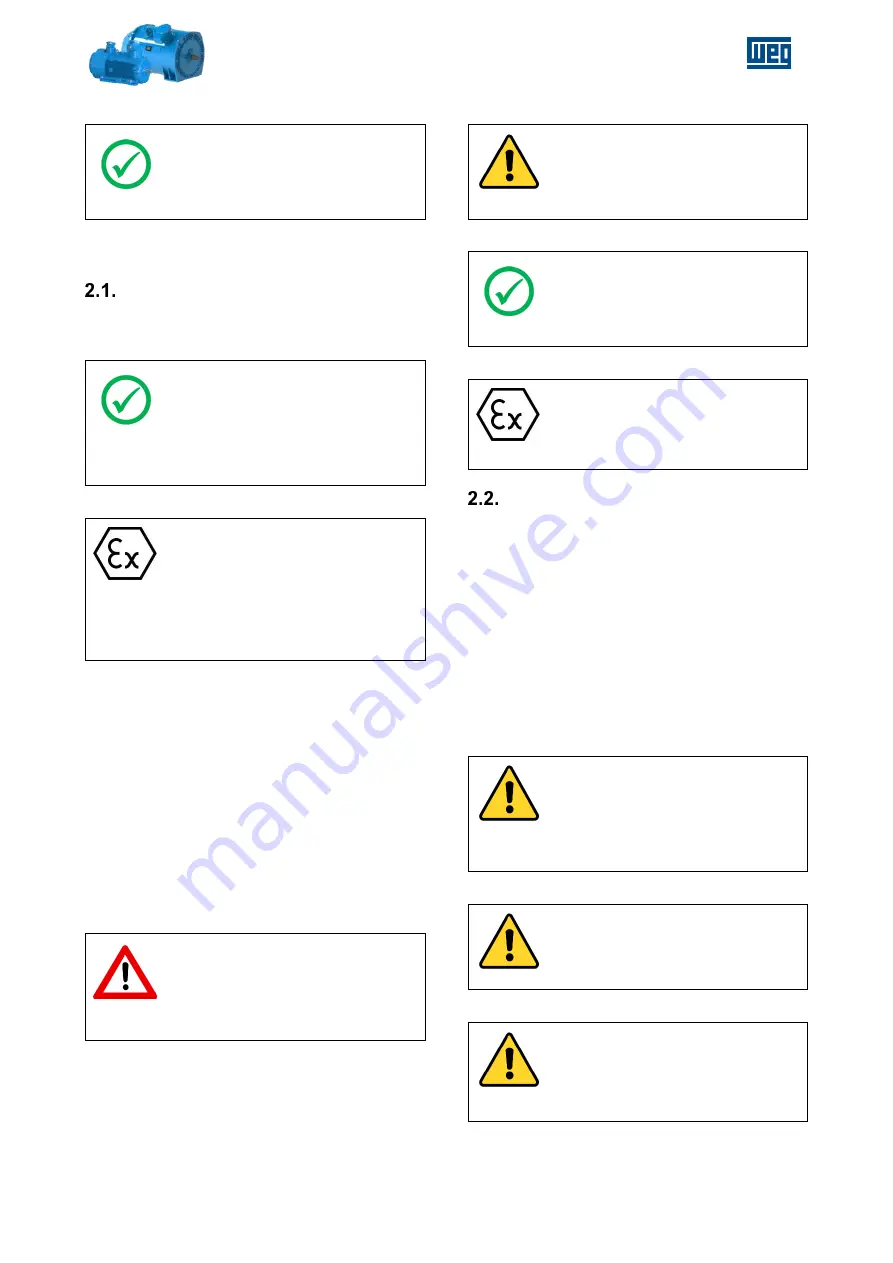
Flameproof motors | 11
www.weg.net
NOTE
WEG states that all information
included in this Manual make part of
the contract and motor warranty.
2.
GENERAL INSTRUCTIONS
MOTOR APPLICATION
Based on the above mentioned Standards, WEG
motors are intended for industrial applications.
NOTE
It is not allowed to use standard
design
motor
in
explosive
atmospheres if they have not been
specifically
certified
for
such
purpose.
EX ATMOSPHERE INFORMATION
This symbol indicates that the
present
paragraph
contains
important
information
about
explosive atmospheres, which must
be strictly followed to avoid damages
and risks.
If a customer makes special requirements, he will
be then responsible to provide safety measures.
The ambient parameters for WEG standard motors
are the following:
- Temperature: -20ºC
≤ T ≤ +40ºC;
- Altitude:
≤ 1000 masl;
In environments containing water and dust, motor
installation will only be allowed if such motor is
specifically designed for such purpose with
instructions on its nameplate.
2.1.1. SAFETY WARNINGS IN THE MANUAL
During installation, operation and maintenance, the
following symbols must be considered:
DANGER
Failure to observe the procedures
recommended in this warning may
result in death, serious injuries and
extensive equipment damage.
ATTENTION
Failure to observe the procedures
recommended in this warning may
result in equipment damage.
NOTE
This provides important information
for correct understanding and proper
operation of the product.
EX ATMOSPHERE INFORMATION
This provides important information
for correct understanding and proper
operation of the Ex Certified product.
TRANSPORTATION
WEG motors equipped with cylindrical-roller,
angular contact or sleeve bearings are supplied with
a shaft locking device on DE side (in some cases,
shaft locking device on NDE side can also be
applied, for example in sea transportation).
Corrosion resistant protection is applied on all
machined surfaces as well.
A visible warning is placed on the motor whenever
this is equipped with a shaft locking device on the
NDF side.
Prior to shipment, motors are factory
–tested and
dynamically balanced.
ATTENTION
Shaft locking device must be
removed before putting the motor
into operation.
ATTENTION
Whenever motor is transported,
reuse shaft locking device.
ATTENTION
To avoid accidents and damages to
the motor, it should be always lifted
with proper cables and devices.