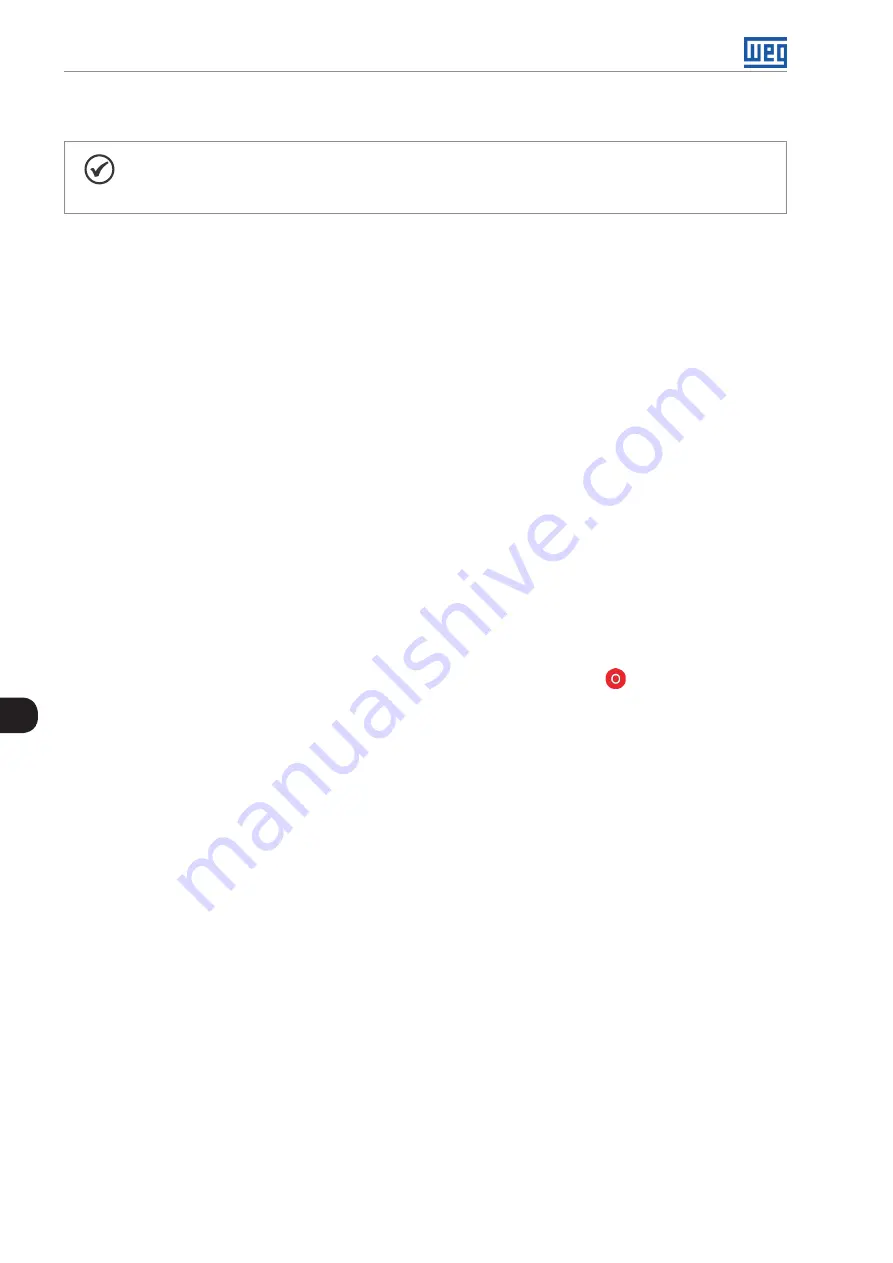
VVW Vector Control
10-8 | CFW501
10
10.2 START-UP IN VVW MODE
NOTE!
Read chapter 3 - Installation and Connection of the user’s manual before installing, powering up or
operating the inverter.
Sequence for installation, verification, power up and start-up.
1. Install the inverter according to chapter 3 - Installation and Connection of the user’s manual, making all the
power and control connections.
2. Prepare and power up the inverter according to section 3.2 - Electric Installation of the user’s manual.
3. Load the correct factory default in P0204 based on the motor rated frequency (set P0204 = 5 for 1800 rpm
(60 Hz) or P0204 = 6 to 1500 rpm (50 Hz).
4. Parameter and function setting specific for the application: program the digital and analog inputs and outputs,
HMI keys, etc., according to the application requirements;
5. Activation of the VVW control: using the HMI “STARTUP” menu, the browsing is limited to the relevant parameters
to set the control mode. Set P0202 = 3; then the “STARTUP” menu will browse the relevant parameters to set
the V VW;
6. Parameterization of the V VW control: browsing the “STARTUP” menu, set parameters P0398, P0399, P0400,
P0401, P0402, P0403, P0404 and P0407 according to the data on the motor nameplate. If some of those data
are not available, insert the approximate value by calculation or similarity to WEG standard motor – see
10.1: Characteristics of IV pole WEG standard motors on page 10-3
.
7. Self-Tuning of the V VW control: The self-tuning is activated by setting P0408 = 1. In this process, the inverter
applies DC to the motor to measure the stator resistance, while the HMI bar graph shows the progress of the
self-tuning. The self-tuning process can be interrupted at any time by pressing the
key.
8. End of the Self-Tuning: at end of the self-tuning, the HMI returns to the browsing menu, the bar displays the
parameter programmed by P0207 again and the stator resistance measured is stored in P0409. On the other
hand, if the self-tuning fails, the inverter will indicate a fault. The most common fault in this case is F0033, which
indicates error in the estimated stator resistance. Refer to
chapter 14 - Faults and Alarms
.
For applications:
That can use the factory default programming of the analog and digital inputs and outputs, use the HMI
“BASIC” menu.
That require just the analog and digital inputs and outputs with programming different from the factory default,
use the HMI “I/O” menu.
That require functions such as flying start, ride-through, DC braking, rheostatic braking, etc., access and modify
the parameter of those functions in the HMI “PARAM” menu. For further information on the HMI menus, refer
to
chapter 5 - Basic Instructions for Programming and Settings.
Summary of Contents for CFW501 V1.8X
Page 2: ......
Page 8: ...Summary...
Page 34: ...General Information 2 4 CFW501 2...
Page 38: ...About the CFW501 3 4 CFW501 3...
Page 42: ...HMI and Basic Programming 4 4 CFW501 4...
Page 58: ...Identification of the Inverter Model and Accessories 6 4 CFW501 6...
Page 72: ...Logical Command and Speed Reference 7 14 CFW501 7...
Page 76: ...Available Motor Control Types 8 4 CFW501 8...
Page 108: ...Functions Common to all the Control Modes 11 14 CFW501 11...
Page 134: ...Digital and Analog Inputs and Outputs 12 26 CFW501 12...
Page 148: ...Faults and Alarms 14 12 CFW501 14...