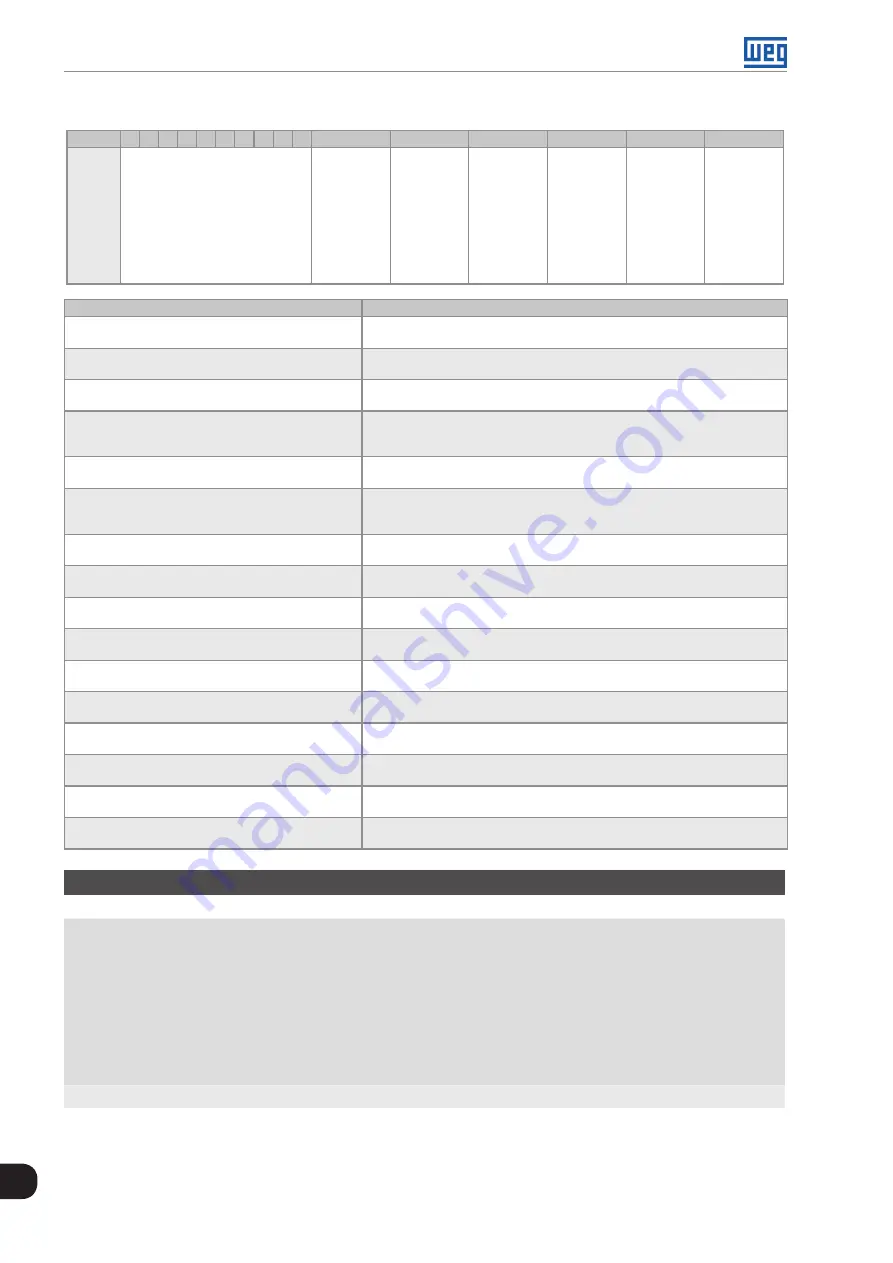
SoftPLC
18-10 | CFW300
18
Table 18.5:
Description of the logical status of the PID controller application
Bits
15 14 13 12 11 10 9 8 7 6
5
4
3
2
1
0
Function
Reserved
Process
Variable High
Level (F763)
Process
Variable High
Level (A762)
Process
Variable Low
Level (F761)
Process
Variable Low
Level (A760)
PID controller
in Manual or
Automatic
Sleep Mode
Active (A750)
Bits
Values
Bit 0
Sleep Mode Active (A750)
0:
Inverter is not in the alarm condition
1:
It indicates that the PID controller is in the sleep mode (A750)
Bit 1
PID Controller in Manual or Automatic
0:
PID controller operating in Manual mode
1:
PID controller operating in Automatic mode
Bit 2
Control Process Variable Low Level (A760)
0:
Inverter is not in the alarm condition
1:
It indicates that the control process variable (P916) is in low level (A760)
Bit 3
Fault for Control Process Variable Low Level (F761)
0:
Inverter is not in the fault condition
1:
It indicates that the inverter switched the motor off due to the control process
variable low level (F761)
Bit 4
Control Process Variable High Level (A762)
0:
Inverter is not in the alarm condition
1:
It indicates that the control process variable (P916) is in high level (A762)
Bit 5
Fault for Control Process Variable High Level (F763)
0:
Inverter is not in the fault condition
1:
It indicates that the inverter switched the motor off due to the control process
variable high level (F763)
Bit 6
Reserved
Reserved
Bit 7
Reserved
Reserved
Bit 8
Reserved
Reserved
Bit 9
Reserved
Reserved
Bit 10
Reserved
Reserved
Bit 11
Reserved
Reserved
Bit 12
Reserved
Reserved
Bit 13
Reserved
Reserved
Bit 14
Reserved
Reserved
Bit 15
Reserved
Reserved
P920 – Selection of the Control Setpoint Source
Adjustable
Range:
0 = Control Setpoint via HMI or Communication Networks (P911)
1 = Control Setpoint via Analog Input AI1
2 = Control Setpoint via Analog Input AI2
3 = Control Setpoint via Electronic Potentiometer (DI3 and DI4)
4 = Two Setpoints via Digital Input DI3 (P912 and P913)
5 = Three Setpoints via Digital Inputs DI3 and DI4 (P912, P913 and
P914)
6 = Four Setpoints via Digital Inputs DI3 and DI4 (P912, P913, P914
and P915)
Factory
Setting:
0
Properties:
Description:
This parameter defines the control setpoint source in automatic mode of the PID controller.
Summary of Contents for CFW300 V1.3X
Page 2: ......
Page 8: ...Contents...
Page 46: ...Identification of the Inverter Model and Accessories 6 4 CFW300 6...
Page 60: ...Logical Command and Speed Reference 7 14 CFW300 7...
Page 72: ...V f Scalar Control 9 10 CFW300 9...
Page 80: ...VVW Vector Control 10 8 CFW300 10...
Page 116: ...Digital and Analog Inputs and Outputs 12 24 CFW300 12...
Page 132: ...Reading Parameters 15 6 CFW300 15...