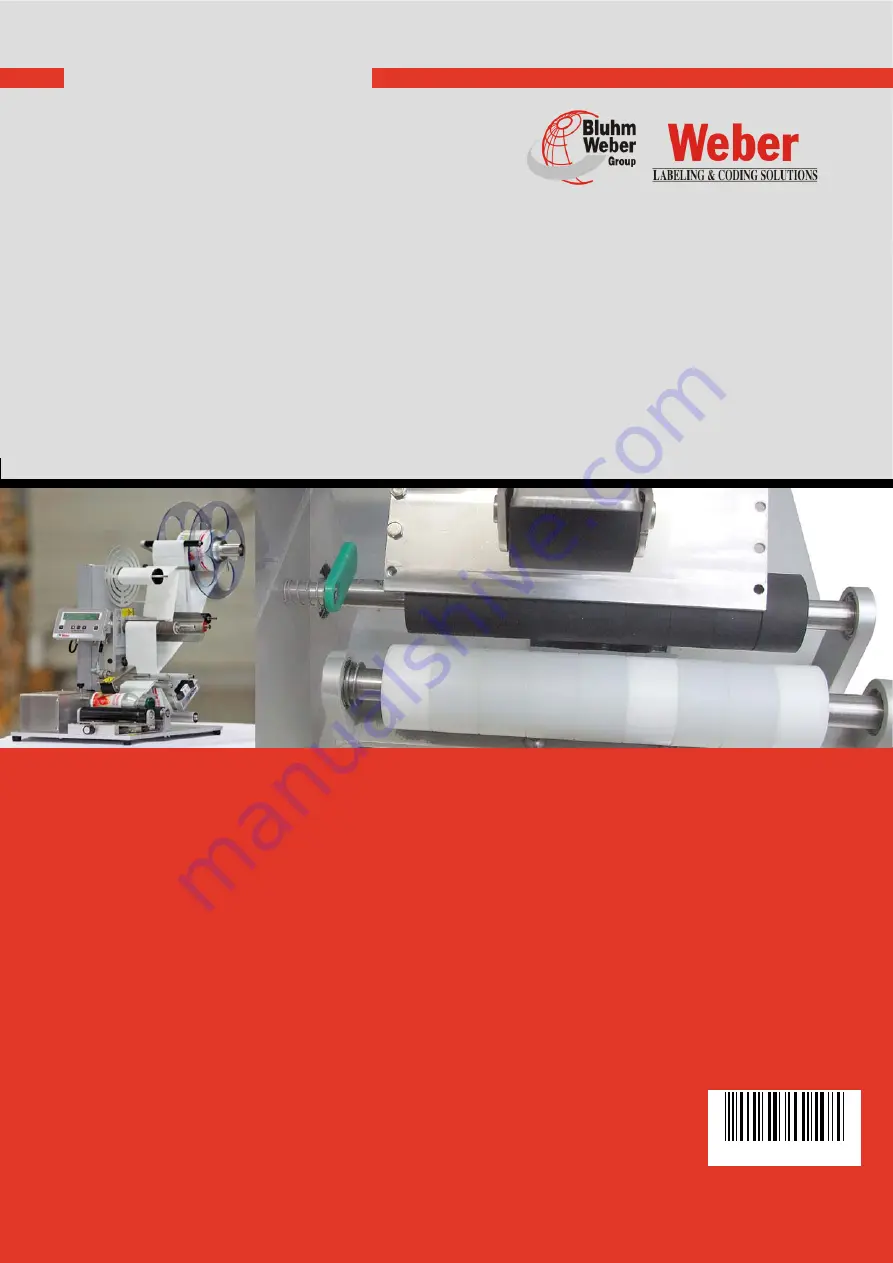
Original User’s Manual
Installation, Setup, Operation and Maintenance
Geset 141
Article number of documentation 40020664
Copyright ©, Weber Marking Systems GmbH
Weber Marking Systems GmbH
Maarweg 33
D-53619 Rheinbreitbach
E-Mail: [email protected]
http://www.webermarking.de
Version: 30.01.15 /ZIM
40020664
Summary of Contents for Geset 141
Page 2: ...Blank page...