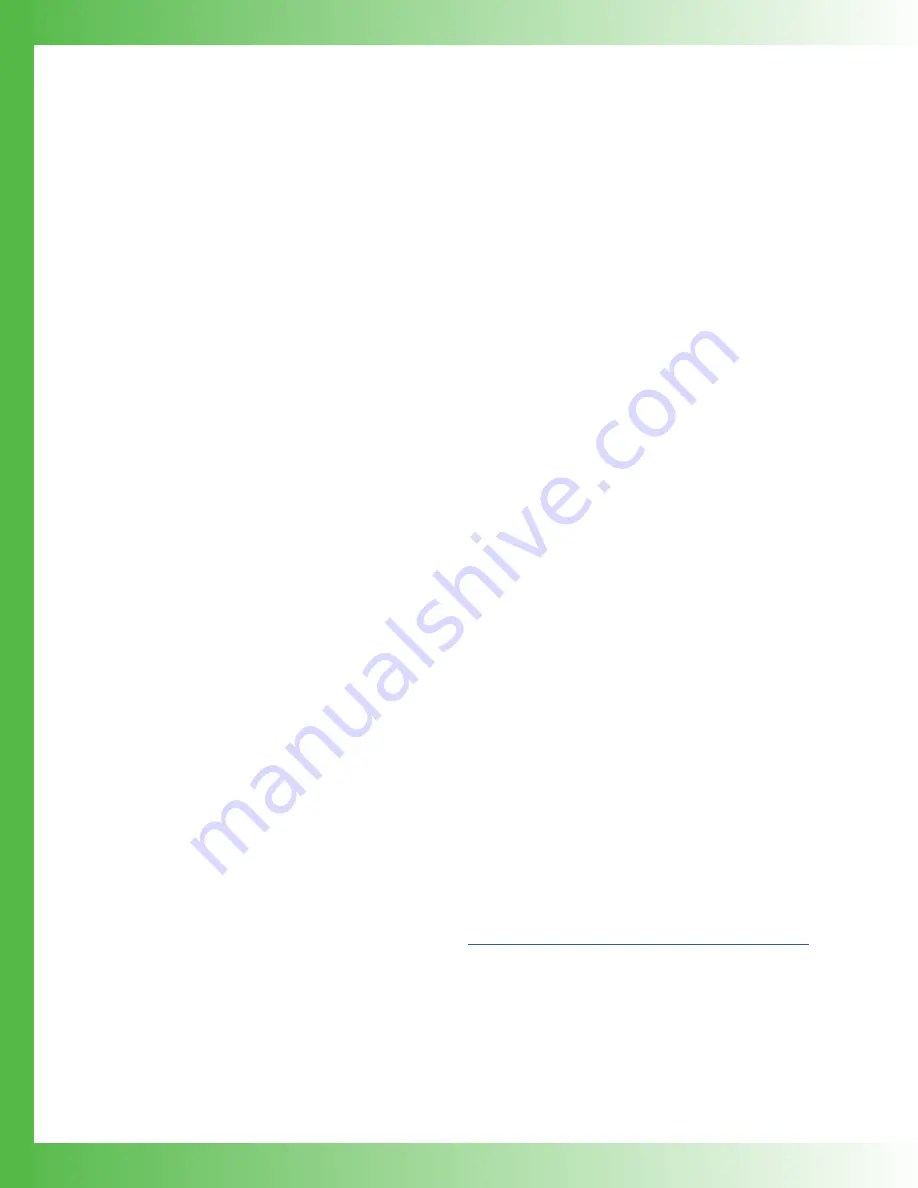
9
THEORY OF OPERATION
The LDTC LAB Series combine a precision temperature
controller and a low-noise laser diode driver in one instrument.
The temperature controller delivers bidirectional current to
Peltier Effect thermoelectric coolers (TEC), or unidirectional
current to resistive heaters (RH)
[1]
. The laser driver operates in
either constant current or constant power mode, maintaining
very stable current to the laser.
The fundamental operating principle of the temperature
controller is that the controller adjusts the output drive current
in order to change the temperature of the sensor that is
connected to the thermal load. The goal is to make the sensor
temperature match the setpoint temperature, and then keep
them equal in spite of changes to ambient conditions and
variations in thermal load.
The laser driver operates on similar principles, attempting to
match the actual laser (or photodiode) current to the user-
defined setpoint, adjusting as required. While output is
enabled, the controller continuously compares the setpoint
laser current and the actual current. If there is a difference
between the setpoint and actual, the controller adjusts the
output current until the difference is zero.
The controller includes features that help protect the load
from damage, and also make it more versatile in a wide array
of applications.
• Current Limits:
The adjustable current limits must be set
correctly in order to avoid over-driving and damaging the
TE/heater and laser.
• Voltage Limit:
The voltage to the TEC can be limited
through remote commands and the voltage to the laser
can be limited on screen.
• Temperature Limits:
Set high and low temperature limits
to protect the laser. If temperature limits are exceeded,
TE current will be disabled. Optionally, LD current can be
configured to disable as well.
• Temperature Control Loop:
The temperature controller
employs a smart Proportional-Integral-Derivative (PID)
control loop to adjust the drive current. The terms are user-
adjustable and, when properly configured, will quickly
settle the load temperature with minimal overshoot and
ringing.
• IntelliTune:
Wavelength’s proprietary algorithm
characterizes the TEC/Sensor system’s response to
the LDTC LAB and determines the optimal PID control
coefficients. Then, it automatically adjusts the PID values
as setpoint, tuning mode, or bias current are changed.
• Disconnect/Failure Protection:
If a short or open circuit
is detected at the temperature sensor, thermoelectric, or
laser, the respective output current is disabled.
[1]
The LDTC LAB does not support packages where the TEC/RH is
connected to the laser case.
INSTRUMENT OVERVIEW
WHAT’S IN THE BOX
• LDTC LAB: Combination Laser Driver and Temperature
Controller Instrument
•
Power Cable, type appropriate for final location
• 15+2 Male D-SUB plug and pins for TC connection
• 15-pin Male D-SUB plug and pins for connection to Type A
laser diodes (passive interlock jumper installed)
• 15-pin Female D-SUB receptacle and pins for connection
to Type C laser diodes (passive interlock jumper installed)
•
50 Ω BNC Terminator for Active Lock BNC
• Two 3.15 A fuses are installed in the red fuse tray in the
power entry module on the back panel
• Keys for the key switch
REQUIRED AND OPTIONAL
EQUIPMENT
FOR SET UP
• Optional test loads with appropriate heatsinking (both
laser and thermoelectric) OR
• Thermoelectric/Resistive Heater with temperature sensor
for feedback, and laser diode
COMPUTER REQUIREMENTS FOR
REMOTE OPERATION ONLY (OPTIONAL)
Operating System: Windows Vista SP2 or later
Note
: See
ESD INFORMATION
Before proceeding, it is critical that you take precautions to
prevent electrostatic discharge (ESD) damage to the laser
diode. ESD damage can result from improper handling of
sensitive electronics, and is easily preventable with simple
precautions.
For more information regarding ESD, see Application Note
AN-LDTC06: Basics: Electrostatic Discharge (ESD)
We recommend that you always observe ESD precautions
when operating the LDTC LAB.