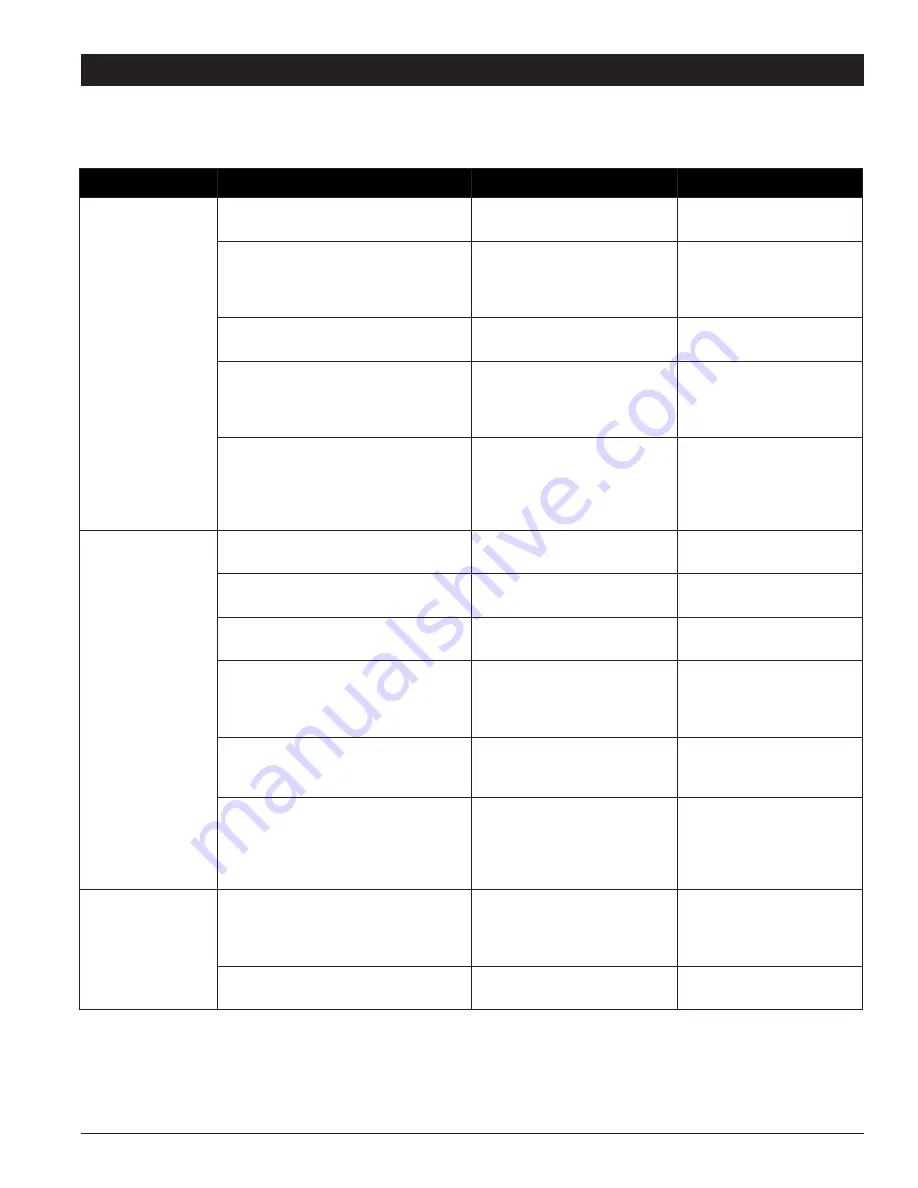
ES-A-ACV-LF960GD-15 2115
Issue
Possible Cause
Corrective Action
Notes
Main Valve will not
open
Closed isolation valves in pilot system.
Check isolation valves, ensure
open.
Insufficient supply pressure.
Check upstream pressure.
Depending on water
source, supply pressure
may not be controlled by
valve operator.
Main valve stem assembly corroded/
damaged
Inspect stem assembly, clean/
replace if necessary.
Blockage in pilot system.
Inspect & clean any installed
pilot system strainers, check
orifice/speed controls for
blockages.
Improperly configured opening speed
control.
Adjust opening speed control
to verify functionality, adjust as
required.
Standard setting for
opening speed control is
1
1/2
- 2
1/2
turns open from
full closed position. Can be
adjusted in field.
Main Valve will not
close
Closed isolation valves in pilot system
Check isolation valves, ensure
open.
Diaphragm is damaged
Conduct diaphragm seal test,
repair and replace if necessary.
Main valve stem assembly corroded/
damaged.
Inspect stem assembly, clean/
replace if necessary.
Blockage in main valve.
Perform freedom of movement
test; if valve does not close,
disassemble and remove
blockage.
Worn/damaged valve seat.
Perform seat sealing check;
disassemble and inspect/re-
pair seat if required.
Improperly configured closing speed
control.
Adjust closing speed control
to verify functionality, adjust as
required.
Standard setting for
closing speed control is
1
1/2
- 2
1/2
turns open from
full closed position. Can
be adjusted in field.
Solenoid will not
actuate
Possible Cause: Low or no voltage
Check voltage at the solenoid
connection, insuring that it has
the minimum of 85% of the
coils rated voltage.
Should be performed by
licensed electrician
Manual operated is engaged
Turn manual operator counter-
clockwise to disengage
23
Troubleshooting Guide
© 2021 Watts