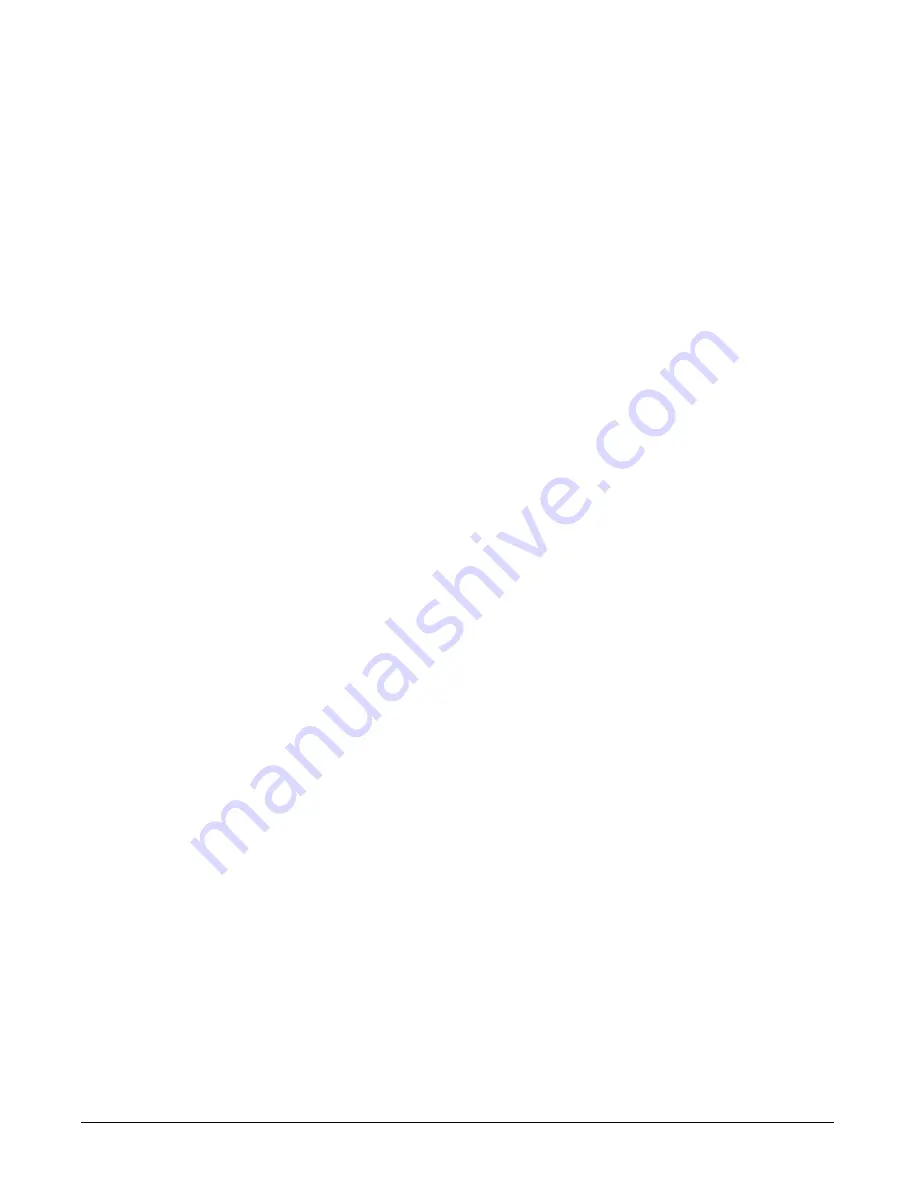
3 . 2
■
O p e r a t i o n s P a g e
Wa t l o w S e r i e s F 4 P
Autotune PID
In autotuning, the controller automatically selects the
PID parameters for optimal control, based on the ther-
mal response of the system. In the Series F4P, five sets of
PID values are available. Default PID values exist for all
PID sets, although these values typically do not provide
optimal control. PID values can be auto-tuned or adjust-
ed manually. When autotuning is complete, the PID val-
ues will be stored in the Edit PID Menu.
Set point changes for remote, ratio and differential con-
trol are ignored until autotuning is complete.
Autotuning Procedure
Autotuning is initiated from the Operation Menu.
1. Before initiating auto-tune, go to the System Menu
(Setup Page), and establish the Autotune Set Point
to a percentage of set point. This percentage is based
on your knowledge of the system and how much
overshoot or undershoot there is likely to be in on-off
control.
Select to display Tune Status in the Custom Main
Page Menu.
2. Go to the Main Page and adjust set point.
3. Go to the Autotune PID Menu (Operations Page) and
choose the PID set in which to store the values. You
must exit back to Main Page with the left arrow. A
message will be displayed on the Main Page during
the autotuning process.
4. When autotuning is complete, the controller will
store the values for optimum control in the specified
PID set.
For additional information about autotuning and propor-
tional, integral and derivative control, see the Features
Chapter.
✔
Note: While the controller is autotuning, only the Op-
eration Page of the software can be entered.
ç
CAUTION: Choose an autotune set point value that will
protect your product from possible damage from overshoot
or undershoot during the autotuning oscillations. If the
product is sensitive, select the autotune set point very
carefully to prevent product damage.
Edit PID
The Edit PID Menu is useful when Auto-tune PID does
not provide adequate control. Each of the PID parame-
ters can be adjusted manually:
Proportional Band: Define a band for PID control, en-
tered in degrees or units. Lower values increase gain,
which reduces droop but can cause oscillation. Increase
the proportional band to eliminate oscillation.
Integral (Reset): Define the integral time in minutes
per repeat; define reset in repeats per minute. Set re-
peats per minute if units are U.S.; minutes per repeat if
units are SI.
Derivative (Rate): Define the derivative (rate) time in
minutes. Large values prevent overshoot but can cause
sluggishness. Decrease if necessary.
Dead Band: Define the dead band in degrees or units.
Heating dead band shifts the set point down. Cooling
dead band shifts the set point up. For more information,
see the Features Chapter.
For background information, see Chapter 7, Features.
Manual Tuning Procedure
1. Apply power to the Series F4P and establish a set
point on the Main Page.
2. Establish Cycle Time in the Control Output Menu
(Setup Page), as required. Typical cycle times are 1.0
second for an SSR and 5.0 seconds for a mechanical
relay. Faster cycle times sometimes achieve the best
system control. However, if a mechanical contactor or
solenoid is switching power to the load, a longer cy-
cle time may be desirable to minimize wear on the
mechanical components. Experiment until the cycle
time is consistent with the desired quality of control.
3. Go to the Edit PID Menu (Operations Page), and
choose the channel and PID set. Establish values for
the PID parameters: Proportional Band, 5; Integral
(Reset), 0; Derivative (Rate), 0; and Autotune, Tune
Off. Tuning begins when you choose a PID set.
4. When the system stabilizes, watch the value of Input
1 on the Main Page. If this value fluctuates, increase
the proportional band setting until it stabilizes. Ad-
just the proportional band in 3° to 5° increments, al-
lowing time for the system to stabilize between ad-
justments.
5. When Input 1 has stabilized, watch the percent pow-
er on the Main Page. It should be stable, ±2%. At
this point, the process temperature should also be
stable, but it will exhibit droop (stabilized below set
point). The droop can be eliminated with integral (re-
set).
Summary of Contents for F4P Series
Page 4: ...ii Table of Contents Watlow Series F4P Notes...
Page 14: ...2 8 Operating from the Front Panel Watlow Series F4P Notes...
Page 58: ...6 32 Parameters Watlow Series F4P Notes...
Page 77: ...Watlow Series F4P Features 7 19 Notes...
Page 78: ...7 20 Features Watlow Series F4P Notes...
Page 94: ...8 16 Installation and Wiring Watlow Series F4P Notes...