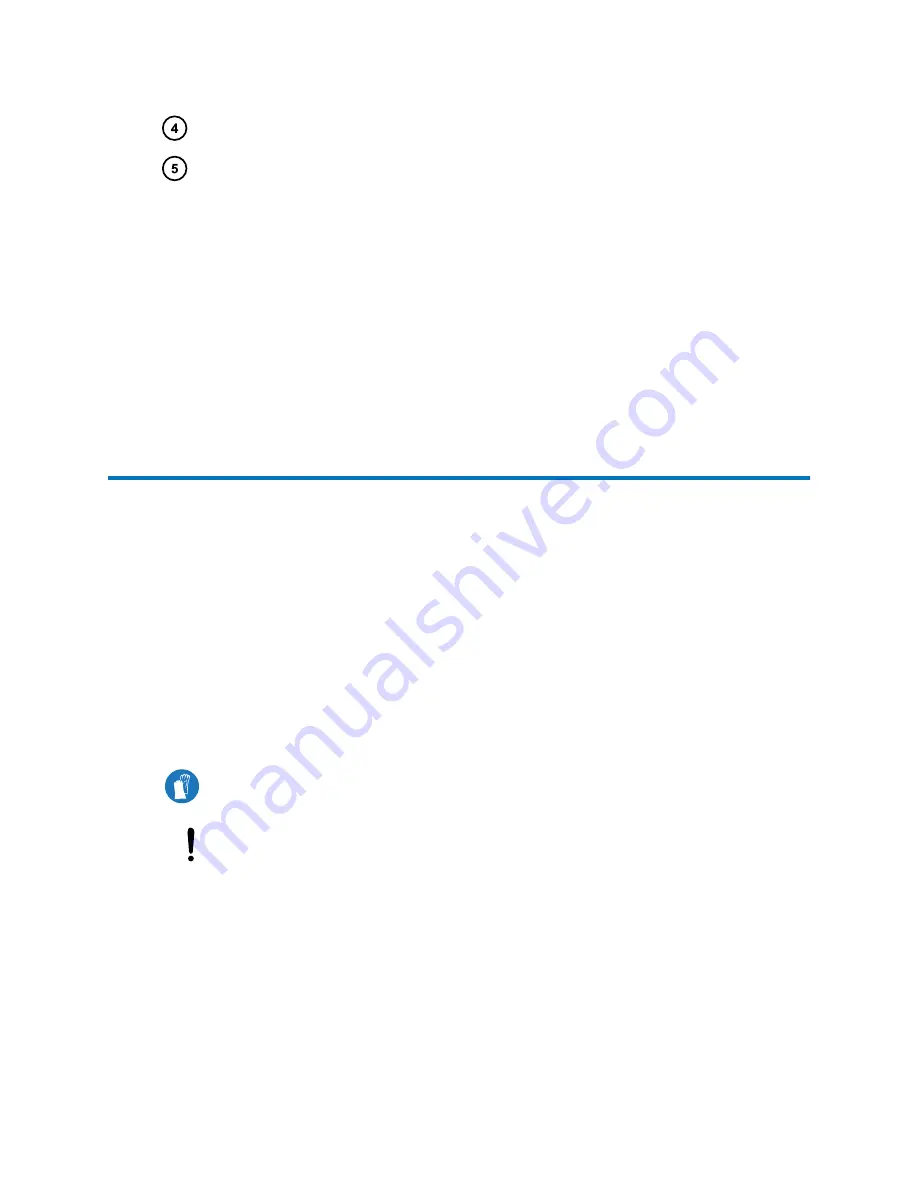
Pump switching box
Power cable
To make the electrical connections to the rotary backing pump:
1.
Connect the pump control cable from the pump switching box to the backing pump
connector on the instrument’s rear panel.
2.
Connect the rotary backing pump power cord to the pump switching box.
3.
Connect the pump switching box power cord to the main power source and use the power
switch on the pump to power it on.
Tip:
The relay box allows the instrument to remotely control the backing pump.
D.4 Connecting to the nitrogen gas supply
Required materials
• Chemical-resistant, powder-free gloves
• Utility knife
• Wrench
• 6-mm PTFE tubing (included in the installation kit)
• 6-mm stud
• Nitrogen regulator
To connect the nitrogen gas supply:
Requirement:
Wear clean, chemical-resistant, powder-free gloves when performing
this procedure.
Notice:
To avoid gas leaks, use the sharp knife to cut the PTFE tubing squarely.
1.
Use the sharp knife to cut a length of 6-mm PTFE tubing long enough to connect the rear
of the instrument to the nitrogen regulator.
2.
Connect one end of the 6-mm PTFE tubing to the nitrogen inlet port on the rear of the
instrument (see
Connecting the Standard instrument's backing pump
3.
Attach the nitrogen regulator to the nitrogen supply.
4.
Install the 6-mm stud into the regulator outlet.
June 15, 2017, 715003956 Rev. F
Page 90