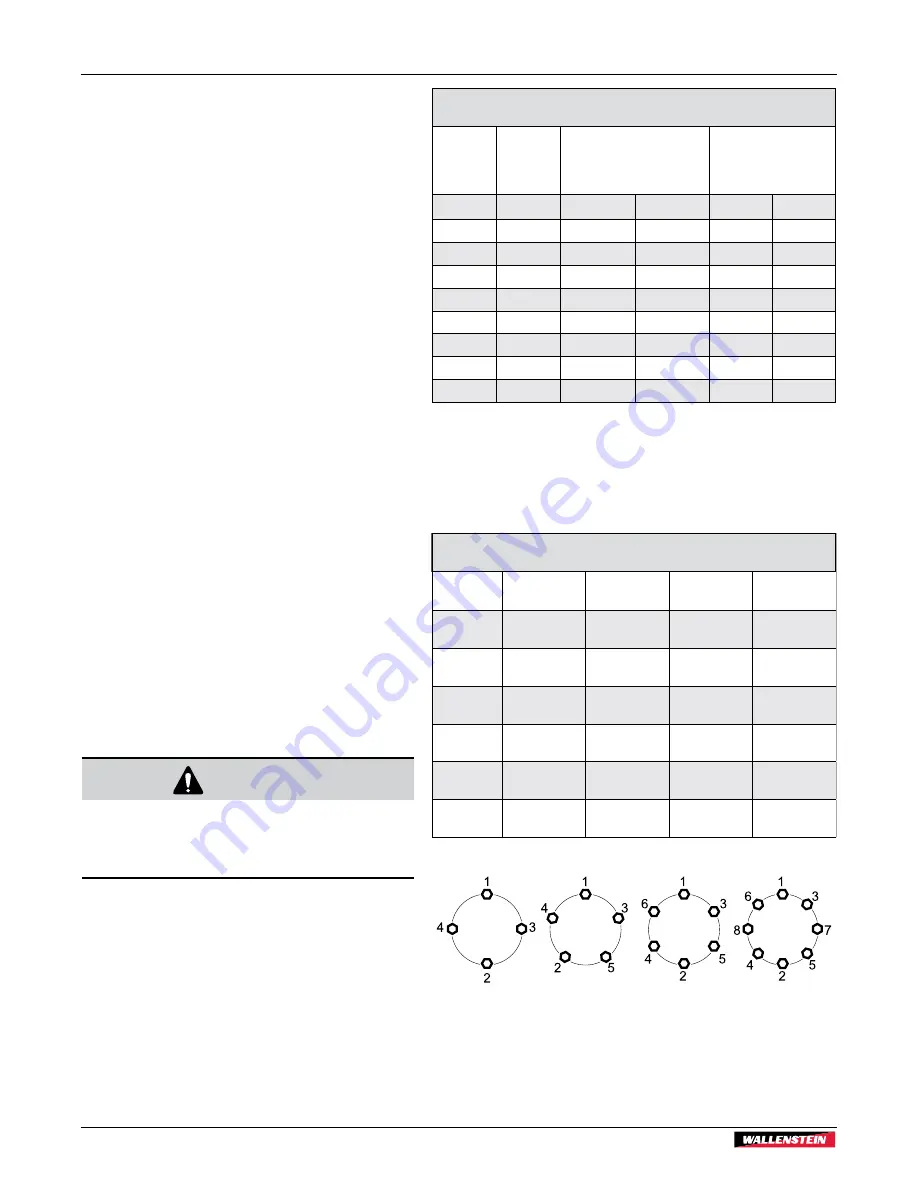
Specifications
WXR720/L, WXR740/L
Trailer Wood Splitter
40
9.3 Hydraulic Fitting Torque
Tightening Flare Type Tube Fittings
1.
Check flare and flare seat for defects that might
cause leakage.
2.
Align tube with fitting before tightening.
3.
Hand-tighten swivel nut until snug.
4.
To prevent twisting the tube, use two wrenches.
Place one wrench on the connector body and tighten
the swivel nut with the second. Torque to values
shown.
If a torque wrench is not available, use the FFFT (Flats
From Finger Tight) method.
Hydraulic Fitting Torque
Tube
Size
OD
Hex
Size
Across
Flats
Torque value
Flats From
Finger Tight
Inches Inches
lbf•ft
N•m
Flats
Turns
3/16
7/16
6
8
2
1/6
1/4
9/16
11–12
15–17
2
1/6
5/16
5/8
14–16
19–22
2
1/6
3/8
11/16
20–22
27–30
1-1/4
1/6
1/2
7/8
44–48
59–65
1
1/6
5/8
1
50–58
68–79
1
1/6
3/4
1-1/4
79–88
107–119
1
1/8
1
1-5/8
117–125 158–170
1
1/8
Values shown are for non-lubricated connections.
9.4 Wheel Lug Torque
It is extremely important safety procedure to apply
and maintain proper wheel mounting torque on your
trailer axle. Torque wrenches are the best method to
assure the proper amount of torque is being applied to
a fastener.
Wheel lugs should be torqued before first road use and
after each wheel removal. Check and re torque after the
first 10 miles (16 km), 25 miles (40 km), and again at
50 miles (80 km). Check periodically thereafter.
WARNING!
Wheel lug nuts must be installed and
kept at the proper torque value to prevent
loose wheels, broken studs, or possible
separation of wheels from axle.
•
Start all lug nuts onto the threads by hand.
•
Tighten lug nuts in stages, following the pattern
shown in the Wheel Lug Nut Torque table.
Wheel Lug Nut Torque
Wheel
Size
Units
1st Stage 2nd Stage 3rd Stage
8"
lbf•ft
N•m
12–20
16–26
30–35
39–45.5
45–55
58.5–71.5
12"
lbf•ft
N•m
20–25
26–32.5
35–40
45.5–52
50–60
65–78
13"
lbf•ft
N•m
20–25
26–32.5
35–40
45.5–52
50–60
65–78
14"
lbf•ft
N•m
20–25
26–32.5
50–60
65–78
90–120
117–156
15"
lbf•ft
N•m
20–25
26–32.5
50–60
65–78
90–120
117–156
16"
lbf•ft
N•m
20–25
26–32.5
50–60
65–78
90–120
117–156
4-Bolt
Wheel Lug Torque Pattern
5-Bolt
6-Bolt
8-Bolt
Summary of Contents for WXR720
Page 44: ...www wallensteinequipment com...