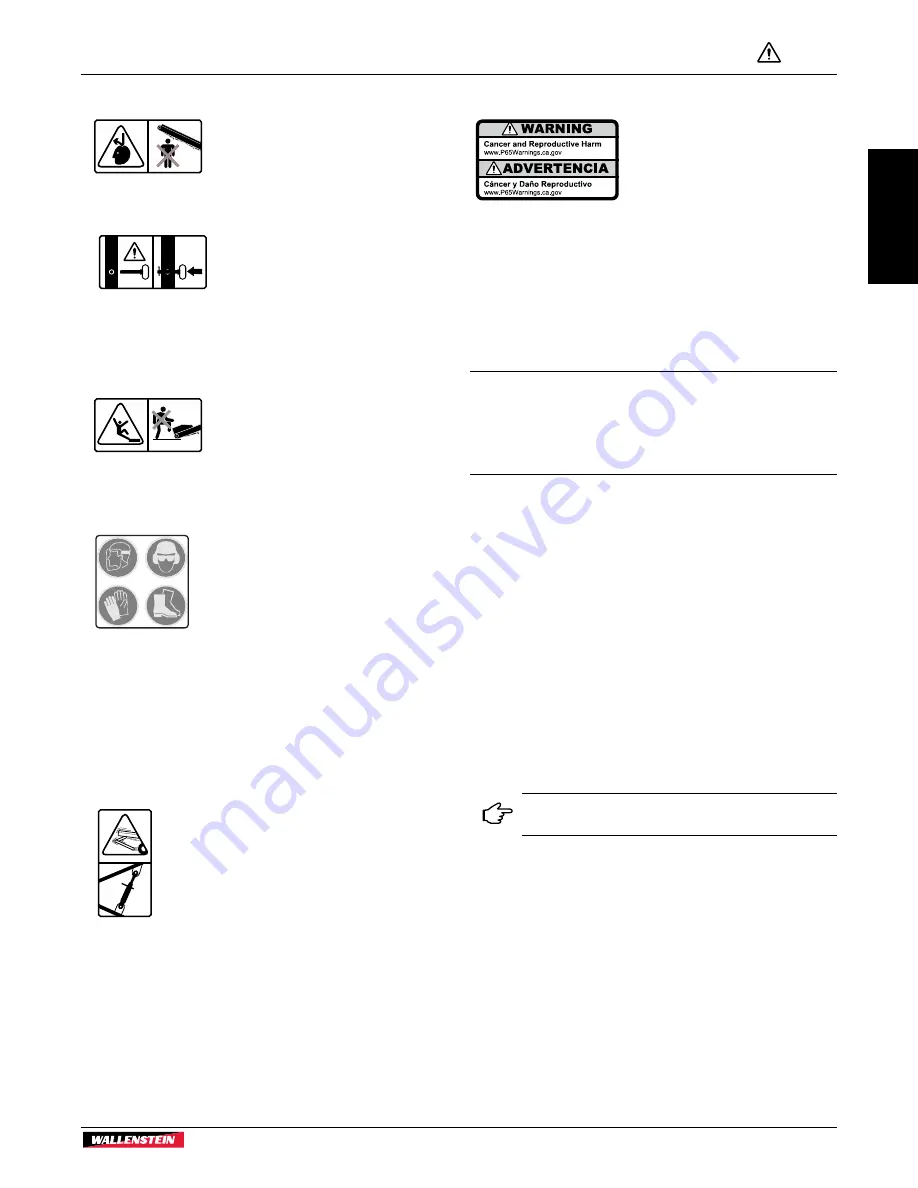
5. Warning!
Risk of being injured from falling
objects.
Do not walk under the conveyor.
6. Warning!
Risk of machine moving
unexpectedly when support pin is
removed. Personal injury could
result.
Keep pin installed and secured with
pin keeper.
7. Warning!
Risk of being injured from falling off
conveyor.
Do not climb on the conveyor.
8. Safety Notice
Always wear appropriate Personal
Protective Equipment when using this
machine.
For example:
• A hard hat
• Heavy gloves
• Hearing protection
• Protective shoes with slip
resistant soles
• Protective glasses, goggles, or
face shield
9. Caution!
Risk of conveyor frame moving or bouncing
unexpectedly during operation or when
transporting. Personal injury could result.
Install toplink to lock top and bottom folding
frames together.
10. Warning!
Risk of cancer or
reproductive harm.
The machine materials contain chemicals or machine
operation may produce gases or dust that are identified by the
state of California as causes of cancer, birth defects, or other
reproductive harm.
This warning is required by the state of California, USA to
comply with Proposition 65: the Safe Drinking Water and Toxic
Enforcement Act of 1986.
IMPORTANT! If parts are replaced that have safety signs on
them, new signs must be applied. Safety signs must always
be replaced if they become damaged, are removed, or
become illegible.
Safety signs are included in the product decal kit available from
your authorized dealer. Decals are not available separately.
2.9 Replacing Damaged Safety Signs
Replace any safety sign that is damaged or missing. If a safety
sign is attached to a part that is replaced, install a safety sign
on the replacement part. Replacement safety signs are available
from your authorized distributor, dealer parts department, or
Wallenstein Equipment.
Procedure
Installation area must be clean and dry. Make sure the surface is
free of grease or oil. Ambient temperature must be above 50 °F
(10 °C).
Determine exact position before removing the
backing paper on the decal.
1.
Peel the decal off the backing sheet.
2.
Align the decal with an edge on the machine if possible.
3.
Starting on one edge, carefully press the center of the
exposed sticky backing in place, smoothing it out as you
work from one side to the other.
4.
Use a squeegee, credit card or similar to smooth it out.
Work from one end of the decal to the other end.
Small air pockets can be pierced with a pin and smoothed out
using the piece of sign backing paper.
CT24
Trailer Firewood Conveyor
Safety
Safety
13