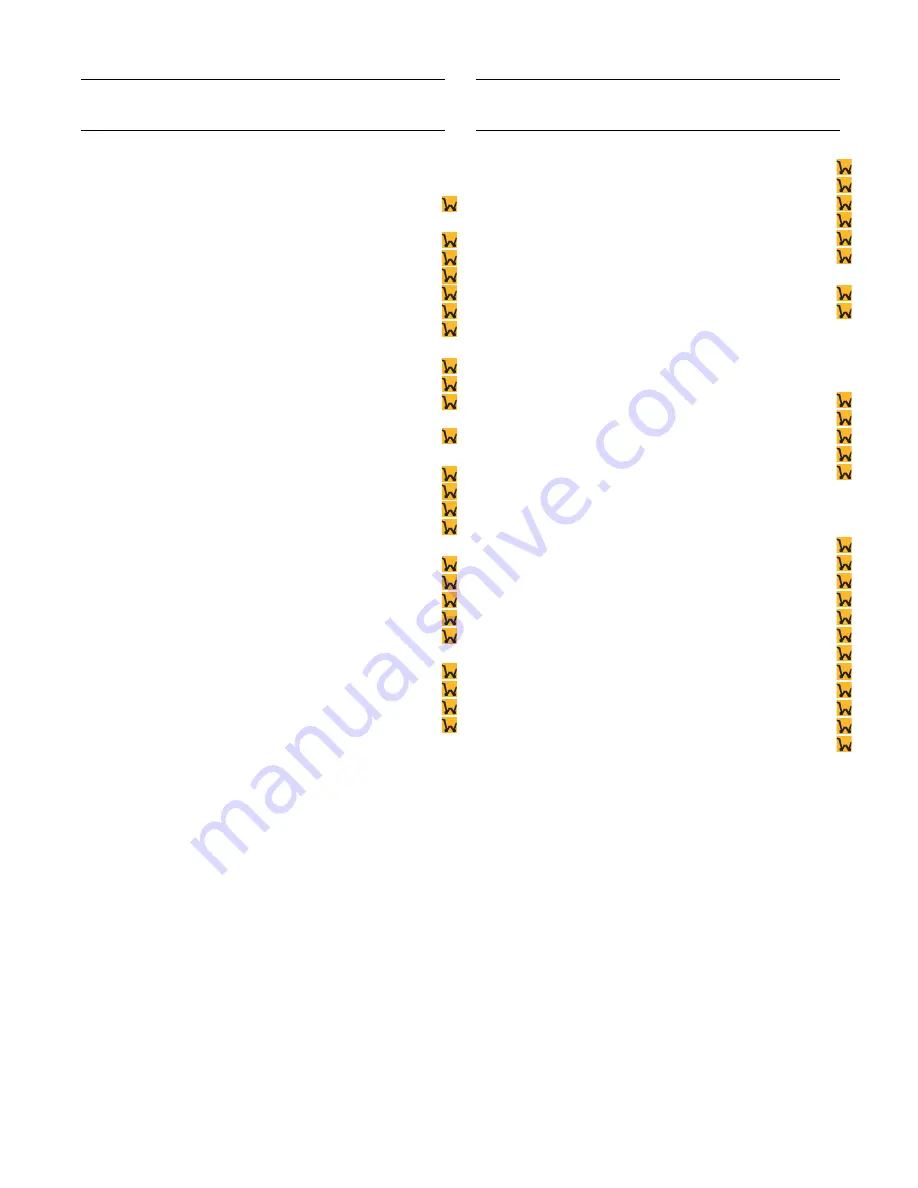
itEm part
dEscriptiOn
nO.
nO.
nO.
rEq’d
itEm part
dEscriptiOn
nO.
nO.
nO.
rEq’d
Use only genuine
Walker
®
replacement parts.
Effective Date 09-15-10
82
ELEctricaL assEmBLY (mOdEL mBs26)
Electrical assembly
8960-15 Ignition Switch W/Keys
(Includes Items # 2, 3 & F349)
8996-10 Amber Indicator Light Assembly
Time Delay Module (Less Harness)
Battery Terminal Insl., Red (+)
Battery Terminal Insl., Blk (-)
Fasteners
*
Service Part Only