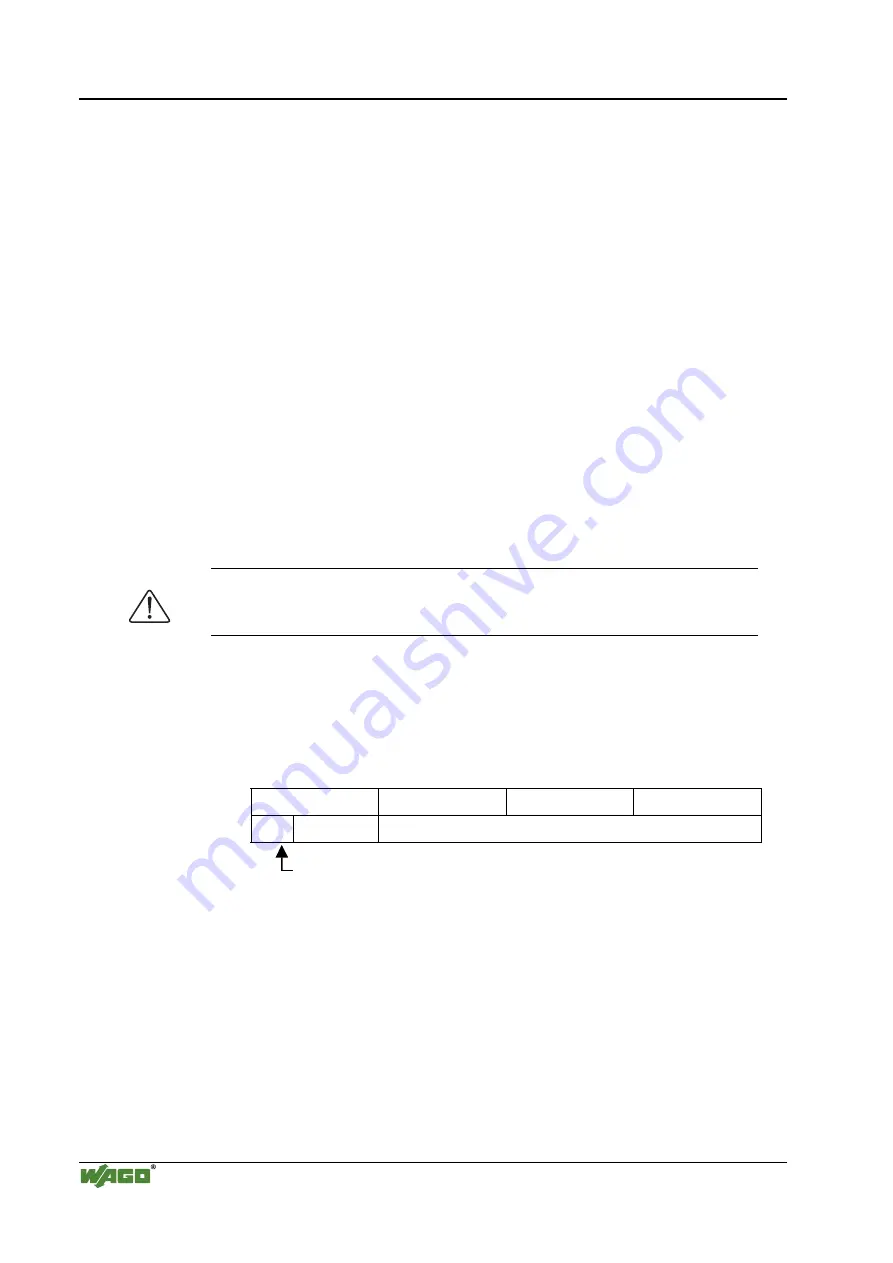
122
•
Fieldbus Communication
ETHERNET
WAGO-I/O-SYSTEM
750
PROFINET IO
However, this does not make data transmission reliable enough for industrial
requirements. To ensure that communication and data transmission via
ETHERNET is reliable, various communication protocols are required.
4.1.3.3.1
IP-Protocol
The Internet protocol divides datagrams into segments and is responsible for
their transmission from one network subscriber to another. The stations
involved may be connected to the same network or to different physical
networks which are linked together by routers.
Routers are able to select various paths (network transmission paths) through
connected networks, and bypass congestion and individual network failures.
However, as individual paths may be selected which are shorter than other
paths, datagrams may overtake each other, causing the sequence of the data
packets to be incorrect.
Therefore, it is necessary to use a higher-level protocol, for example, TCP to
guarantee correct transmission.
IP addresses
To allow communication over the network each fieldbus node requires a 32 bit
Internet address (IP address).
Attention
Internet addresses have to be unique throughout the entire interconnected
networks.
As shown below there are various address classes with net identification (net
ID) and subscriber identification (subscriber ID) of varying lengths. The net
ID defines the network in which the subscriber is located. The subscriber ID
identifies a particular subscriber within this network.
Networks are divided into various network classes for addressing purposes:
•
Class A:
(Net-ID: Byte1, Host-ID: Byte2 - Byte4)
e.g.:
101 . 16 . 232 . 22
01100101
00010000
11101000
00010110
0
Net-ID
Host-ID
The highest bit in Class A networks is always ‘0’.
Meaning the highest byte can be in a range of
’0 0000000’ to ‘0 1111111’.
Therefore, the address range of a Class A network in the first byte is always
between 0 and 127.