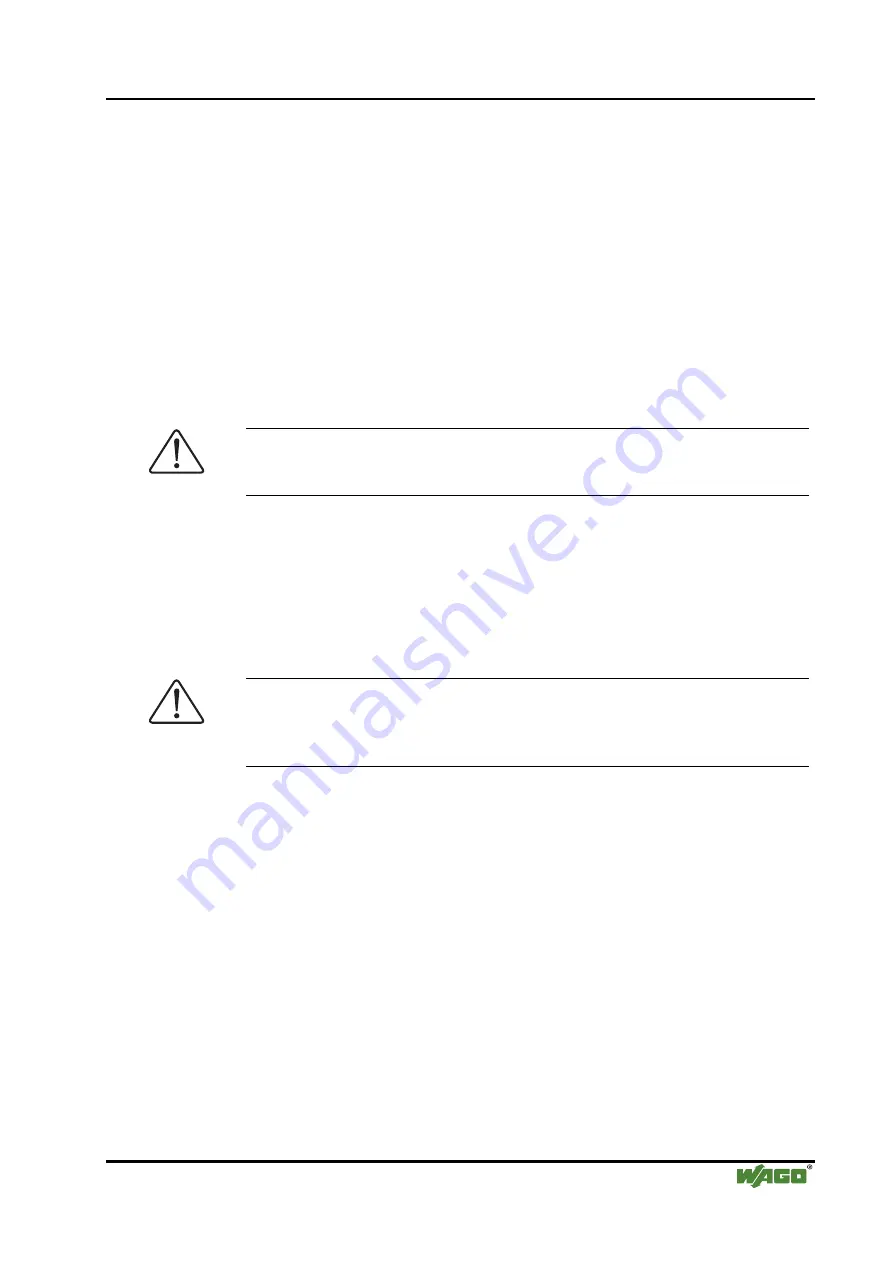
Programmable Field Bus Controller 750-833
•
61
Process Image
WAGO-I/O-SYSTEM 750
Bus System
3.4 Process Image
3.4.1 Local Process Image
The process is mapped on the PROFIBUS with the module configuration. This
is the reason why this description is only important for programming the
controller with
WAGO-I/O-
PRO
.
After power-up, the controller recognizes all I/O modules connected in the
node (data width/bit width > 0). Analog and digital I/O modules can be mixed.
The controller generates an internal local process image from the data width
and the type of I/O module as well as the position of the I/O modules in the
node. This is divided into an input and an output area.
Attention
For the number of input and output bits or bytes of the individual I/O
modules please refer to the corresponding description of the I/O modules.
The data of the I/O modules is separated for the local input and output process
image in the sequence of their position after the controller in the individual
process image.
First of all, the byte-orientated bus terminals are filed in the process image and
then the bit-orientated. The bits of the digital terminals are combined into
bytes. If the number of digital I/Os is greater than 8 bits, the coupler
automatically begins another byte.
Attention
If a node is changed or extended this may result in a new process image
structure. In case of an extension the process data of all previous clamps is to
be considered.
In addition, the data of the PFC variables are separated according to input and
output data and put into the process image of the controller.