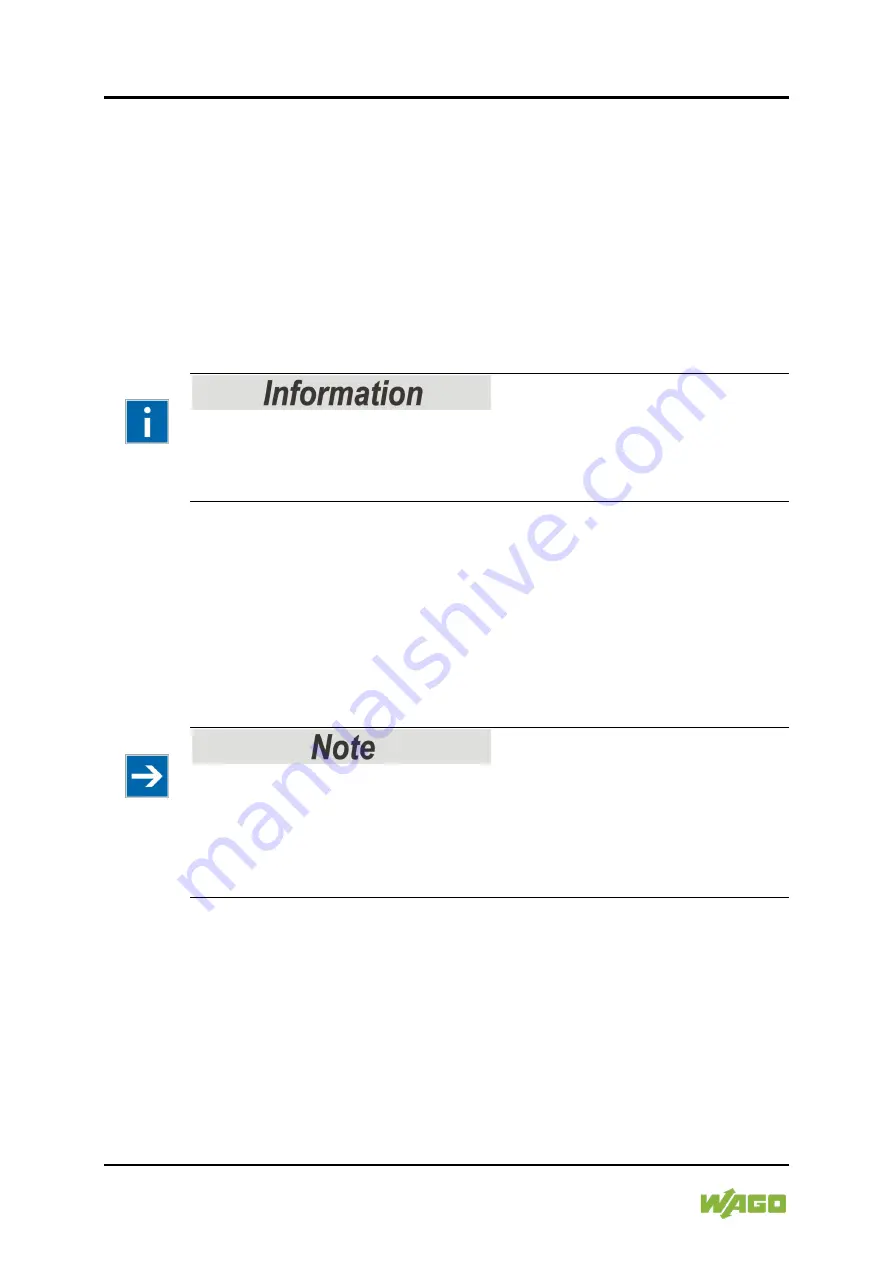
72 Function Description
WAGO-I/O-SYSTEM 750
750-325 CC-Link Fieldbus Coupler
Manual
Version 2.0.1
7.2
Process Data Architecture
The following sections provide a glimpse of the internal functioning, data
processing and addressing in CC-Link communication.
7.2.1
Basic Setup
After switching on the fieldbus coupler, it identifies all I/O modules of the node
that send or expect to receive data (data/bit width > 0). Any number of analog
input/output modules and digital input/output modules can be arranged within a
node.
Additional Information
For the fieldbus-specific structure of the process values of any I/O module within
the 750 or 753 Series of the WAGO-I/O-SYSTEM, refer to Section “I/O modules”
>> “Structure of process data for CC-Link“.
The coupler creates an internal local process image on the basis of the data
width, the type of I/O module and the position of the module in the node. This
process image is separated into input and output data range.
For both, the local input and output process image, the I/O module data is stored
in the corresponding process image depending on the order in which the
modules are connected to the coupler.
Hardware changes can result in changes of the process image!
If the hardware configuration is changed by adding, changing, removing or
reparametrisation of I/O modules with a data width > 0 bit, this result in a new
process image structure. The process data addresses would then change. If
adding I/O modules, the process data of all previous I/O modules has to be taken
into account.
7.2.2
Address Areas of the CC-Link Fieldbus Coupler
7.2.2.1 Address Area Overview
Depending on the configuration, a CC-Link slave can occupy up to four stations
(occupied stations). In addition, in the setting of the CC-Link specification V2.0,
the extended cyclic setting can be selected with 1, 2, 4 or 8 cycles for data
transmission.