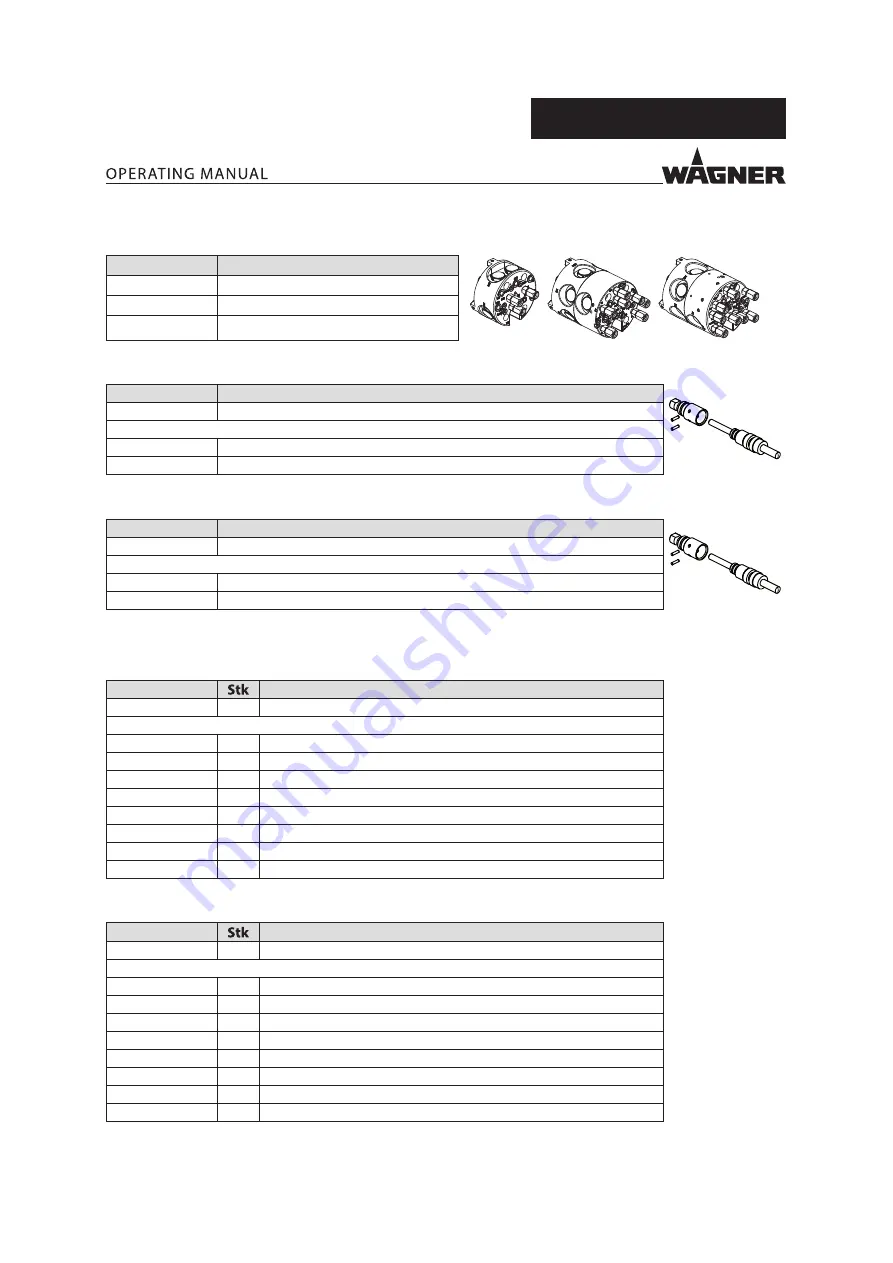
65
VERSION 01/2018
ORDER NUMBER DOC 2385674
TOPFINISH Bell 1S
14.6 VALVE BLOCKS
Order no.
Description
B_06866
1
2
4
2372279
Valve block M/DM/FB (1-paint)
2391613
Valve block 2C (2-paints)
2391617
Valve block 4C (4-paints)
14.7 OPTICAL FIBER 9.9 M WITH SLEEVE
Order no.
Designation
B_06679
2383286
Optical fiber 9.9 m with sleeve
Consists of:
2335584
Optical fiber 9.9 m
2382097
Sleeve for optical fiber, complete
14.8 OPTICAL FIBER 15 M WITH SLEEVE
Order no.
Designation
B_06679
2383289
Optical fiber 15 m with sleeve
Consists of:
387101
Optical fiber 15 mm
2382097
Sleeve for optical fiber, complete
14.9 HOSE SETS
14.9.1 AIR HOSE SET, 10 M
Order no.
Designation
2373986
Air hose set, 10 m
consisting of:
700370
5
Hose PU ø 8/5.5 mm blue 10 m
700371
1
Hose PU ø 6/4 mm blue 10 m
2348719
4
Hose PEN ø 4/2.7 mm blue 10 m
2383812
1
Wire labeling
3051200
2
Cable tie 360x4.8 mm
3051199
2
Cable tie 140x3.6 mm
9982016
1
Protective hose 9m
2335584
1
Optical fiber 9.9 m
14.9.2 AIR HOSE SET, 15 M
Order no.
Designation
2373994
Air hose set, 15 m
consisting of:
700370
5
Hose PU ø 8/5.5 mm 15 m
700371
1
Hose PU ø 6/4 mm blue 15 m
2348719
4
Hose PEN ø 4/2.7 mm blue 15 m
2383812
1
Wire labeling
3051200
2
Cable tie 360x4.8 mm
3051199
2
Cable tie 140x3.6 mm
9982016
1
Protective hose 14m
387101
1
Optical fiber 15 mm