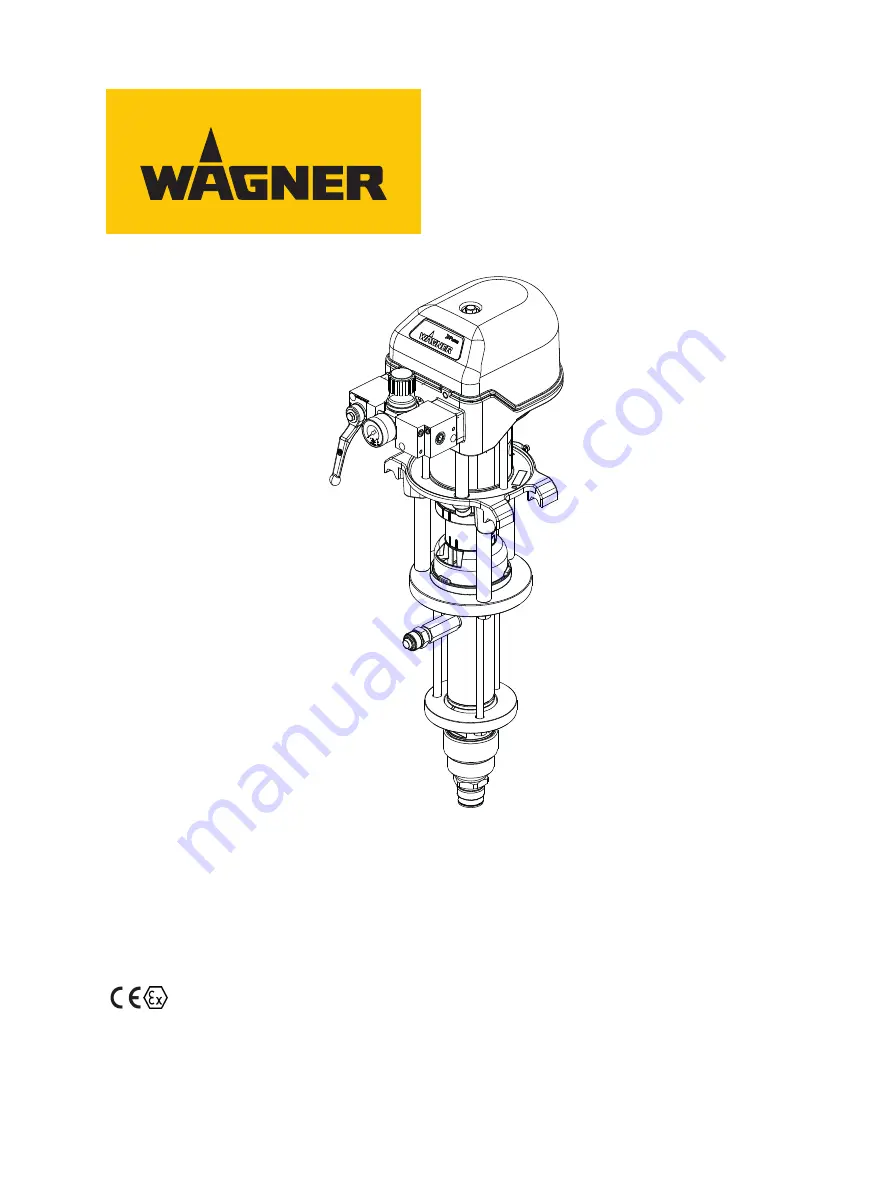
B_06985
Piston pump
IceBreaker 40-200 ccm (Finishing)
Translation of the original operating manual
II 2 G Ex h IIB T3/T4 Gb X
For professional use.
Always observe the information in this manual, particularly the safety
instructions and the warning instructions. Store the manual in a safe place.
Edition: 03/2021