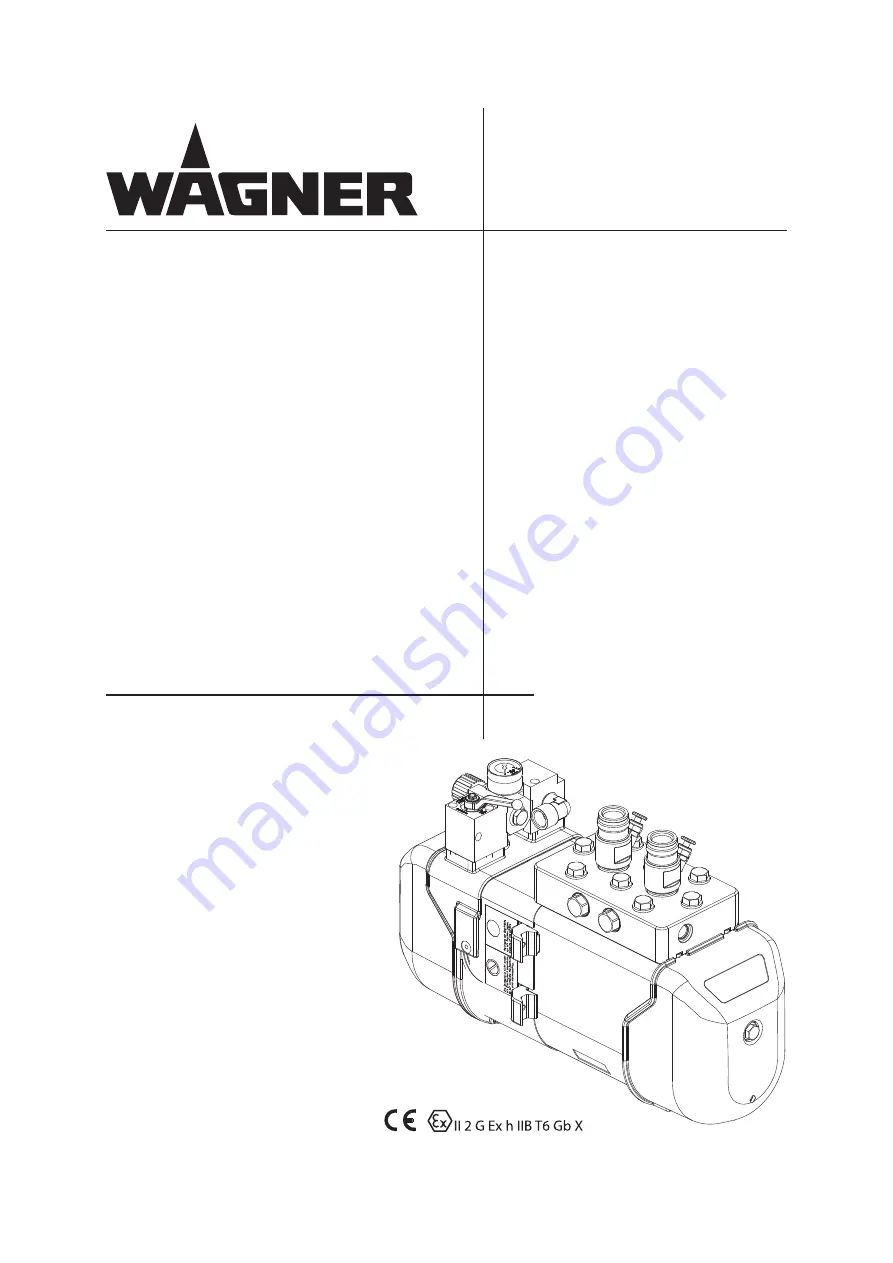
Translation of the Original
Operating Manual
For professional use.
Always follow the information in this manual,
particularly the safety instructions and the warning
instructions. Store the manual in a safe place.
Cobra 40-10 / 2K
High Pressure Double
Diaphragm Pump for
2-Component Products with
Mixing Ratio 1:1
Version 04/2018
B_5076
Summary of Contents for Cobra 40-10/2K
Page 2: ......