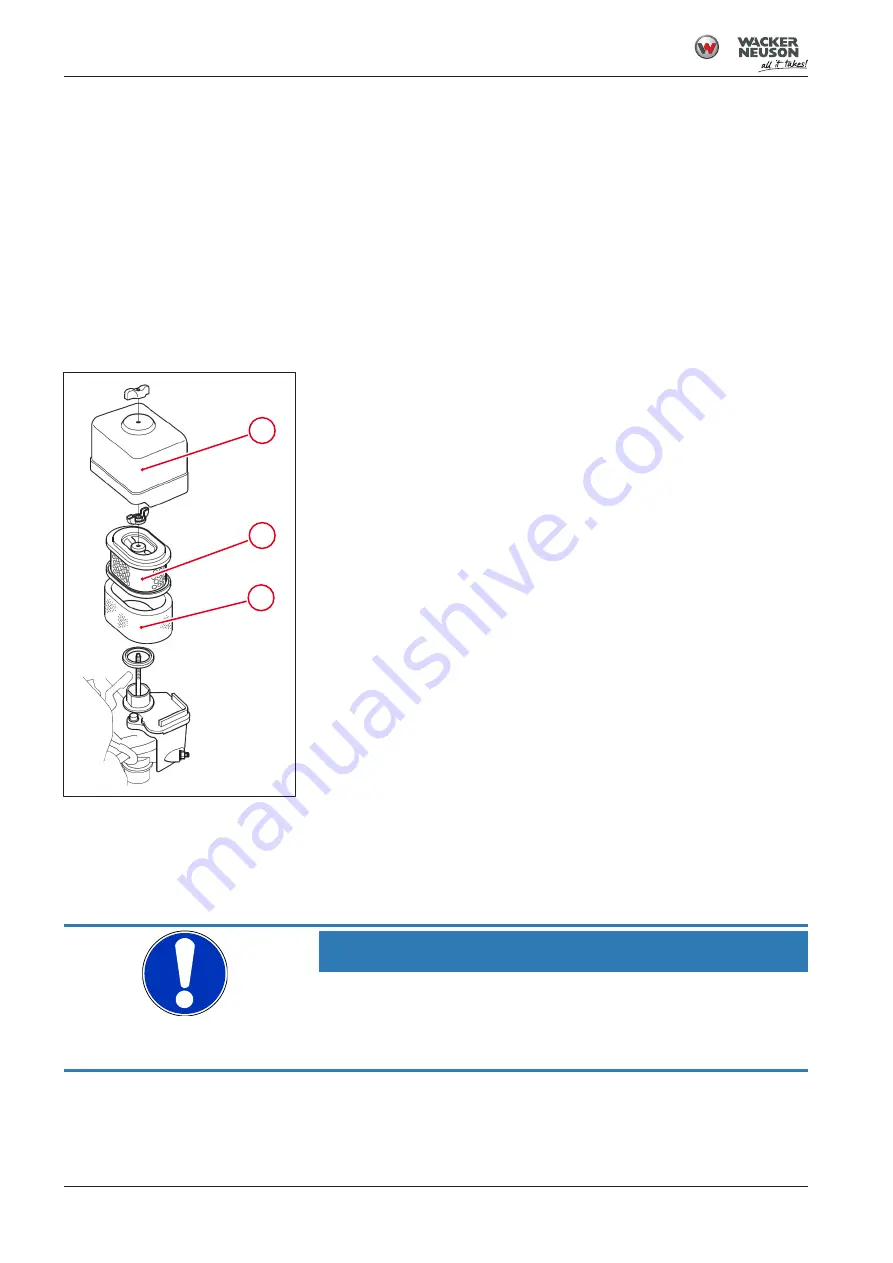
Maintenance
9.3 Maintenance work
34
Operator’s Manual | BPS | 5100060589 | 07/2021 | [us]
9.3.2
Checking and topping up the fuel level
1.
Remove dirt.
2.
Open tank lid.
3.
Check the fuel level.
ð
Max. fuel level to lower edge of filler neck.
4.
Refuel if necessary,
see Technical Data on page 42
.
5.
Close tank cap tightly.
9.3.3
Cleaning and checking the air filter
1
2
3
1.
Remove air filter lid
1
.
2.
Remove and separate the air filter inserts.
ð
Paper filter insert
2
and foam filter insert
3
3.
Check both air filter inserts for cracks and holes, replace if dam-
aged.
Cleaning the paper filter insert
1.
Knock out filter insert on hard surface.
2.
Blow with compressed air from the inside through the filter insert.
ð
Do not brush out, this will force dirt into the fibers.
ð
Replace if heavily soiled.
Cleaning the foam filter insert
1.
Wash the filter insert in soapy water.
2.
Rinse thoroughly with water.
3.
Leave to dry.
4.
Immerse in new engine oil,
see Technical Data on page 42
.
5.
Press out the filter insert.
ð
Excess engine oil will smoke when the engine is started.
9.3.4
Checking and topping up engine oil level
NOTICE
Danger of engine damage!
►
Only change the oil when the engine is at operating temperature.
►
Only use engine oil with the correct specification,
on page 42
.